Notes
The term CMC is generic and refers to organic sodium carboxymethylcellulose. In ceramics, this material is added to glazes, colors and enamels. As percentages are increased CMC gum makes slurries stickier and slower drying (these properties increase exponentially with percentage added). In industry, where ware exiting driers can be quite hot, slowing down drying is important to maintain at least some moisture to improve adhesion of the next layer (of engobe, glaze, grit, etc).
CMC gum is organic, so microorganism attack can affect slurry rheology (so an anti-microbial might be needed). Also, note that organics generate gases on firing, these can produce glaze defects.
CMC gum is commonly used in glaze slurries to improve dry hardness and adherence to the bisque. It is especially important in brushing glazes for another reason: Slower drying. Gum is an important addition to over-glaze colors applied by stamping or painting, it gives them a paint-like consistency. Gum is important in transparent glazes that need to adhere and spread evenly over underglaze decoration. Highly fritted glazes benefit most from gum additions because they lack clay content to harden and suspend them. Conversely, with a gum addition, high-clay glazes that would otherwise crack on drying (and thus crawl during firing) can dry without problems and adhere to bisque. Single-layer dipping glazes that have natural hardening properties, because they contain 15% or more clay, normally do not need gum additions (unless there is a need to slow down the drying speed). Base coat glazes (applied by dipping and covered with subsequent layers) need gum to firmly adhere them to the bisque (to prevent being lifted because of the shrinking of subsequent layers). In production situations, it is wise to tune the percentage of CMC to be minimal, enough to provide adherence but not slow down drying too much.
When enough CMC gum is present it becomes the dominant factor determining slurry rheology, even negating the effects of other rheology modifiers. A glaze that formerly relied on water content to control viscosity will likely require a specific gravity adjustment when CMC gum is added (often less water).
Powdered gum can be very difficult to disperse in water (addition-as-a-powder to an existing slurry is almost impossible). While it is possible to mix gum powder with other dry ingredients before adding them to the water (often 0.5-1.5%) a much more effective method is to make a gum solution (gumsol) and replace part of the water with it when making a batch. Make the solution by boiling water and mixing in the powder vigorously with a mechanical mixer (it should thin out over time). What percentage of gum should be in a gum solution? We use Laguna Gum Solution, it works well and contains 67 grams of powdered gum per litre (as well as an antimicrobial preservative).
The amount of solution needed in a glaze must then be calculated to source the amount of gum powder desired. We find that about a 5:95 gumsol:water mix is good for our G2926B base coat dipping glaze, but this amount does not necessarily apply to others (testing is needed to be sure the gum amount is not excessive). Brushing glazes are at the opposite extreme, requiring as high as 20:80 gumsol:water. It is normal to allow a glaze slurry to settle and remove an amount of water equal to the amount of gumsol being added. That being said, gumsol may thin the slurry, so it might be better, for example, to remove 200g of water and replace with 100g of gumsol.
Do not substitute something else just because it has the word "gum" in its name. VeeGum T, for example, is a refined plastic clay, a completely different type of material (CMC gum is a glue, Veegum T is a high surface area clay that encourages gelling in glaze slurries lacking fine-particled clay in their recipes).
There are reasons to use a mix of VeeGum T and CMC Gum. For example, it is often advantageous for brushing glazes to have a low specific gravity (e.g. 1.3), however such high-water-content slurries are like water. Veegum T acts as a thickener and CMC gum a hardener. There is a material named "Veegum CER", it is a mix of CMC and Veegum T, it is used for just such a purpose. Since VeeGum CER thickens or gels the slurry, it is practical to add it, in solution, to an existing dipping glaze (without having to remove the same amount of water). A VeeGum Cer addition can mean that more water is also needed to get the degree of gelling needed.
CMC gum trade name examples are Aqualon from Hercules, Gabrosa from Alzo Nobel.
Related Information
Here is my setup to make brushing glazes and underglazes by-the-jar
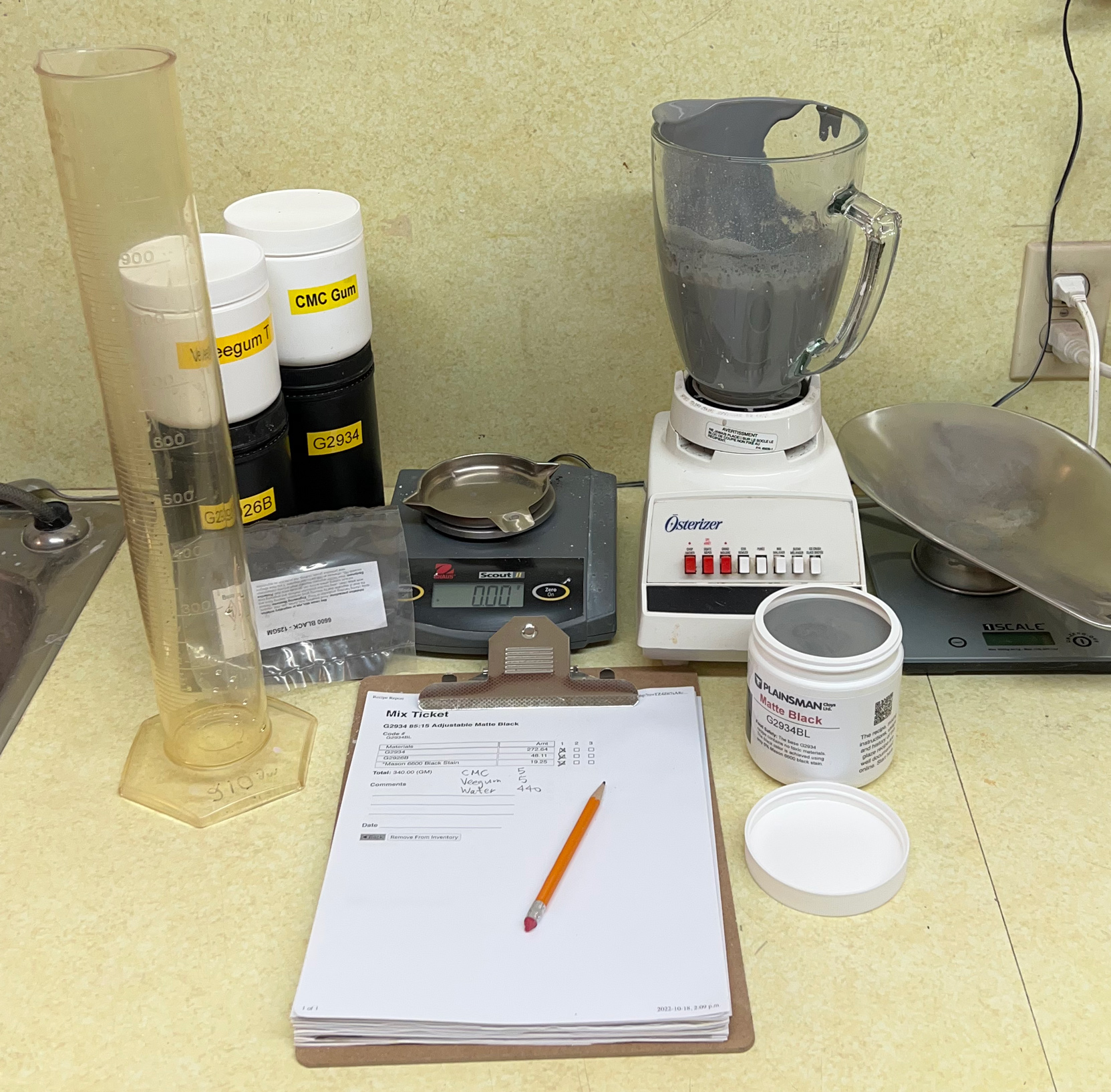
This picture has its own page with more detail, click here to see it.
Although I promote DIY dipping glazes, you can also make DIY brushing glazes. Let's make a low SG version of G2934BL. Weigh out a 340g batch of dipping glaze powder. Include 5g Veegum (to gel the slurry to enable more than normal water) and 5g CMC gum (to slow drying and impart brushing properties). Measure 440g of water initially (adjusting later if needed). Shake-mix all the powder in a plastic bag. Pour it into the water, which is blender mixing on low speed, and finish with 20 seconds on high speed. This just fills a 500ml jar. In subsequent batches, I adjust the Veegum for more or less gel, the CMC for slower or faster drying and the water amount for thicker or thinner painted layers. Later I also assess whether the CMC gum is being degraded by microbial attack - often evident if the slurry thins and loses its gel. Dipping glaze recipes can and do respond differently to the gums. Those having little clay content work well (e.g. reactive and crystalline glazes). If bentonite is present it is often best to leave it out. Recipes having high percentages of ball clay or kaolin might work best with less Veegum. Keeping good notes (with pictures) is essential to reach the objective here: Good brushing properties. We always use code-numbering (in our group account at Insight-live.com) and write those on the jars and test pieces. This is so worthwhile doing that I make quality custom labels for each jar!
Common dipping glazes converted to jars of high SG brushing
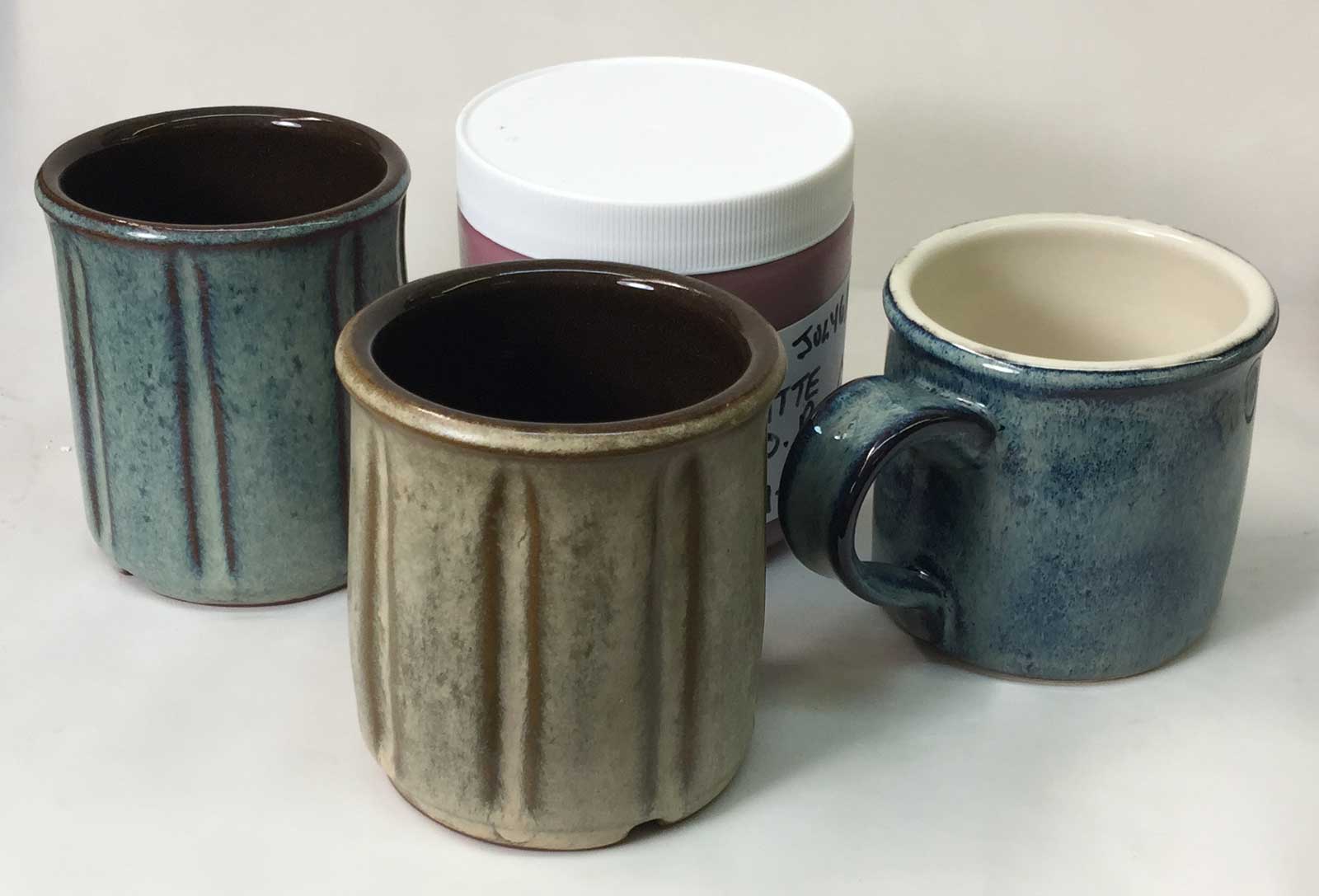
This picture has its own page with more detail, click here to see it.
