Notes
An encapsulated stain made by Mason Color Works. Contains Cd, Si, Zr, Se.
Works well as a body stain in porcelain, even at high temperatures (they recommend it only as a glaze stain but we have found it works well in porcelains).
Max. firing limit 2300 degrees F (1260C). May be used with zinc or without zinc.
Related Information
Polar Ice Porcelain with Body Stains - by Robert Barritz
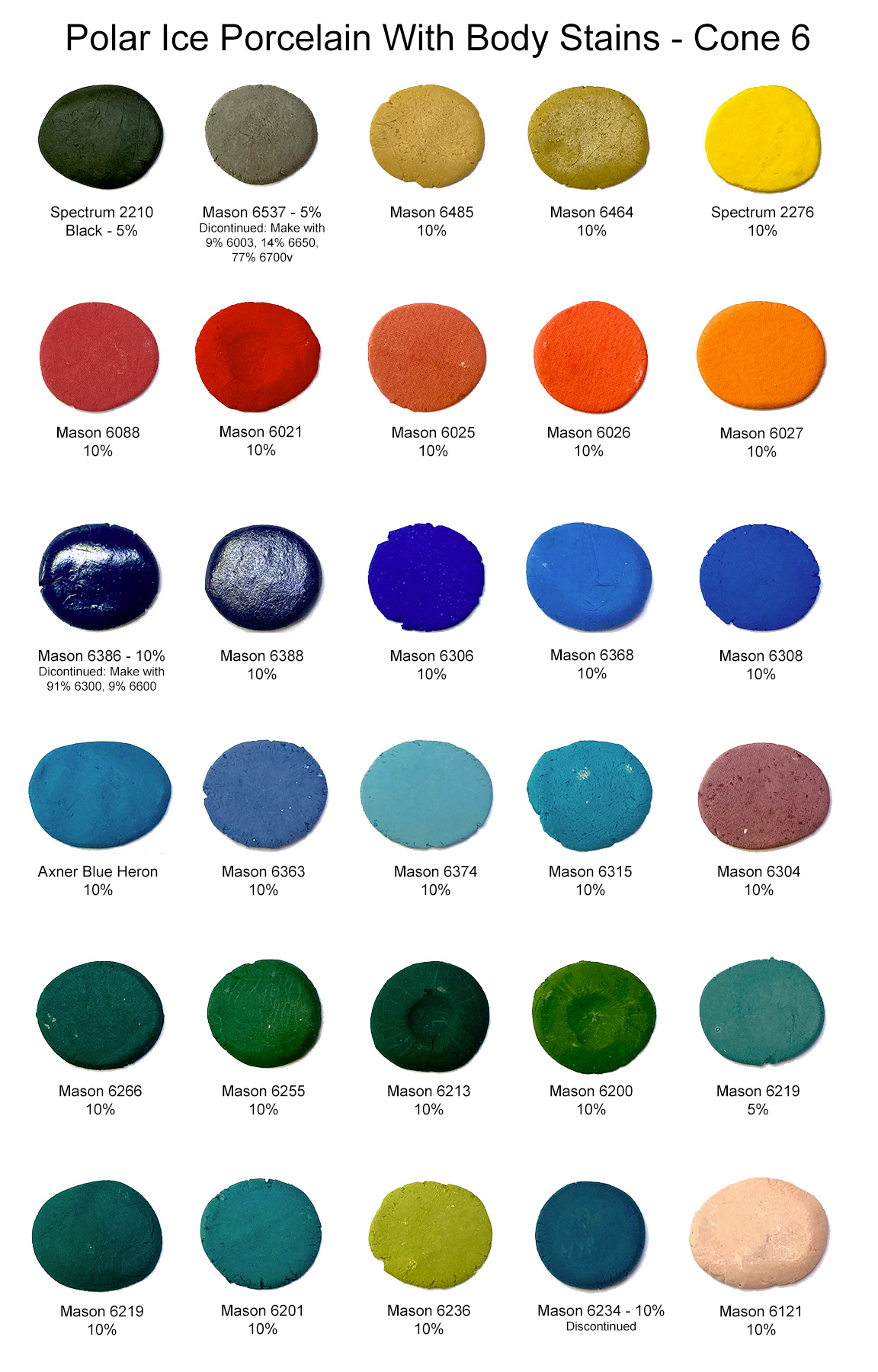
This picture has its own page with more detail, click here to see it.
