All Articles
A ChatBot gives jaw-dropping glaze recipe advice - Jan 2025A Low Cost Tester of Glaze Melt FluidityA One-speed Lab or Studio Slurry MixerA Textbook Cone 6 Matte Glaze With ProblemsAdjusting Glaze Expansion by Calculation to Solve ShiveringAlberta Slip, 20 Years of Substitution for Albany SlipAn Overview of Ceramic StainsAre You in Control of Your Production Process?Are Your Glazes Food Safe or are They Leachable?Attack on Glass: Corrosion Attack MechanismsBall Milling Glazes, Bodies, EngobesBinders for Ceramic BodiesBringing Out the Big Guns in Craze Control: MgO (G1215U)Can We Help You Fix a Specific Problem?Ceramic Glazes TodayCeramic Material NomenclatureCeramic Tile Clay Body FormulationChanging Our View of GlazesChemistry vs. Matrix Blending to Create Glazes from Native MaterialsConcentrate on One Good GlazeCopper Red GlazesCrazing and Bacteria: Is There a Hazard?Crazing in Stoneware Glazes: Treating the Causes, Not the SymptomsCreating a Non-Glaze Ceramic Slip or EngobeCreating Your Own Budget GlazeCrystal Glazes: Understanding the Process and MaterialsDeflocculants: A Detailed OverviewDemonstrating Glaze Fit Issues to StudentsDiagnosing a Casting Problem at a Sanitaryware PlantDrying Ceramics Without CracksDuplicating Albany SlipDuplicating AP Green FireclayElectric Hobby Kilns: What You Need to KnowFighting the Glaze DragonFiring Clay Test BarsFiring: What Happens to Ceramic Ware in a Firing KilnFirst You See It Then You Don't: Raku Glaze StabilityFixing a glaze that does not stay in suspensionFormulating a body using clays native to your areaFormulating a Clear Glaze Compatible with Chrome-Tin StainsFormulating a PorcelainFormulating Ash and Native-Material GlazesG1214M Cone 5-7 20x5 glossy transparent glazeG1214W Cone 6 transparent glazeG1214Z Cone 6 matte glazeG1916M Cone 06-04 transparent glazeGetting the Glaze Color You Want: Working With StainsGlaze and Body Pigments and Stains in the Ceramic Tile IndustryGlaze Chemistry Basics - Formula, Analysis, Mole%, Unity Glaze chemistry using a frit of approximate analysisGlaze Recipes: Formulate and Make Your Own InsteadGlaze Types, Formulation and Application in the Tile IndustryHaving Your Glaze Tested for Toxic Metal ReleaseHigh Gloss GlazesHire Us for a 3D Printing ProjectHow a Material Chemical Analysis is DoneHow desktop INSIGHT Deals With Unity, LOI and Formula WeightHow to Find and Test Your Own Native ClaysI have always done it this way!Inkjet Decoration of Ceramic TilesIs Your Fired Ware Safe?Leaching Cone 6 Glaze Case StudyLimit Formulas and Target FormulasLow Budget Testing of Ceramic GlazesMake Your Own Ball Mill StandMaking Glaze Testing ConesMonoporosa or Single Fired Wall TilesOrganic Matter in Clays: Detailed OverviewOutdoor Weather Resistant CeramicsPainting Glazes Rather Than Dipping or SprayingParticle Size Distribution of Ceramic PowdersPorcelain Tile, Vitrified TileRationalizing Conflicting Opinions About PlasticityRavenscrag Slip is BornRecylcing Scrap ClayReducing the Firing Temperature of a Glaze From Cone 10 to 6Setting up a Clay Testing Program in Your CompanySimple Physical Testing of ClaysSingle Fire GlazingSoluble Salts in Minerals: Detailed OverviewSome Keys to Dealing With Firing CracksStoneware Casting Body RecipesSubstituting Cornwall StoneSuper-Refined Terra SigillataThe Chemistry, Physics and Manufacturing of Glaze FritsThe Effect of Glaze Fit on Fired Ware StrengthThe Four Levels on Which to View Ceramic GlazesThe Majolica Earthenware ProcessThe Potter's PrayerThe Right Chemistry for a Cone 6 MgO MatteThe Trials of Being the Only Technical Person in the ClubThe Whining Stops Here: A Realistic Look at Clay BodiesThose Unlabelled Bags and BucketsTiles and Mosaics for PottersToxicity of Firebricks Used in OvensTrafficking in Glaze RecipesUnderstanding Ceramic MaterialsUnderstanding Ceramic OxidesUnderstanding Glaze Slurry PropertiesUnderstanding the Deflocculation Process in Slip CastingUnderstanding the Terra Cotta Slip Casting Recipes In North AmericaUnderstanding Thermal Expansion in Ceramic GlazesUnwanted Crystallization in a Cone 6 GlazeVolcanic AshWhat Determines a Glaze's Firing Temperature?What is a Mole, Checking Out the MoleWhat is the Glaze Dragon?Where do I start in understanding glazes?Why Textbook Glazes Are So DifficultWorking with children Why Textbook Glazes Are So Difficult
Description
The trade is glaze recipes has spawned generations of potters going up blind alleys trying recipes that don't work and living with ones that are much more trouble than they are worth. It is time to leave this behind and take control.