These are cone 6 Alberta Slip recipes that have been brushed onto the outsides of mugs (three coats gave very thick coverage). Recipes are GA6-C Rutile Blue on the outside of the left mug, GA6-F Alberta Slip Oatmeal on the outside of the center mug and GA6-F Oatmeal over G2926B black on the outside of the right mug). These one-pint jars were made using 500g of powder, 280g of water and 75g of Laguna CMC gum solution (equivalent of adding 1% powdered CMC). Because no Veegum is being used this blender mixes to a slurry of high 1.6 specific gravity (for thicker coverage per coat than commercial glazes having much more water). This approach is good for recipes high in Alberta Slip. The gum removes the need for roasting part of it, reduces the water needed and the plasticity of the Alberta Slip helps suspend the slurry.
Add CMC gum to a dipping glaze slurry for brushing
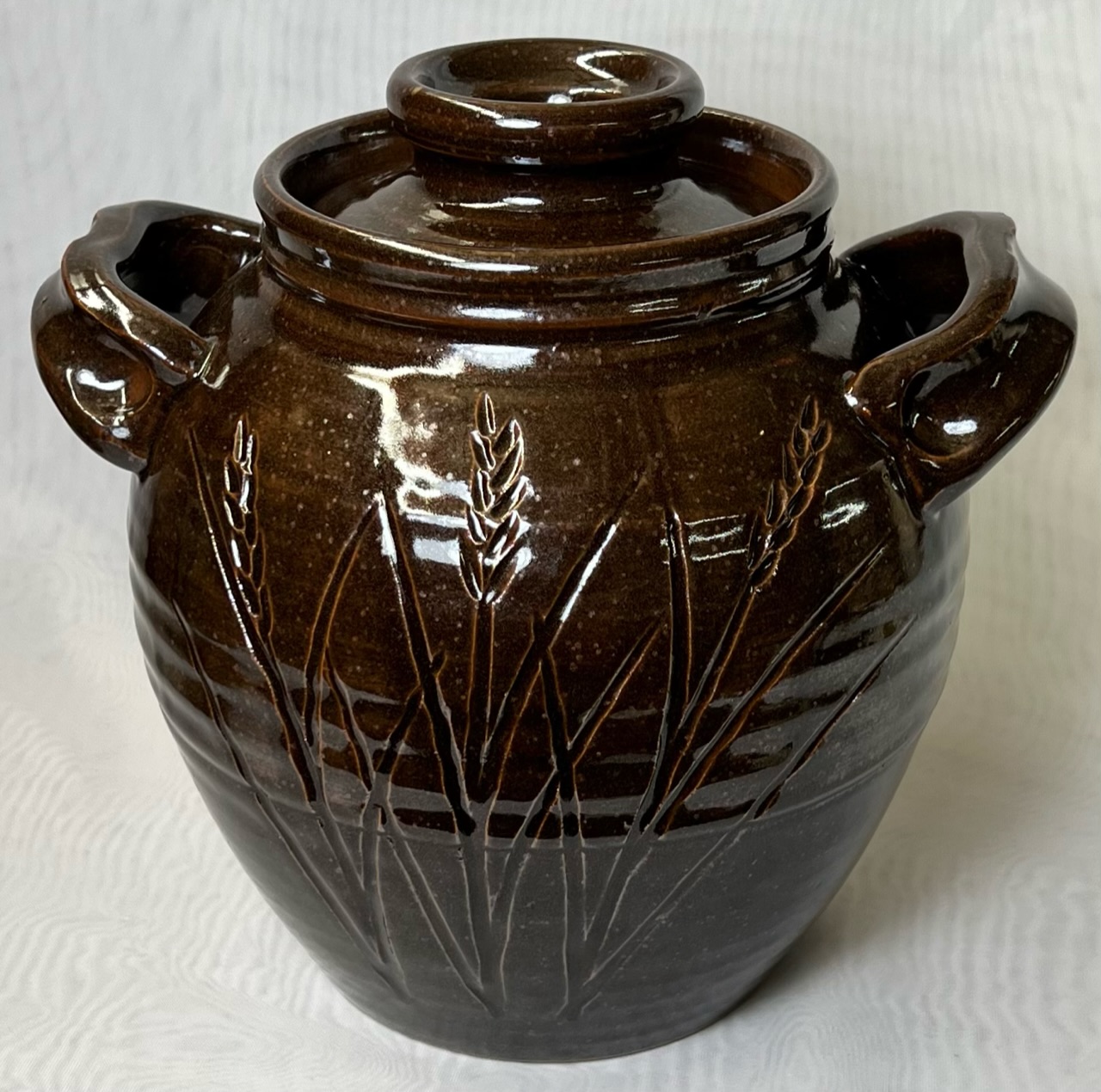
This picture has its own page with more detail, click here to see it.
The outsides of these reduction-fired bean-pots are a unique challenge to glaze evenly and drip-free using dipping or pouring (also, a much thinner layer is needed inside the flange). A gummed brushing glaze is a solution. But how can one convert a cup of dipping glaze into a brushing glaze? CMC gum powder - it slows down drying and imparts brushing properties. Since our dipping glazes are about 50:50 water:powder, I blender-mixed 3.75g CMC gum powder into 1000g of slurry to get ~0.75% concentration (depending on your mixer it might require more). Triple-layer brush-glazing this piece takes about five minutes. I use two brush types (fan and hake) and different techniques for each zone. It dries really hard. If the gum over-thins your glaze, a water-reduced version is needed. Assuming it has settled somewhat pour off or sponge off some of the water and add the CMC gum to that. Don’t forget, it has to be blender mixed.
Veegum is not a gum, it is a gelling agent. CMC gum needs something it provides.
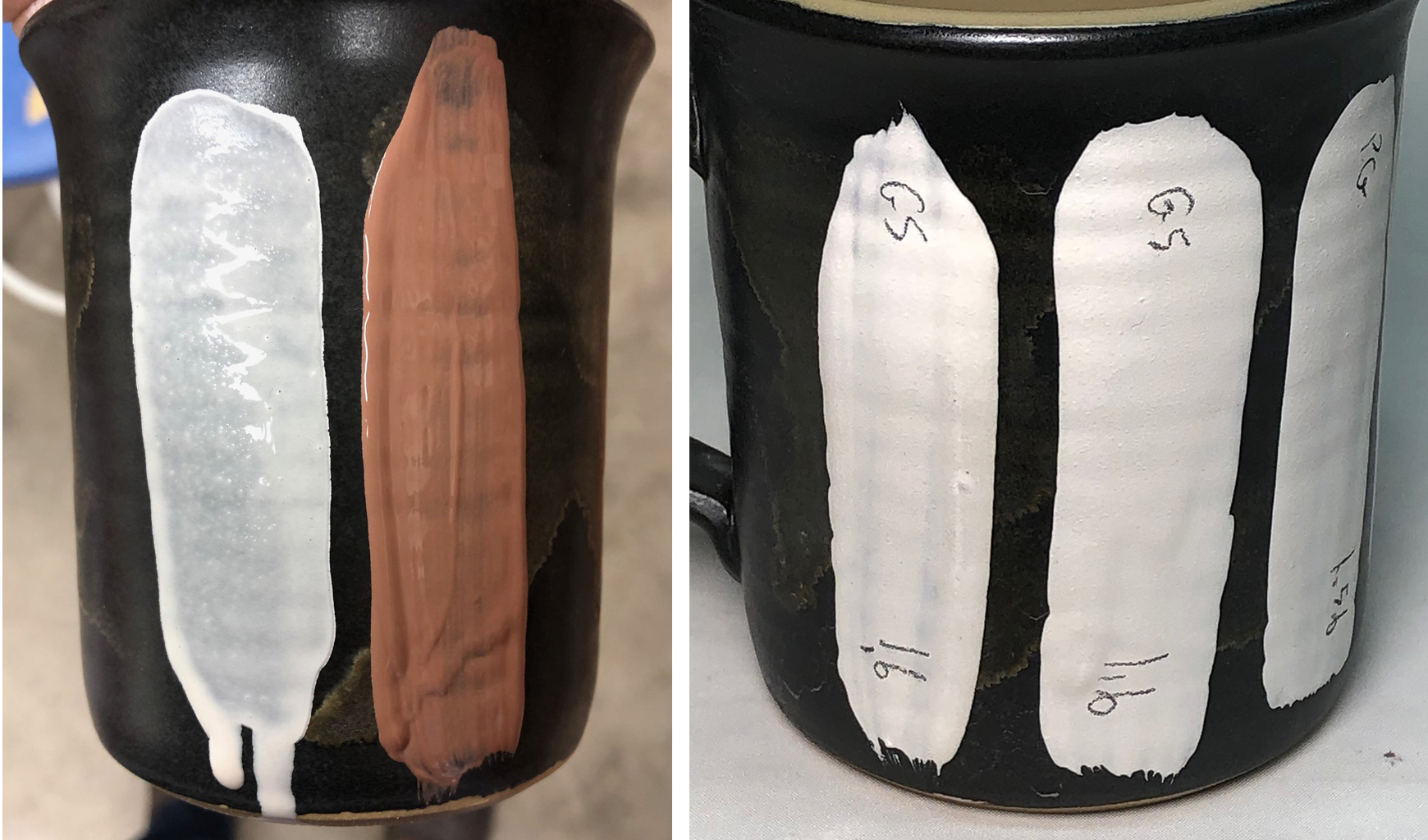
This picture has its own page with more detail, click here to see it.
On the left, the brush-strokes of gummed glaze, which I batched myself, have been freshly painted onto an already-fired glaze. Notice the brown brush stroke holds its character. It has a high specific gravity (SG): 1.6. And contains 1.5% CMC gum. The white one to its left, whose brush stroke has flattened and it is running downward, has the same gum content but an SG of 1.5. Is it running because of its lower SG? No. Commercial glazes with an SG below 1.3 still hold in place well. How? Because they also have a gelling agent (e.g. Veegum - it has an unfortunate name, it is not a gum). That reveals a secret: Gums and gelling agents need each other. CMC Gum needs particle surface area to work its magic and bentonite, the gelling agent here, supplies that. And, the gelling agent needs the gum to slow down drying and enable a hard and crack-free dried surface. The dried strokes on the right demonstrate that - 2% bentonite has been added to the drippy one on the far left. They held in place because of the bentonite and hardened without cracking because of the CMC gum.