Robert has done really valuable work in this research, what an amazing range of color! Surfaces are unpolished and unglazed. All are fired to cone 6. Browns are missing, they can be made using iron oxide. For blacks, Mason 6600 is also effective. The blues can be intense using lower percentages than shown here, as low as 2% can be effective. There is an optimal amount for each stain, beyond that, increases in percentage bring little increase in color intensity. There is another reason to keep stain percentages to a minimum: To reduce the impact on body maturity (and firing shrinkage). Blues, for example, can significantly heighten the degree of vitrification, even melting the porcelain. If you plan to marble different colors, keeping stain percentage as low as possible is even more important, unless you can do fired shrinkage compatibility testing, for example, the EBCT test. Need to develop your own white porcelain? See the link below.
Stains in bodies will usually bleed color into glazes used over them, especially if the body is vitreous. This can be leveraged to create or amplify variegation. Strangely, stains can increase micro bubbles in transparent glazes.
Mason stains in the G2926B base glaze at cone 6
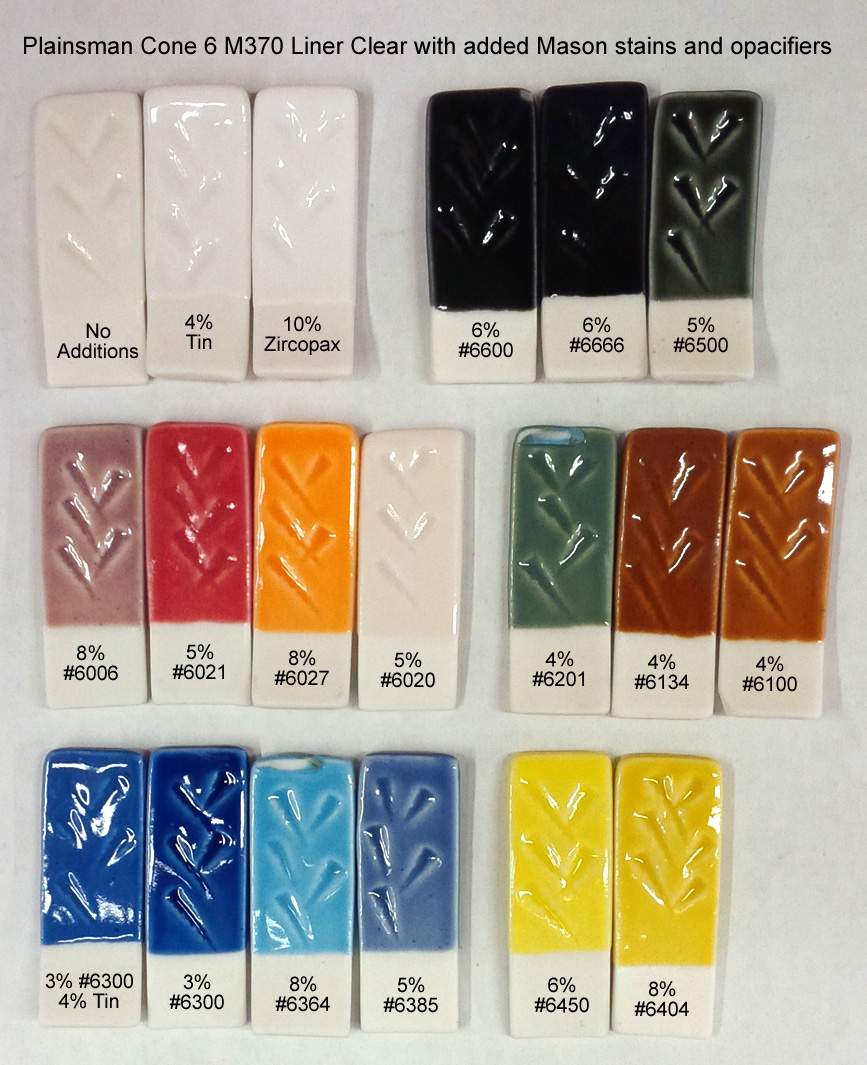
This picture has its own page with more detail, click here to see it.