Article
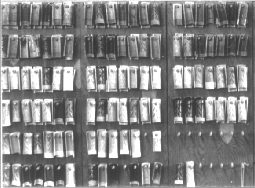
If you are like me you have racks
of test samples that never quite worked
These recipes used to be in textbooks, now they are in computer databases and on the web. But most still do not work! So many potters and companies simply buy prepared glazes. In fact, recent years have seen an explosion in the number of small manufacturers of prepared glazes.
Yet, there are still lots of masochists out there that are determined to make their own glazes and continue on their quest to find that perfect glaze just by trying textbook recipes at random. I want to make my own glazes but I am not a masochist and I do not need faith. Like me, more and more ceramic artists and technicians are saying "I am at the stage now where I want to know why, I want to understand glazes so I can fix and adjust and even formulate my own". I want to make my own glazes either from scratch or adjust an existing base, it is the only way I will get what I really want. And it is alot less expensive.
It can take new potters years to get textbook glazes out of their system. However, experience soon teaches us that these glazes seldom behave, and they are frequently touchy and introduce more problems than they solve. Sometimes people claim to have found useful glazes that work well in their circumstances. But how well? The glaze may fire to the surface they want, but what other problems and quirks do they have to endure with it that they simply overlook and tolerate. Perhaps you will agree that textbook quests don't normally breed intimate knowledge of how glazes work or even that they can be adjusted and controlled.
A good glaze is a little like a good dog. It is best to raise your own from a pup rather than trying to adopt someone else's full grown hound. Let's consider some of the reasons why a textbook glaze might not "travel" very well. As we will see, much more goes into achieving a particular glaze effect then just weighing it, throwing in some water, and slapping it on the ware. I'm not trying to discourage the use of all glaze recipes that you might import into your studio or business but I am saying a few words of warning.
- If your raw materials are different, then your version of the glaze can hardly be expected to match the author's. Remember that chemical or mineral names can be used loosely. There are thousands of different distinct minerals and grades of minerals available under an umbrella of a few dozen different generic names. The feldspar available to the glaze author may be quite different than yours. Ball clays vary across one quarry site; never mind what they do in different parts of the country. There are many different kaolin products and their physical properties, especially, vary widely. Very common materials like talc, whiting, and dolomite are available in more and less consistent versions, and some manufacturers stretch the definition of a mineral name to market their odd-ball product. Likewise, the particle size of flux-sourcing materials will have a marked effect on their reactivity and the particle sizes of refractory materials on their readiness to dissolve in the melt. Physical property differences in the materials may affect the way the glaze applies, the thickness it wants to be, the laydown density, tendency to settle and separate in the bucket, etc; these all affect the fired product. Special purpose glazes do not tolerate travelling nearly as well.