This serious glaze crawling problem was solved with a simple addition
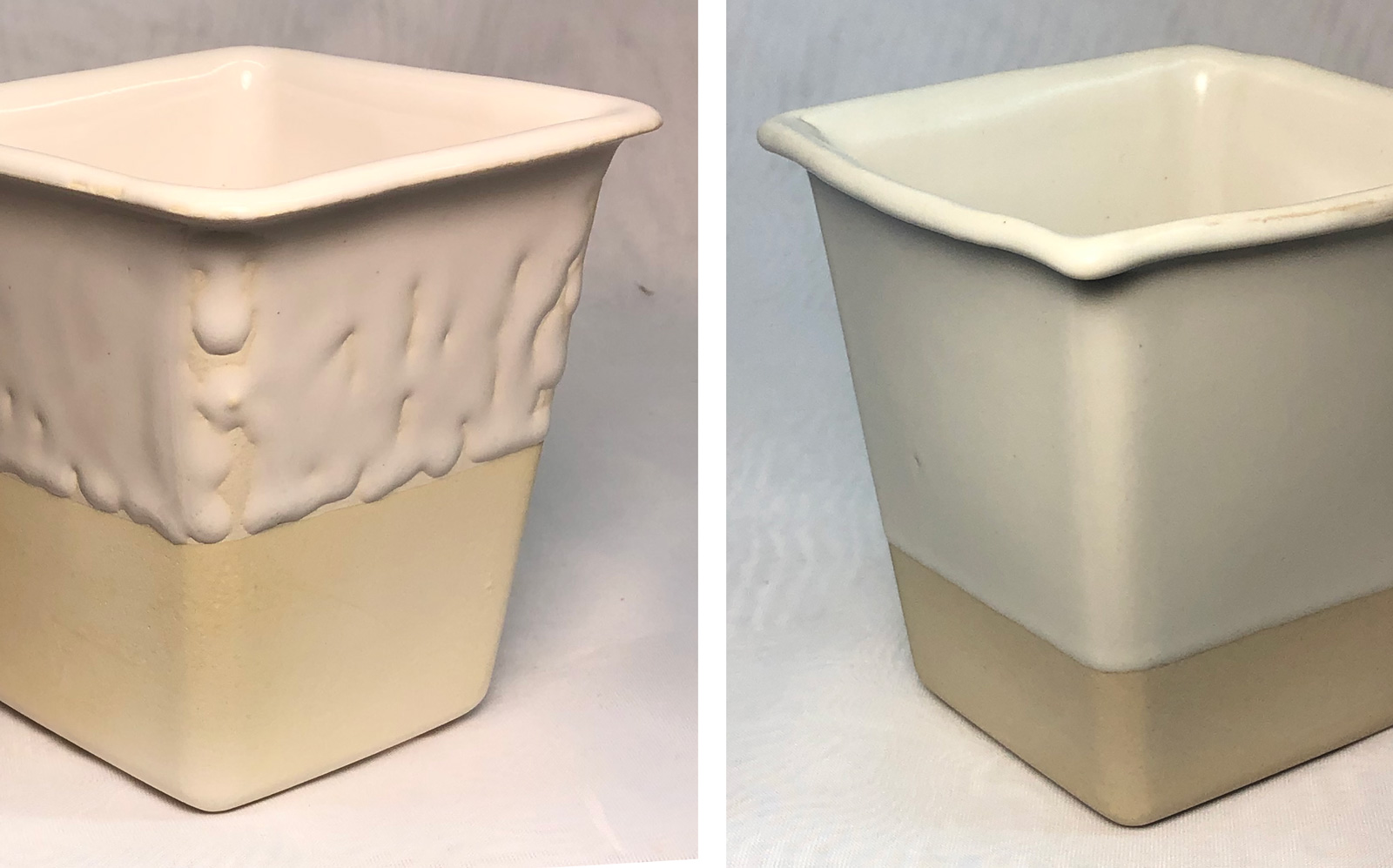
This picture has its own page with more detail, click here to see it.
This is G2934Y white (with 10% Zircopax). I initially blamed the zircon for the crawling. But, since the slurry had settled somewhat I was able to remove about 15% of the water and replace it with CMC gum solution. The gum addition was not enough to slow down the drying much but it really improved reduced the problem! This likely means that adherence of the dried layer to the smooth bisque was the issue. This being said, there were still a couple of small spots where it crawled. The ultimate solution thus appears to be discovering the percentage of CMC gum and water needed to get the least loss of drying speed and while achieving integrity of glaze coverage. It is best to add the CMC gum as a powder at mixing time and blender mix the slurry thoroughly to be sure that it fully dissolves (watch for a rheology change on aging, that will demonstrate if mixing was thorough enough).
Fixing a crawling problem with a measured CMC addition
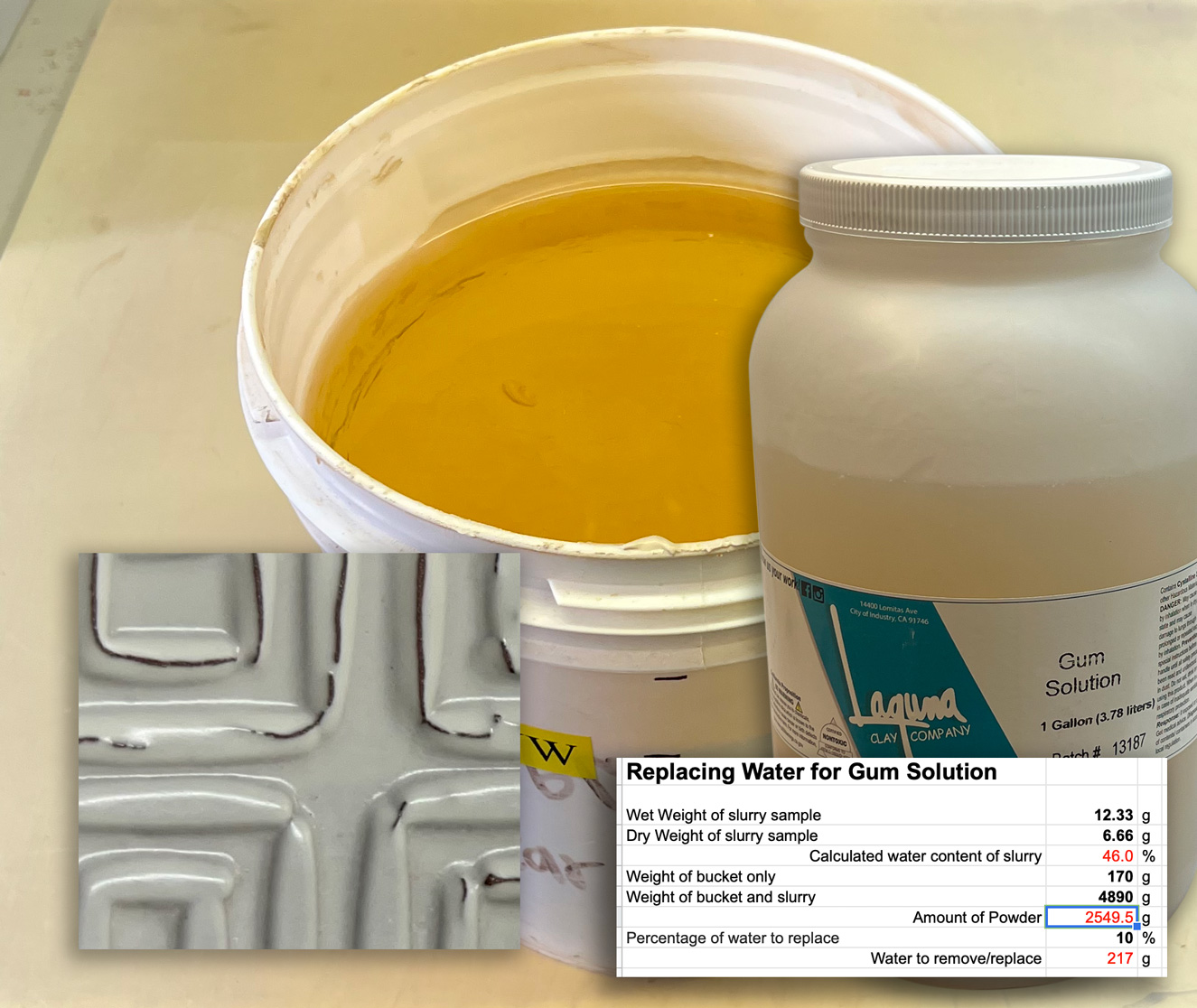
This picture has its own page with more detail, click here to see it.
The problem: This dipping glaze is crawling (as shown on the glazed tile). Let's assume I have already checked to make sure the specific gravity is right and the slurry is thixotropic. Because it has settled a little there is an opportunity for plan B: Remove some of the water and replace it with gum solution. Shown here is a precise calculation of the exact water content of the slurry to replace 10% of the water with gum solution. But it is better to take a more conservative and easier approach: Replace one-twentieth of the water with gum solution (too much gum and the glaze will drip excessively and dry too slowly). Rather than be overly precise let's just guess: I have 5000g of slurry that is about 50% water, so that is 2500g of powder, so I need to remove 125g of water and replace it with 125g of Laguna gum solution. A good way is to use a sponge: Wet and wring it out first and then repeat touching it to the water surface and wringing it out into a container to get 125g. A propeller mixer is needed to mix in the added gum solution (it won't just stir in).
What should the consistency of CMC gum solution be?

This picture has its own page with more detail, click here to see it.
This is CMC gum 35g/liter gum solution after it has been thoroughly hot-mixed and cooled to about 30C. As it cools further and sits it thins. Gum solutions can have a higher CMC content, up to double this, but they are more difficult to use.
Most often, gum solution is intended to augment the water when batching a recipe - not adding to a glaze slurry. This is because adding enough to have any effect on an already-mixed glaze thins it (so an equal amount or more water should first be removed). For example, consider converting a dipping glaze to a brushing glaze: Adding the equivalent of 1.5% CMC gum powder, via this gum solution, to a gallon of glaze would also add almost a liter of water. Better to blender mix in the CMC power. CMC gum is often used in consort with a gelling agent like VeeGum, enabling more water (this is done in many commercial bottled glazes).
CMC gum solutions can go bad

This picture has its own page with more detail, click here to see it.
That is why glazes containing CMC often need a biocide if they are going to be stored for extended periods. We made this one. The gallon jar of Laguna gum solution sitting next to this did not go bad, that means they have added some sort of anti-microbial agent.
How much CMC gum powder is in the gum solution you buy?
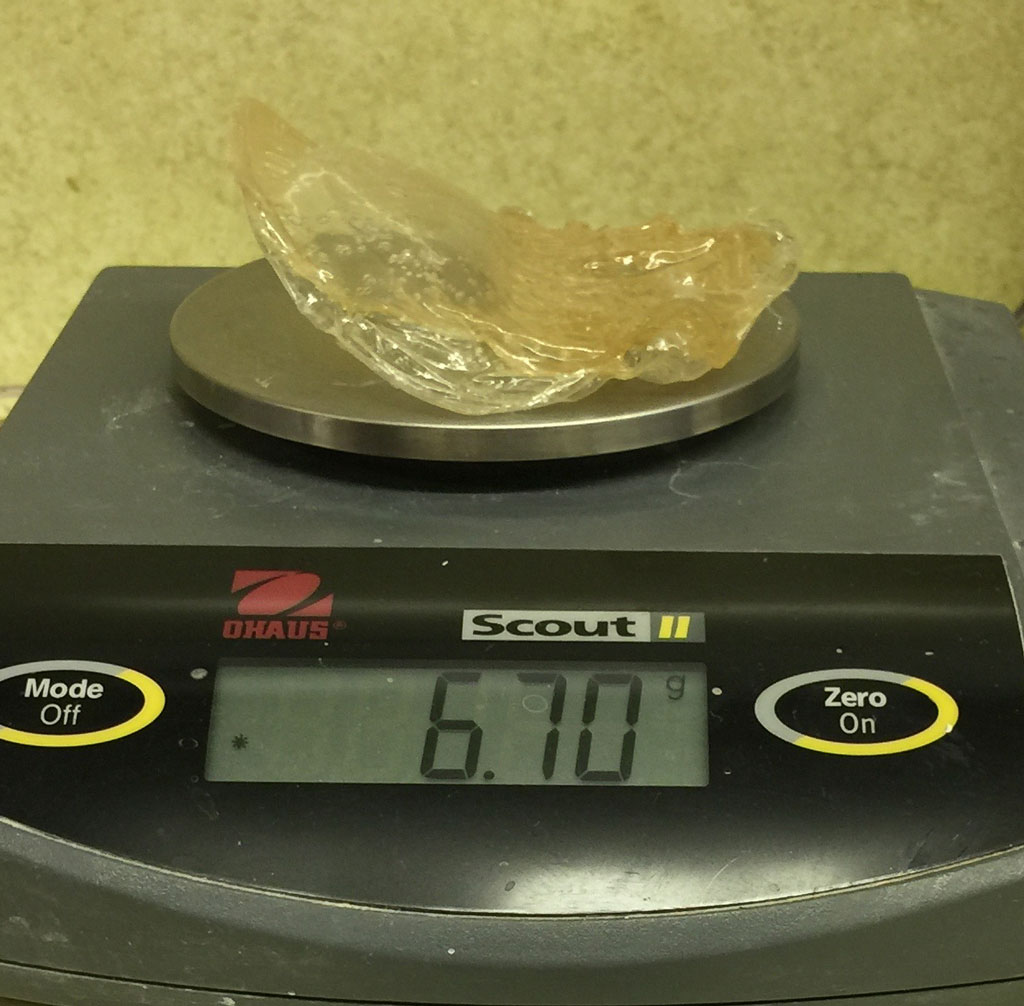
This picture has its own page with more detail, click here to see it.