This glaze, G2926B, is our main glossy base recipe. Stains are a much better choice for coloring it than raw metal oxides. Other than the great colors they produce here, there are a number of things worth noticing. Stains are potent; the percentages needed are normally much less than for metal oxides. Staining a transparent glaze produces a transparent color, it is more intense where the laydown is thicker - this is often desirable in highlighting contours and designs. For pastel shades, add an opacifier (e.g. 5-10% Zircopax, more stain might be needed to maintain the color intensity). The chrome-tin maroon 6006 does not develop well in this base (alternatives are G2916F or G1214M). The 6020 manganese alumina pink is also not developing here (it is a body stain). Caution is required with inclusion stains (like #6021). Bubbling, as is happening here, is common - this can be mitigated by adding 1-2% Zircopax. And it’s easy to turn any of these into brushing or dipping glazes.
Mason stains in G2916F cone 6 clear base
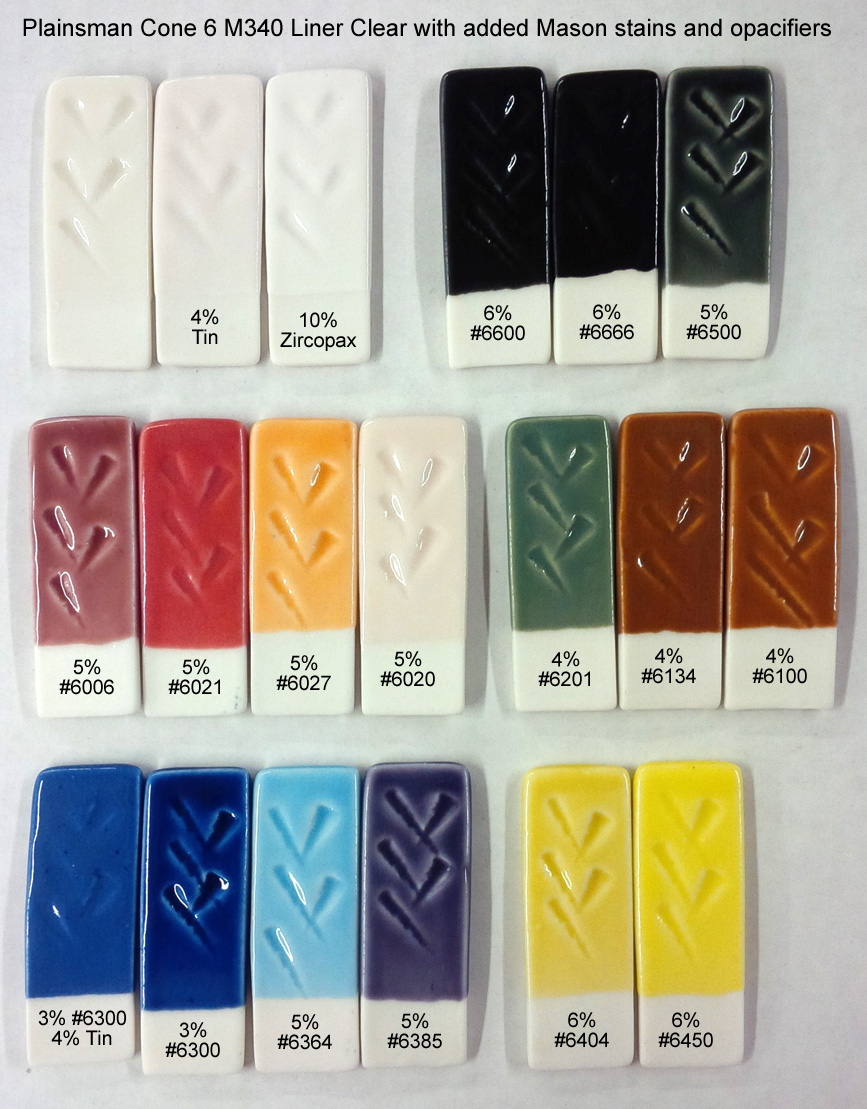
This picture has its own page with more detail, click here to see it.