- The glaze recipe may depend on a volatile or touchy mechanism (a eutectic, a matte surface, crystal development, color response to a specific chemistry), on a tight balance of oxides, a certain mineral phase or particle size profile in one of the materials, a particular firing schedule, or some special preparation or application technique. The author may be unaware that the glaze is "on the edge" in any respect, and has never seen reason to test various temperatures, methods, material substitutions or oxide variations. Inabilities of a glaze to survive these kinds of variations will show up in your studio or factory.
- Many (or most) glazes are dramatically affected by the nature of the clay they are applied to. Porcelain reacts little with overlying glazes, whereas stonewares, especially those with iron and added fluxes and silica, can react strongly with a glaze, changing its appearance considerably. Often, the whiter, smoother, and more mature the clay body; the more vivid and brighter a glaze will be. Conversely, the darker, coarser, and more immature the body; the more subdued and dry the glaze will be. But, this is not always the case, some glazes come alive on dark burning bodies. If there is no information about how the glaze reacts to different types of clay bodies; then just about anything could happen when you try it on yours.
- A glaze can be very sensitive to temperature and cooling cycle. Some glazes produce a matte of one color if cooled slowly and a gloss of another color if cooled quickly. Different types of kilns have their own characteristic cooling curves and if yours is different than the author's, your version of his or her glaze will be also. What are the chances that you have the same interpretation on how to read cones or that your thermocouples are both performing the same? Think also about your kiln controller: Just because a kiln is programmed to heat up or cool down at a certain rate, that does not mean the elements and insulation characteristics will cooperate to produce that schedule, either in your kiln or that of the other person. How many glaze recipes do you see that come with firing schedules anyway?
- Some glazes are very sensitive to thickness of application and whether they are on a vertical or horizontal surface. Therefore, you will want to develop a glaze testing tile that provides planes of both, as well as some incised lines and sharp edges to see how well the glaze covers these, and whether it highlights or masks the relief. Also, be aware that different application techniques like spraying, pouring, and painting can produce fired surfaces on the finished ware that are very different in character from what the small dipped samples indicated.
- Is the author ball milling the glaze? If so, how long and how efficient is the mill? Many glazes are profoundly affected by milling, especially if they contain materials of coarser particle size.
- Even if you find a glaze that looks great, it could well craze or shiver on your clay body, or else fit just poorly enough to considerably weaken fired strength. Doubtless, the author has not documented how to adjust its expansion. It is even possible that the author doesn't really care or even know about issues involving fired hardness or solubility of things like manganese or barium. What if the person has an undeveloped eye for fired quality in glazes and thus tolerates a measure of pinholing, bubbling, blistering, or immaturity? What if he has the recipe so loaded with clay that it crawls half the time, or uses no clay and is so powdery you can hardly handle or decorate the ware? These are all things that you may miss at first, but which later become painfully evident.
Unfortunately, these differences don't line up and politely hit you one at a time. It is likely that most of them will come into play in any attempt to transplant a glaze recipe into a new environment. The trouble is this: If you know how to "level the playing field" to get useful tests, then you can probably formulate glazes from your own native materials anyway.
- "What about calculation?", you might ask. Every glaze has a formula of oxides, and it is true that oxide formulas travel a little easier than recipes, especially when accompanied by adequate documentation. Still, most of the above problems will come into play anyway because you still have to derive a recipe of materials to supply those oxides, and if you are smart enough to adjust a textbook glaze, then why bother. It is just easier to make your own glazes using materials native to your area.
Yes, there is something that travels even better than oxide formulas. It is the knowledge of what each oxide type contributes to a glaze, what each mineral type does to give it fired personality, and how they affect physical working properties. Each new recipe either confirms or fine tunes your existing oxide-effect knowledge, or educates you in the effects of its special purpose source materials (i.e. colorants, opacifiers, crystal forming agents) or unique formula (i.e. crystals from high CaO and low Al2O3 ). Each can be adapted to your own proven base recipes.
Add a smattering of line blending and trial and error adjustment, and you can make anything you want; adjust it any way you want. You can tell the glaze what to do. So why jump through hoops trying to pacify temperamental recipes that are always throwing ceramic tantrums in your kiln? You don't have to put up with that any more.
Related Information
Links