We dried out 100 ml of Laguna gum solution and were left with this residue on the bottom of the container, 6.7g. Thus, a liter contains 67g. What if you need 10g of gum to achieve a 1.5% concentration in a liter of typical dipping glaze? That would be 10/0.067=149g. That liter of glaze thus has to be able to tolerate the addition of 140g of extra water without thinning too much (keep in mind that the gum also thins it).
Using boiling water and an hour of propeller mixing to make our own gum solution the highest practical level of CMC we can reach is 3.5%, it is not completely clear why.
Underglaze decoration difficult to cover with clear overglaze
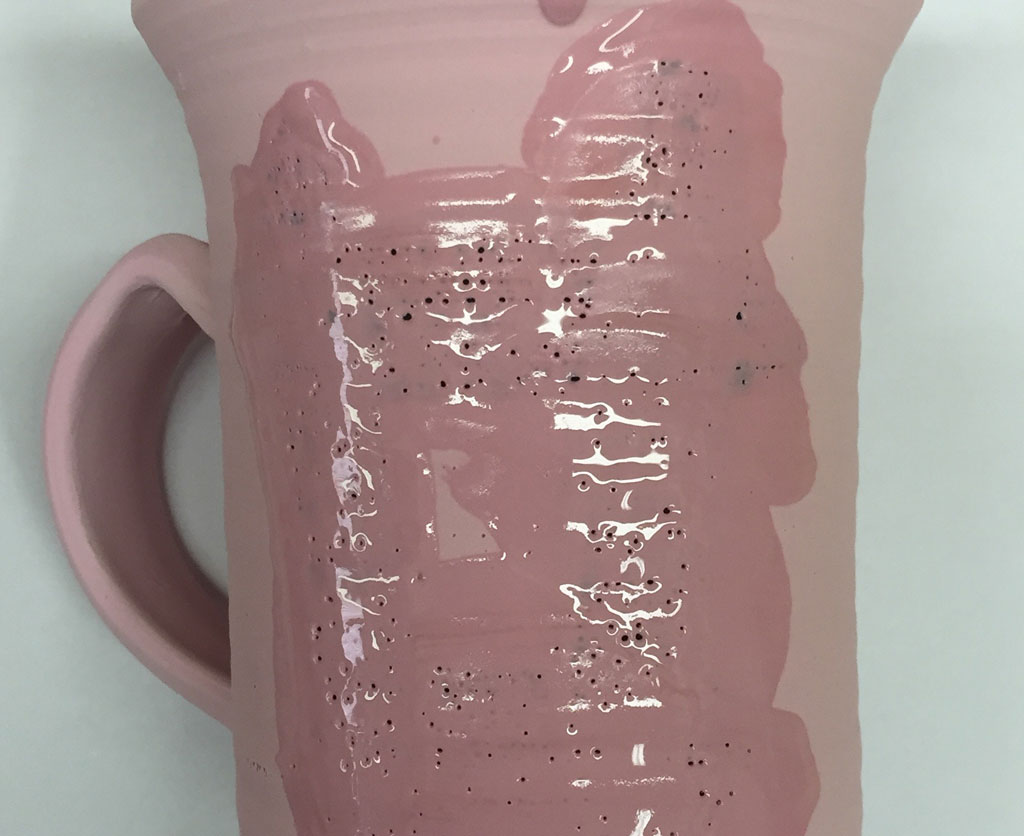
This picture has its own page with more detail, click here to see it.
The underglaze was painted on to bisque ware (has not be fired on). This is a problem. It has a high gum content and has sealed the surface so the porous body underneath is unable to pull water out to dry it quickly. During the slow dry the little absorption that is taking place is generating air bubbles from below and these are producing bare spots. The solution is to either make your own underglaze having a lower gum content or decorate ware in the dry or leather hard stage so the bisque fire will neutralize the gum.
CMC Gum is magic for multi-layering, even for raw Alberta Slip
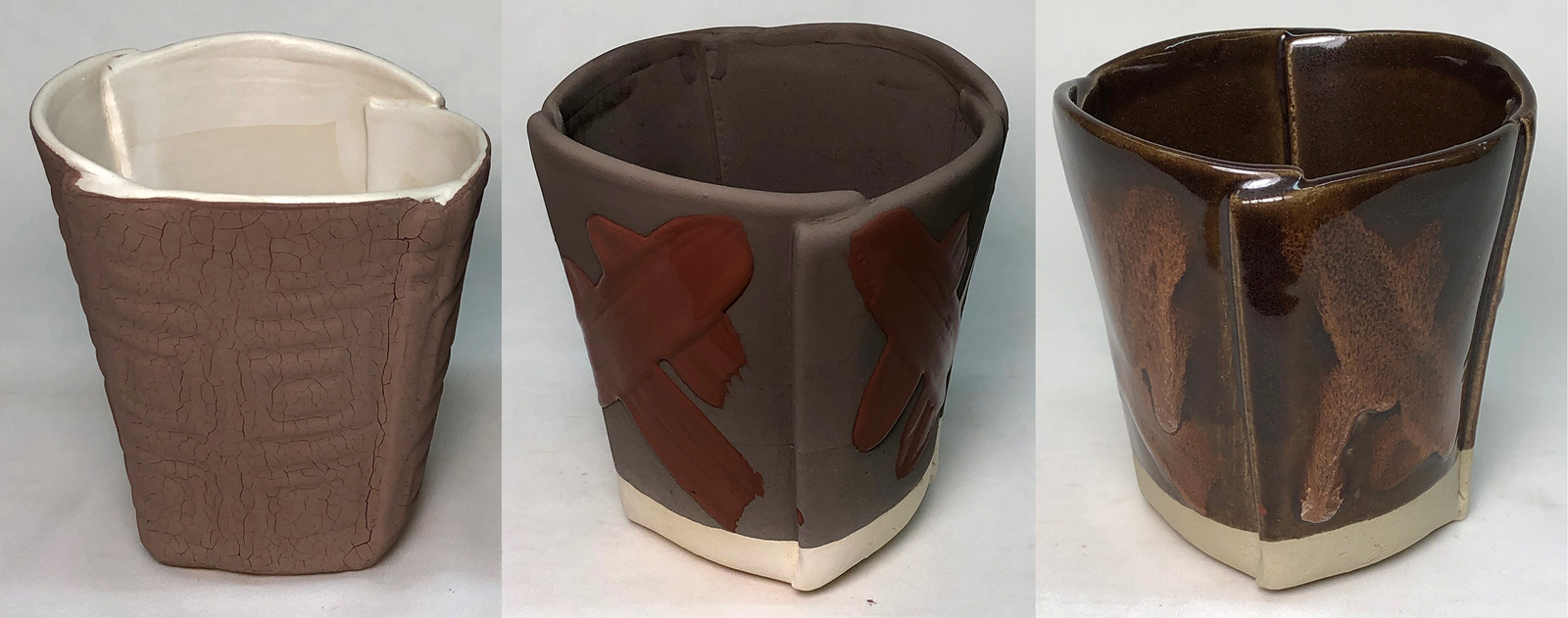
This picture has its own page with more detail, click here to see it.
The glaze on the left is 85% of a calcine:raw Alberta Slip mix (40:60). It was on too thick so it cracked on drying (even if not too thick, if others are layered over it everything will flake off). The center piece has the same recipe but uses 85% pure raw Alberta Slip, yet it sports no cracks. It should be cracked much worse than #1. How is this possible? 1% added CMC Gum (via a gum solution) was added! This is magic, but there is more. It is double-layered! Plus very thick strokes of a commercial brushing glaze have been applied over that. Yet no cracks. CMC is the secret of dipping-glazes for multi-layering. The downside: More patience during dipping, they drip a lot and take much longer to dry.
Six layers, 85% Alberta Slip in the glaze, yet no cracking. How? CMC gum.
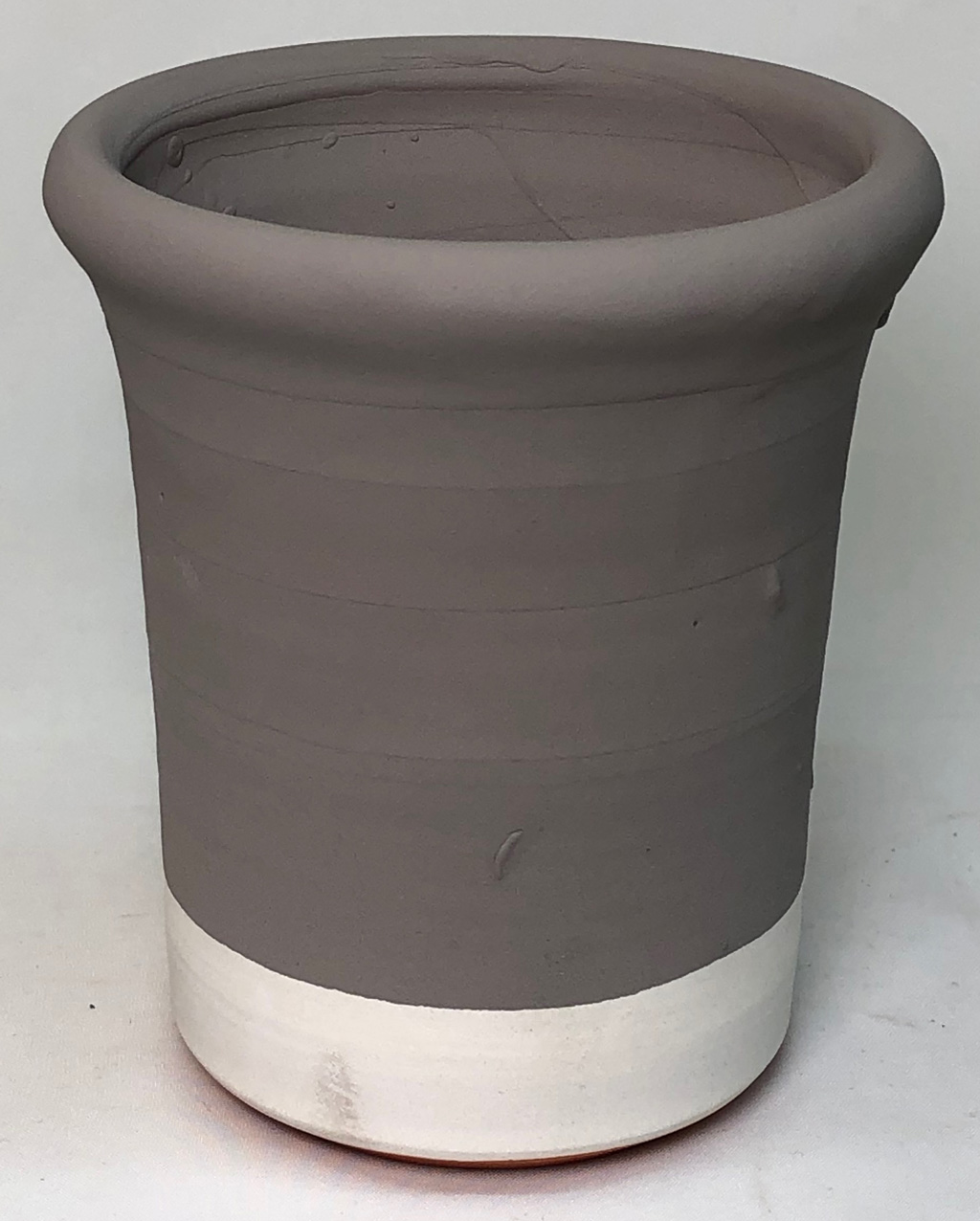
This picture has its own page with more detail, click here to see it.