These are Mason stains added to cone 6 G2916F clear liner base glaze. Notice that all of these stains develop the correct colors with this base (except for manganese alumina pink 6020). However caution is required with inclusion stains (like #6021), if they are rated to cone 8 they may already begin bubbling at cone 6 is some host glazes.
Mason stains in the G2934 matte base glaze at cone 6
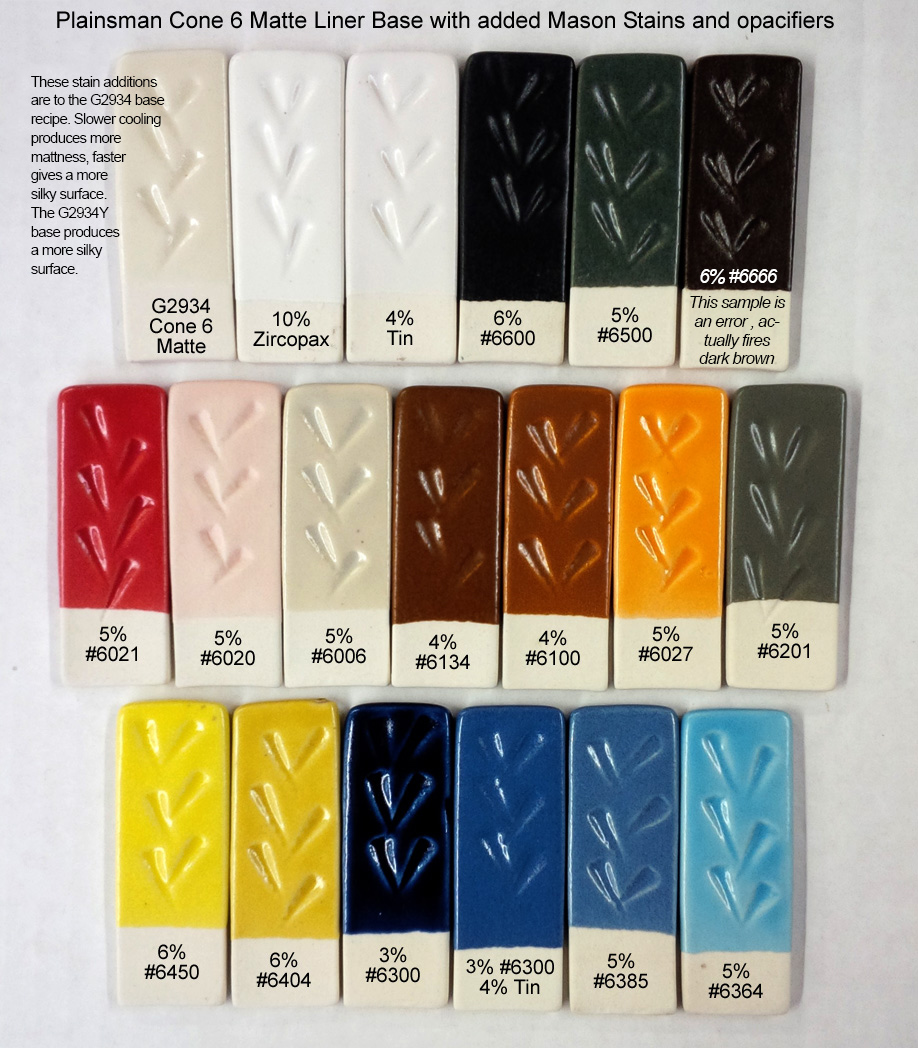
This picture has its own page with more detail, click here to see it.