Six layers of any normal dipping glaze would be impossible (flaking usually starts with the second). Yet this slurry is 85% plastic clay, it shrinks so much that it would be like a "dried-up lake bed" on the first layer. By the second it would all just fall off! How was it possible to dip six layers of this with no cracking? A 1% CMC gum addition added enough adhesive power to not only stick it on better but also counteract the drying shrinkage! Of course, there is a downside: A drying period is needed between each layer, the time depends on the porosity and wall thickness of the ware and the amount of gum. This also demonstrates the difference between the function of Veegum (and similar materials) with CMC. The former, if added to this recipe, would gel the slurry, require more water and increase the shrinkage, making the cracking much worse. We typically use a mix of calcine:raw Alberta Slip to control drying shrinkage enough to enable crack-free application for one coat (without CMC). But, as a first coat dipping glaze, a CMC addition is required.
CMC gum in the water is preventing this powder from slaking
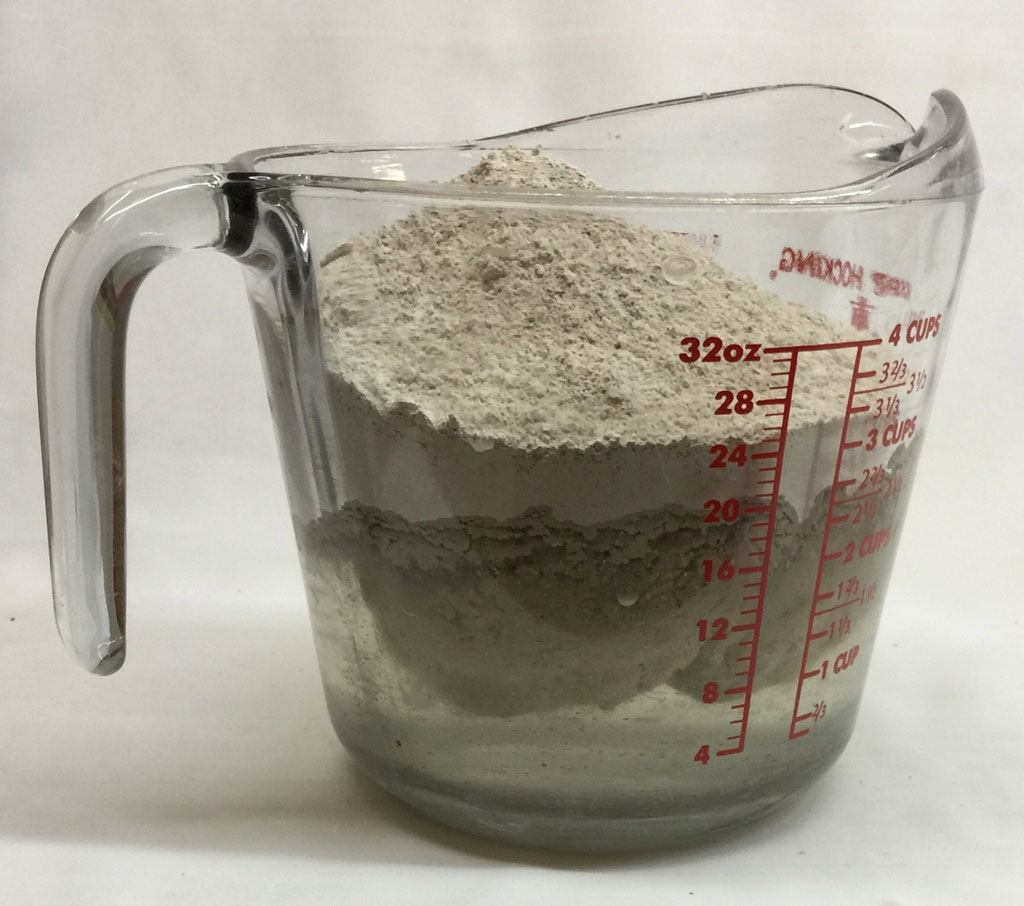
This picture has its own page with more detail, click here to see it.
Normally the powder would slake and settle to the bottom immediately. Mixing this requires a powerful mixer and plenty of time to remove all the lumps. The proportion of gum in the water amounts to 1.5% the total weight of the powder in the glaze.
CMC Gum ruined a batch of this glaze
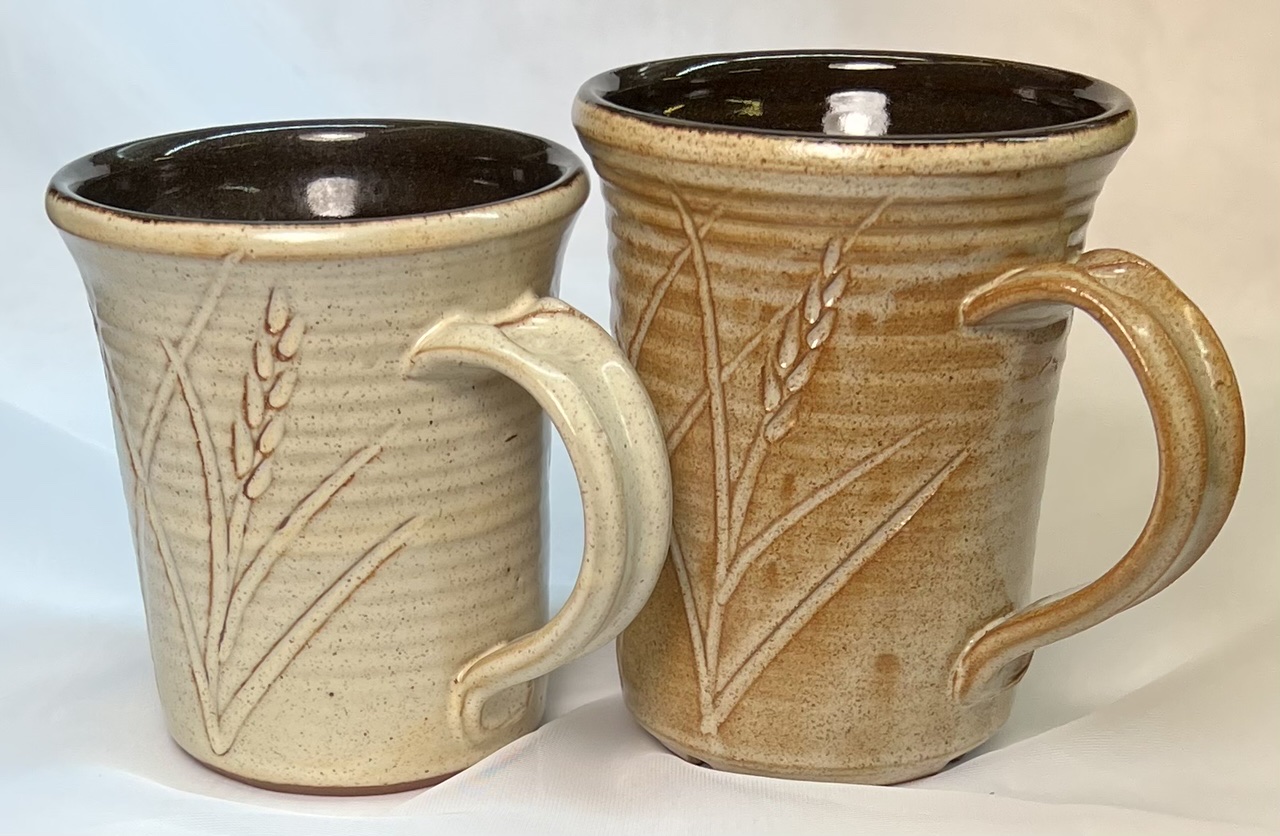
This picture has its own page with more detail, click here to see it.
I used a mix 95:5 water:gum solution when making this glaze. But even that small amount of CMC gum slowed down absorption into the bisque (and drying speed) enough that it was impossible to get it on thick enough. The version of the glaze used for the mug on the left has no gum, it is a thixotropic slurry of 1.45 specific gravity. A 3-4 second dip of a bisque piece is enough to build up a good thickness, which is important for this glaze. It dries for handling in less than 10 seconds. The one on the right was dipped twice for about 8 seconds each time and it took a minute or so before it could be handled. Yet it is still much too thinly applied. This glaze needs at least some gum because it is crawling slightly, it is an example of where precision is needed to determine the maximum that can be tolerated without impacting application thickness.
Gum content in glazes can have a dramatic effect on drying time
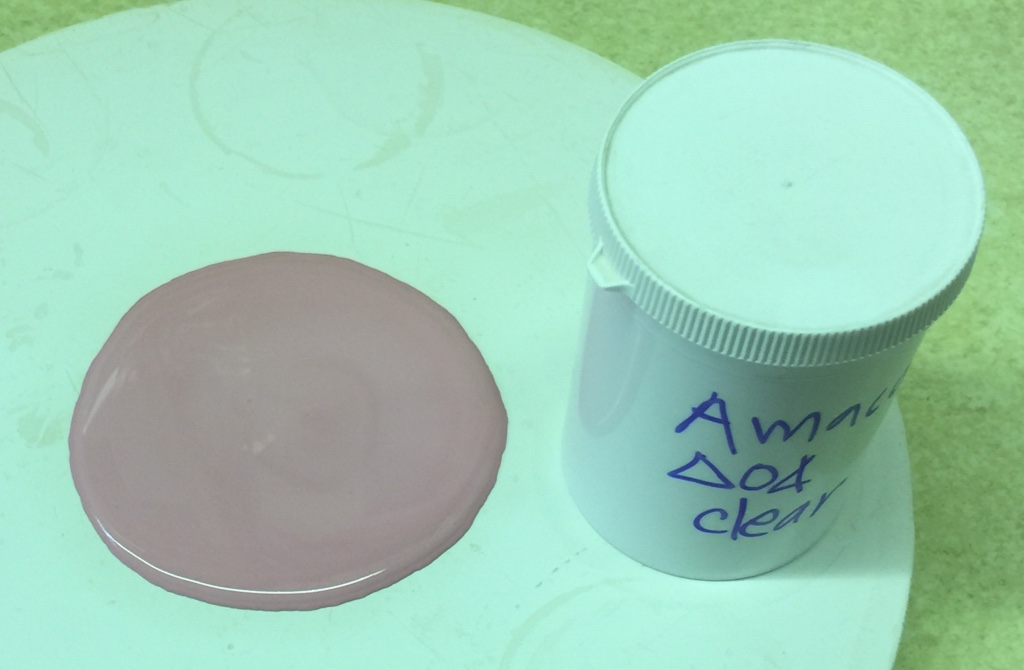
This picture has its own page with more detail, click here to see it.
This is a low fire brushing glaze. It has been sitting on this plaster bat for two hours and shows little sign of dewatering. A typical pottery dipping glaze, by contrast, would dewater in seconds! Clearly, such glazes are only good for brushing.
Veegum CER Saturated suspension
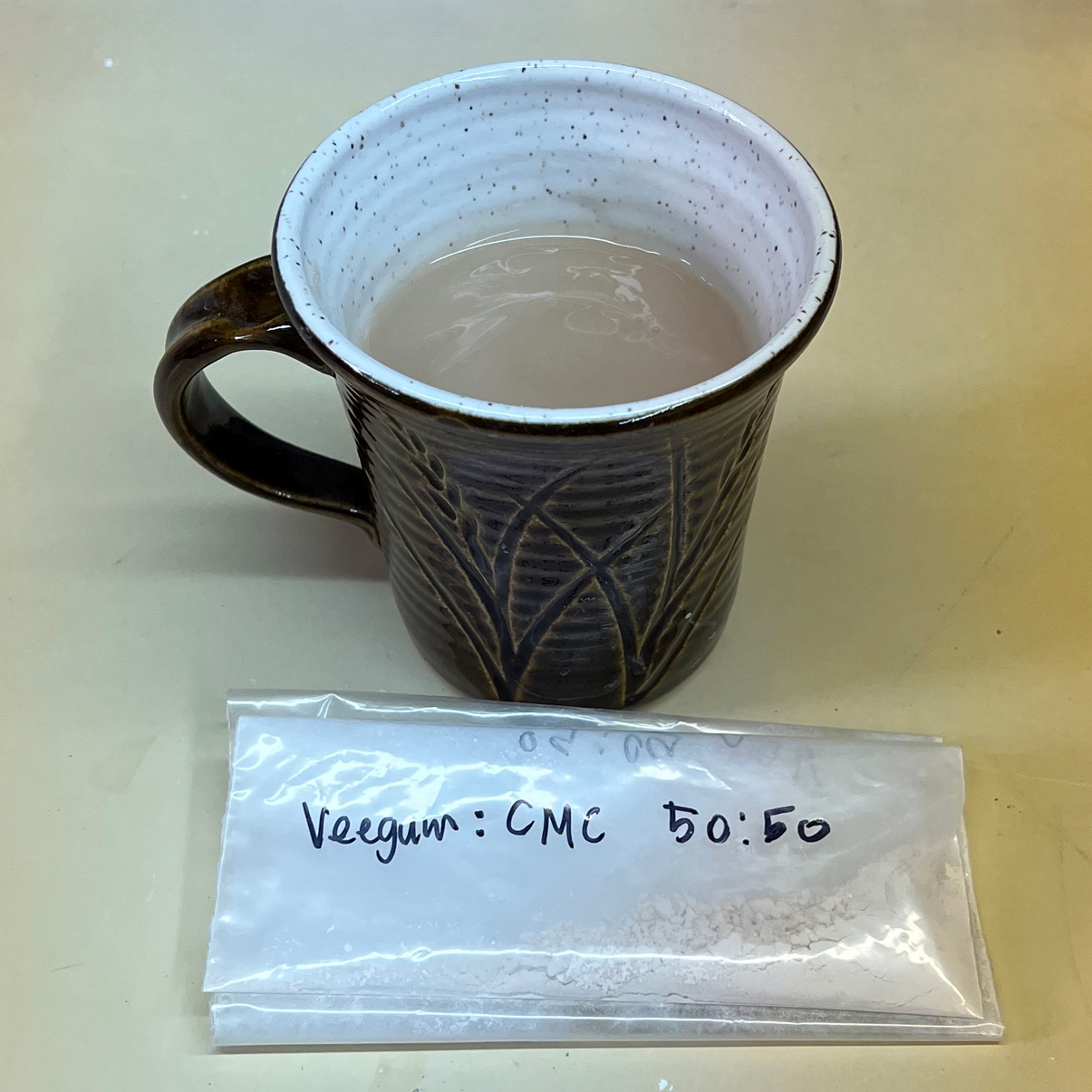
This picture has its own page with more detail, click here to see it.
This is the most viscous suspension we can make using hot water and a propeller mixer - 300ml water with 13.25g Veegum CER. In glazes having low clay content adding this gels the slurry, enabling higher water content to improve its brushing properties and slow down drying. In slurries having plenty of clay pure CMC gum is usually better (unless a high-water-content slurry is needed). Of course, keep in mind that anything with CMC gum can be subject to microbial attack.
Crawling in G2934Y Zircopax white glaze: Here are some fixes.
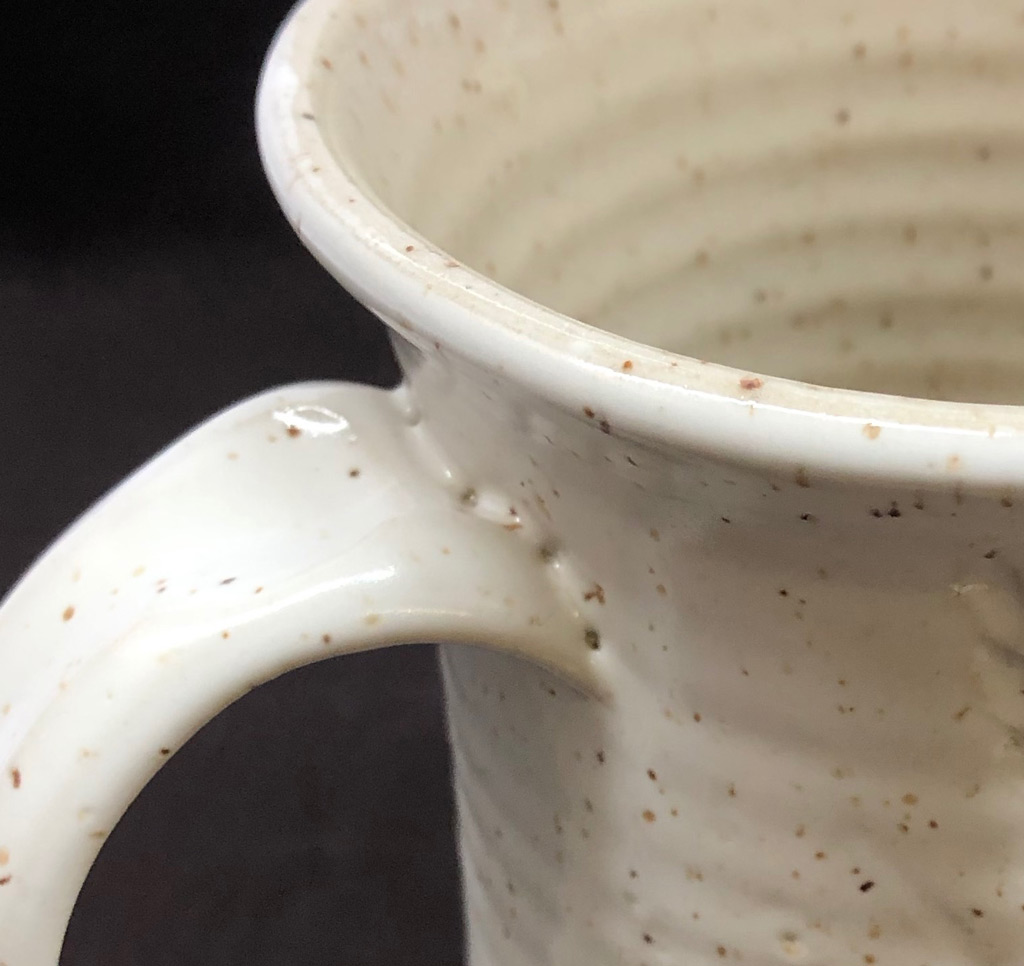
This picture has its own page with more detail, click here to see it.
G2934Y, a variation of the G2934 base, is a good stain matte base glaze but it is not without issues. It has significant clay content in the recipe and high levels of Al2O3 in the chemistry, these make it susceptible to crawling. This base is normally fine as is but when opacified or certain stains are added (especially at significant percentages) it can crawl. This has 10% Zircopax. Even though the glaze layer thickens at the recess of the handle join it is still crawling. We also get this on the insides of mugs where wall and foot meet at a sharp angle. This was initiated because the glaze cracked here during drying. Normally it would heal but the zircon stiffens the melt, making it less mobile. The easiest solution is to adjust the specific gravity of the glaze to 1.44 and flocculate it to thixotropic, this assures that the application is not too thick. Another measure is to add a little CMC gum (by replacing some of the water with gum solution). Lastly, use a blend of tin oxide and Zircopax, as in the G3926C version of the recipe, to opacify it.
Control gel using Veegum, brushing properties with CMC gum
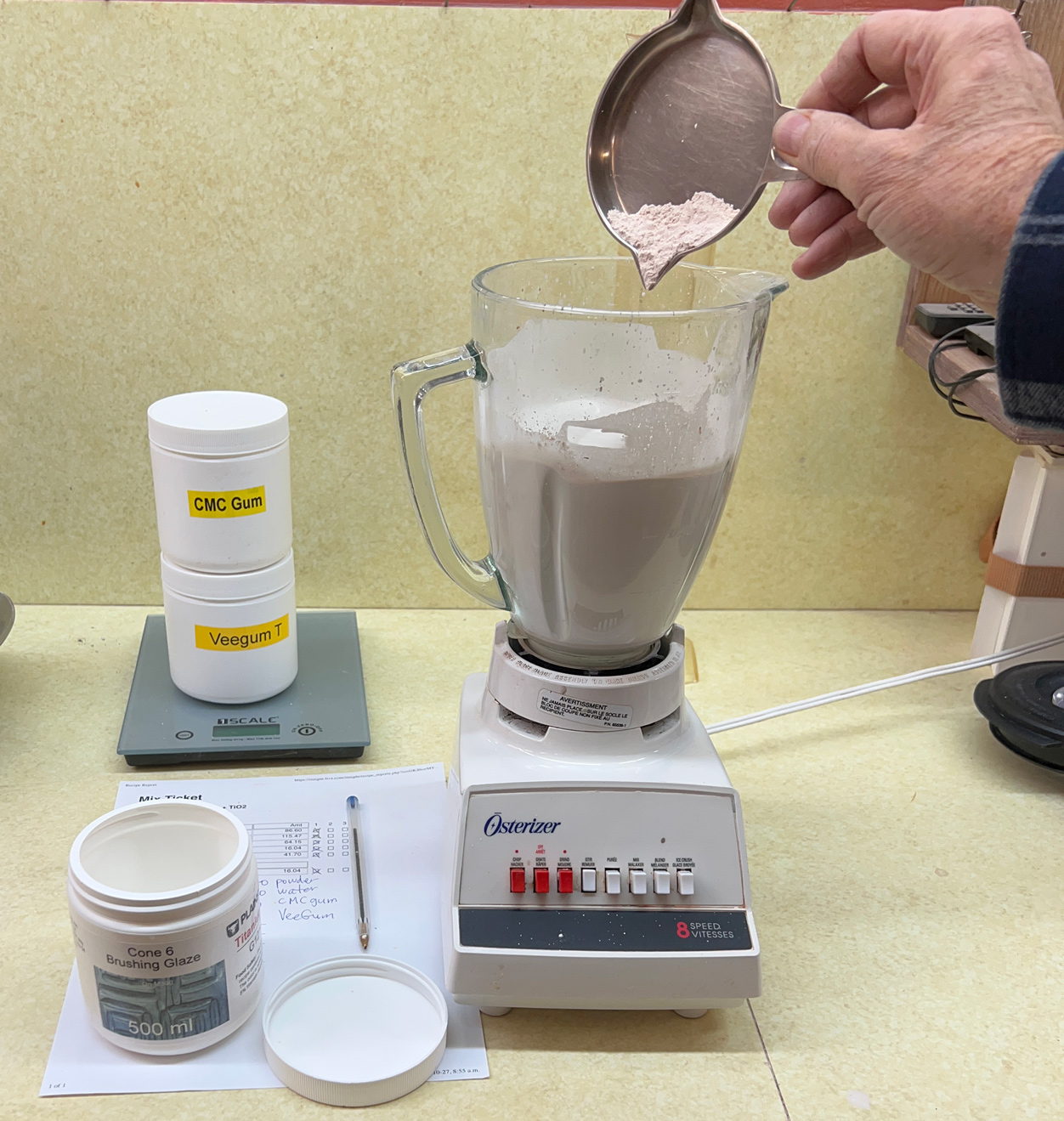
This picture has its own page with more detail, click here to see it.
This is G1214Z1 brushing glaze (with 5% titanium added). For a 340g powder batch (to get a pint) my initial target is 5g CMC gum and 5g Veegum. CMC controls drying speed and Veegum the amount of gelling. I first mix the CMC with the powder and shake the whole batch in a plastic bag. Then I add it all to 440g of water in the blender jar and mix it well (making sure no agglomerates remain (stage 1). Stage 2 is adding the VeeGum slowly, while high-speed blender-mixing, this is important because it enables tuning the degree of gel (which cannot be predicted). Because this recipe has little clay, it took all 5g of Veegum without overgelling (the entire mass moved freely in the mixer jar). But it did gel overnight (so 4g would be better next time). By contrast, it is the brushing behavior that demonstrates whether the amount of CMC is right. Not enough and coats dry too fast and go on too thick. Too much and it dries too slowly and too many coats are needed.