Stains can work surprisingly well in matte base glazes like the DIY G2934 recipe. The glass is less transparent and so varying thicknesses do not produce as much variation in tint as glossy bases do. Notice how low many of the stain percentages are here, yet most of the colors are bright. We tested 6600, 6350, 6300, 6021 and 6404 overnight in lemon juice, they all passed leach-free. The 6385 is an error, it should be purple (that being said, do not use it, it is ugly in this base). And chrome-tin pink and maroon stains do not develop the color (e.g. 6006). But our G1214Z1 CaO-matte comes to the rescue, it both works better with some stains and has a more crystal matte surface. The degree-of-matteness of both can be tuned by cooling speed and blending in some G2926B glossy base. You can mix any of these into brushing or dipping glazes.
Red stain in matte and glossy bases. Which looks best?
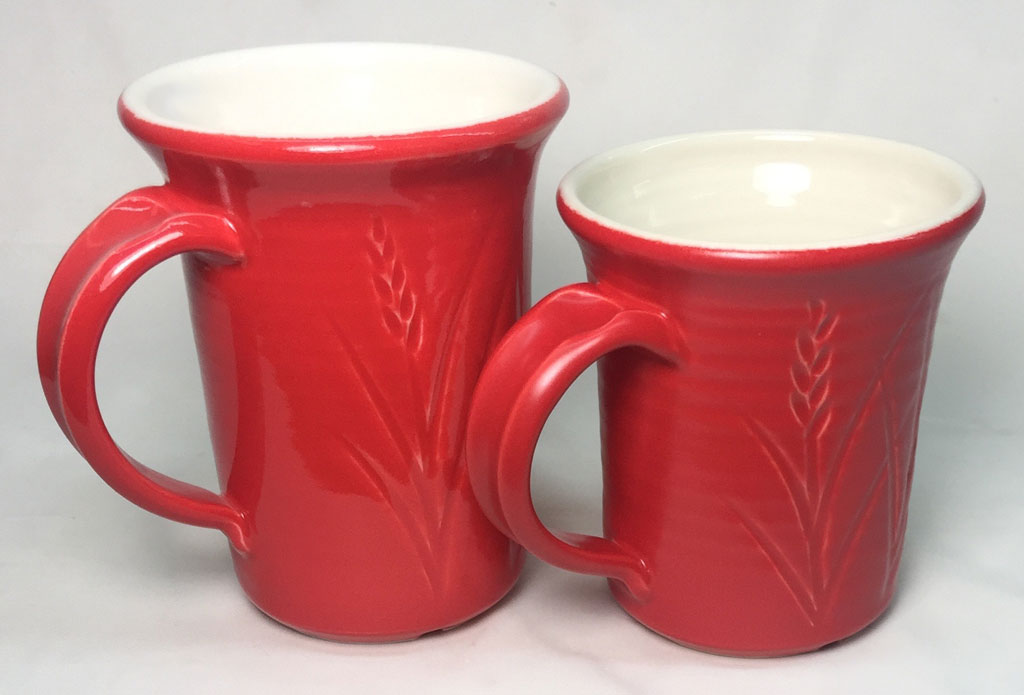
This picture has its own page with more detail, click here to see it.
The silky matte. 11% Mason 6021 encapsulated stain has been added to each. The one on the left is G2926B glossy base (it also has 2% zircopax as a fining agent for the micro-bubbles). But in the matte base on the right, G2934Y, no zircopax is necessary. It produces a stunning surface using this and other stains (including orange, yellow, black, purple), very pleasant to touch.