What to do when glazes drain and drip like this
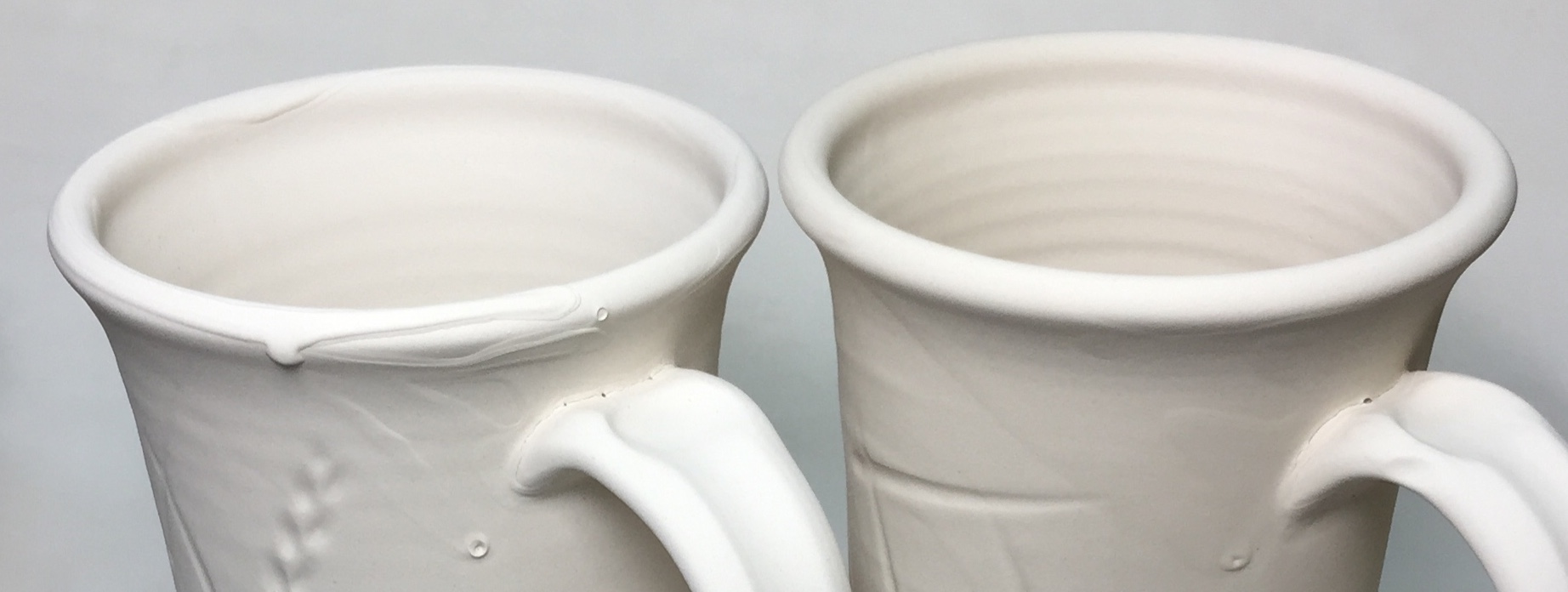
This picture has its own page with more detail, click here to see it.
These are the same dipping glaze, it is variegated and drips look ugly on fired ware. The slurry of the one on the left had a specific gravity of 1.45, it was creamy and appeared to be good. However, when this bisque porcelain mug was pulled out after the dip and rolled it formed drips on the rim. Why fix the slurry instead of just rubbing this out? Keep reading. To fix this I added water to decrease the specific gravity to 1.43. Then I added Epsom salts to induce thixotropy and gel it back to a creamy consistency. This time it went on evenly. Although the piece dries enough to handle in less than 30 seconds, it does take longer to dry completely because there is more water in the slurry. Adding CMC gum would also slow down drying but it would be very tricky to get just the right amount (otherwise dripping could be worse than this). Consider a few of the advantages of thixotropic dipping glazes: They don't settle like a rock in the bucket, they don't go on too thick or in multiple thicknesses, they don't drip and they don't dry too fast.
Paint another layer onto a fired glaze? Yes. With CMC gum.
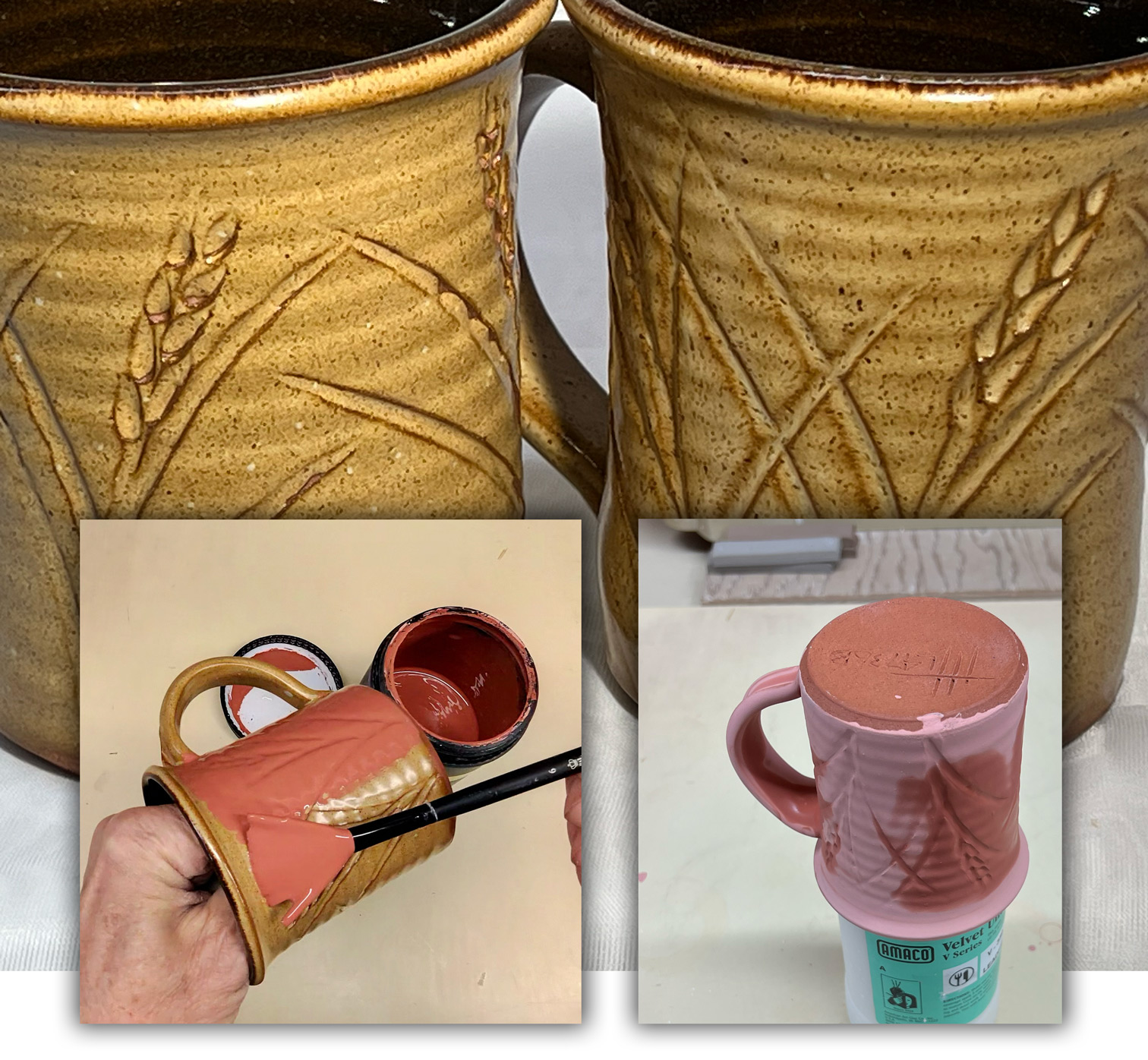
This picture has its own page with more detail, click here to see it.
The cone 6 mug on the left has the G3933A glaze, applied as a dipping glaze. It turned out poorly - crawling from corners and looking thin and washed out. I made a brushing glaze version of this (which adds 1.5% CMC gum), I keep it around for this very purpose. It has a high specific gravity (unlike commercial ones that have high water contents - they will run and go on too thin if you try this). Because of the gum it dries hard, there is no shrinkage or cracking. On a second firing, using the C6DHSC schedule again, (mug on the right) the surface is transformed - thicker, more vibrant color (being picked up from the underlying body).
Preparing balls for a melt fluidity test using CMC gum
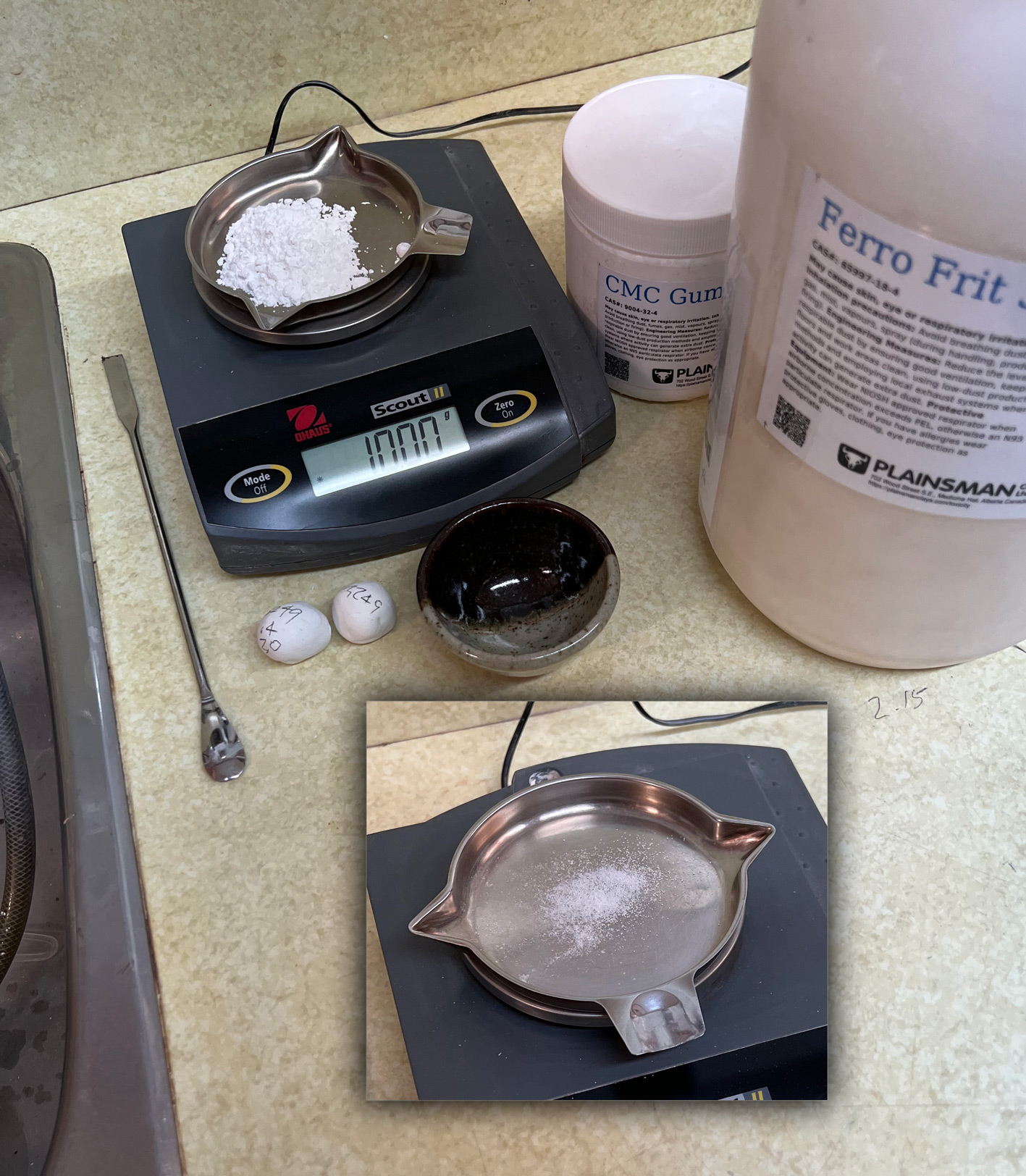
This picture has its own page with more detail, click here to see it.
We use 11g of the material being tested, e.g. a frit, (the right amount for one ball), 0.11g CMC (1%). Of course, you need a 0.01g scale to be able to accurately weigh 0.1g (that is a really small amount). Put them in a small ziplock bag, zip it to entrap air and roll the zipper down to inflate it. Shake well to mix. Stir the powder into water (~5-8g) in a small bowl. Pour it onto a plaster slab - it dewaters very quickly (e.g. as little as 10 seconds) - just as the water sheen is gone, peel it up with a rubber rib. Smear it back down and peel it up every few seconds until it is plastic and formable (but not sticky). For better formability use 1.5% CMC gum - however, the ball will dry slower - drying time is an issue with this method, you will need a heat lamp or other drier of some sort (e.g. a dehydrator). You will also need a plaster surface to absorb the excess water (which invariably happens).
VeeGum and CMC gum can plastify non-plastic powders for making melt-flow test balls
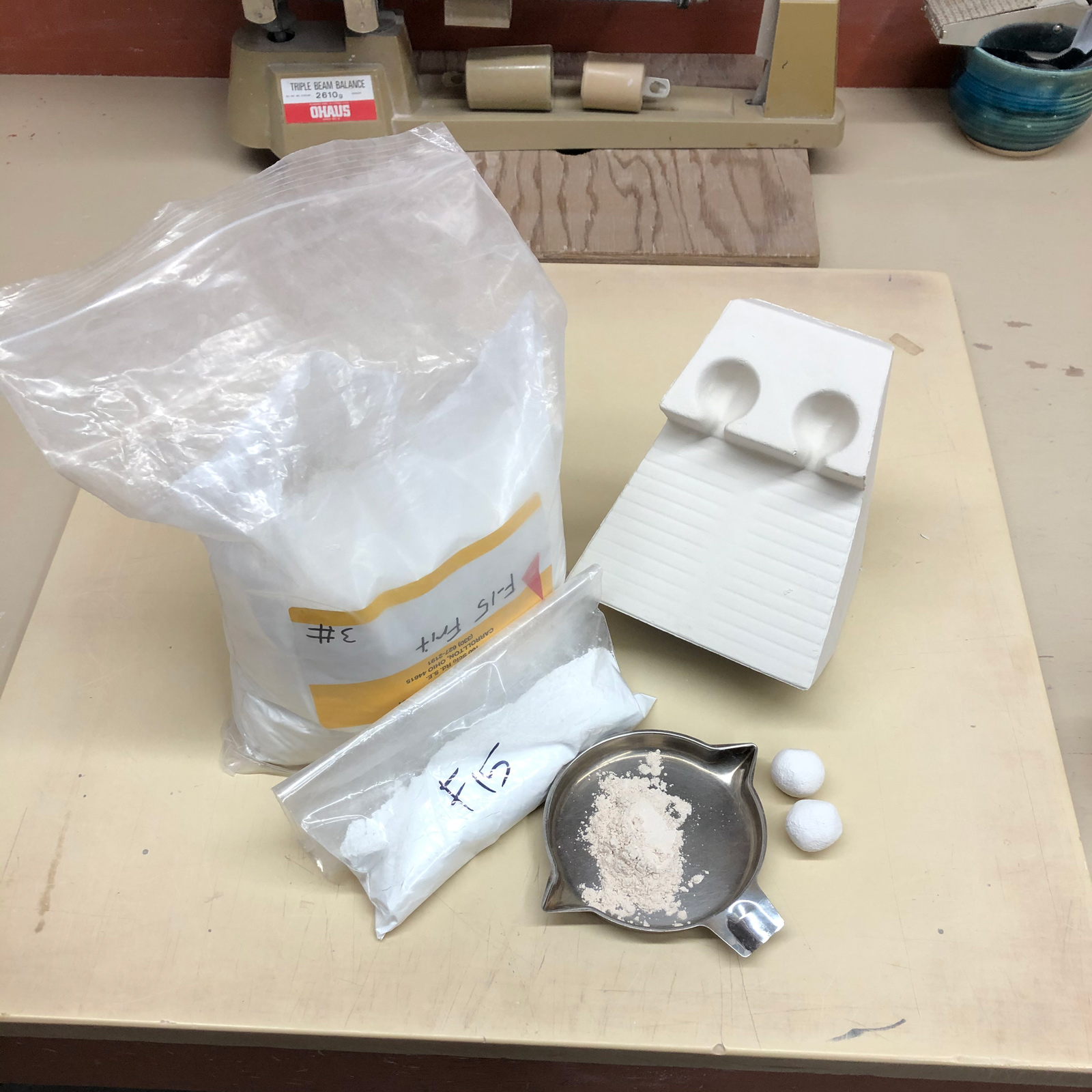
This picture has its own page with more detail, click here to see it.
Fluxes used in ceramics are almost always non-plastic, they cannot be formed like clay - frits and feldspars are good examples. And they don't dry hard. To make balls for use in the GBMF test for melt flow a binder needs to be added. Traditionally we have used Veegum, however, it interacts with materials enough to affect melting - CMC gum does not. That being said, Veegum dries better (these balls can dry very slowly). When simply comparing the melt of two materials either is fine.
Each ceramic powder responds differently to being water-mixed with a gum or plasticizer. Some material-gum mixes uptake water so well that it can be worked in drops at a time until a plastic material is produced. Others require vigorous mixing into a slurry and then dewatering on a plaster surface. We target 9g balls, they fit into the reservoir of the melt flow tester. To make one ball we start with 11 or 12g of powder (to allow for waste) and then form them into 12g (wet) balls - these dry them down to the 9g weight. We are almost always comparing the flow of two materials, in these cases it is only important that the two balls be the same weight - so we trim the heavier one down to the weight of the lighter one. Does cornstarch work? No, the mix is not plastic. Psyllium? Yes, but it has a flakey texture and demands more water.
If you are testing a plastic material then a binder is not needed.
Two methods to make your own low SG brushing glaze.
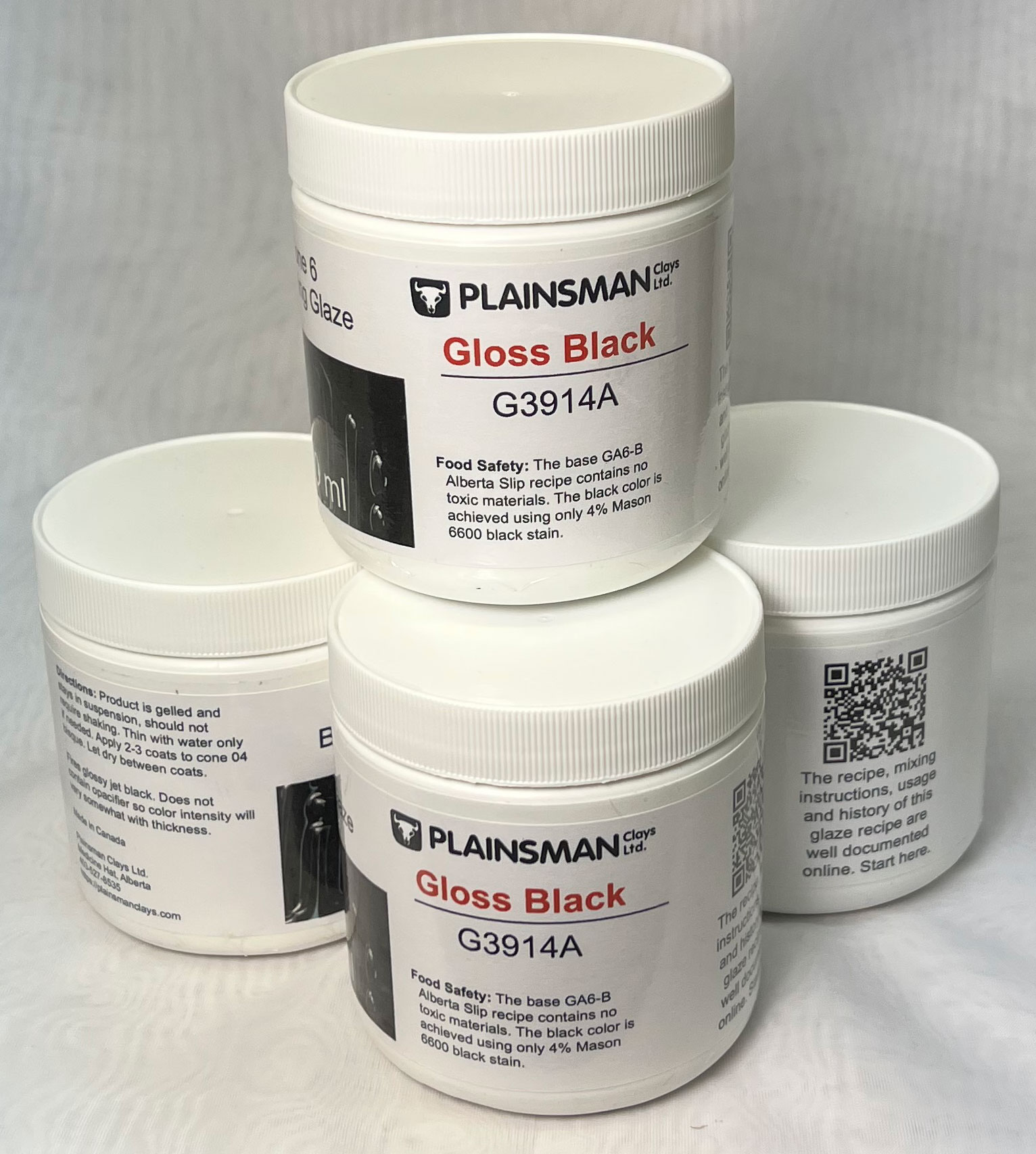
This picture has its own page with more detail, click here to see it.
Dipping glaze applies and dries in seconds. Brushing glazes dry slowly and dry hard. Brushing glazes simply have gum in the recipe, dipping glazes typically do not. This is the Alberta Slip cone 6 base, made jet black with 4% black ceramic stain (our code G3914A). We normally mix this as a dipping glaze but I have made a 500ml jar of low SG brushing version using both of the following methods. These methods will work for almost any glaze recipe (for those having exceptionally high clay content less Veegum is needed).
1) Shake together, in a plastic bag, 340g of mixed glaze powder with 5g of Veegum and 5g of CMC gum. Add that to 440g of water in a kitchen blender and mix on high speed until it gels (the gums resist mixing so the highest speed for at least 30 seconds is needed to prevent lumps).
2) Take 680g of dipping glaze (assuming it is about 50:50 water:powder you get 340g of dry), put that in the blender with another 80g of water and proceed as in method 1. Less total water is being used because the dipping glaze might not be exactly 50:50 water:powder. During mixing, if it gels too much add the extra 20g of water.
Links
Articles |
Painting Glazes Rather Than Dipping or Spraying
Potters who are used to dipping and spraying glazes might be surprised to learn how well glazes can paint on if they have enough gum in the recipe.
|
Articles |
Using Dextrin, Glycerine and CMC Gum together
|
URLs |
https://www.akzonobel.com/en
Akzo Nobel Functional Chemicals Website
|
URLs |
http://en.wikipedia.org/wiki/Carboxymethyl_cellulose
Carboxymethylcellulose at Wikipedia
|
Materials |
Peptapon
|
Materials |
Bentolite L-3
|
Materials |
Tektamer 38 Biocide
|
Materials |
Gum Arabic
|
Materials |
Optapix
|
Materials |
Methylcellulose
|
Materials |
Dextrin
|
Troubles |
Powdering, Cracking and Settling Glazes
Powdering and dusting glazes are difficult and a dust hazard. Shrinking and cracking glazes fall off and crawl. The cause is the wrong amount or type of clay.
|
Typecodes |
Additives for Ceramic Glazes
Materials that are added to glazes to impart physical working properties and usually burn away during firing. In industry all glazes, inks and engobes have additives, they are considered essential to control of cohesion, adhesion, suspension, dry hardness, surface leveling, rheology, speed-of-drying, etc. Among potters, it is common for glazes to have zero additives.
|
Glossary |
Soluble colors
|
Glossary |
Brushing Glaze
Hobbyists and increasing numbers of potters use commercial paint-on glazes. It's convenient, there are lots of visual effects. There are also issues compared to dipping glazes. You can also make your own.
|
Glossary |
Base-Coat Dipping Glaze
These are ceramic glazes intended for dipping but which contain a gum to enable them to adhere to the body better and tolerate over-layers without danger of flaking or cracking.
|
Glossary |
Glaze Layering
In hobby ceramics and pottery it is common to layer glazes for visual effects. Using brush-on glazes it is easy. But how to do it with dipping glazes? Or apply brush-ons on to dipped base coats?
|
Mechanisms