The varying power of different encapsulated stains
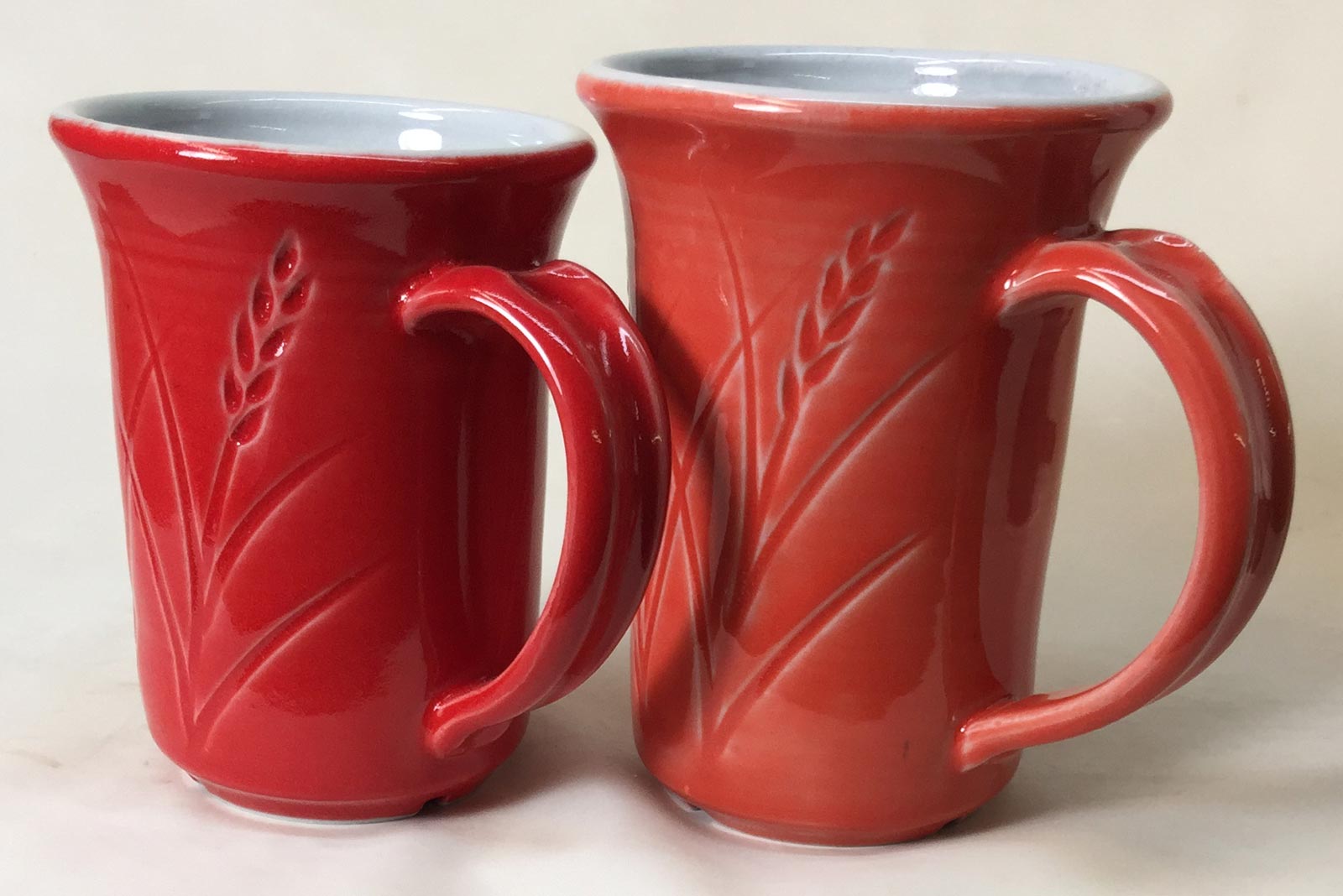
This picture has its own page with more detail, click here to see it.
These mugs are fired at cone 03. The outside glazes are G2931K transparent with added stain plus 3% Zircopax. The left one contains 10% Mason 6021 red. The right one has 15% Cerdec 297497 red stain. The latter is an older product, obviously not as potent. Encapsulated stains are a revolution in ceramics but test the ones available. You could save money and get better color at the same time.
The glaze with less stain + 2% Zircopax is brighter than the one with more stain!
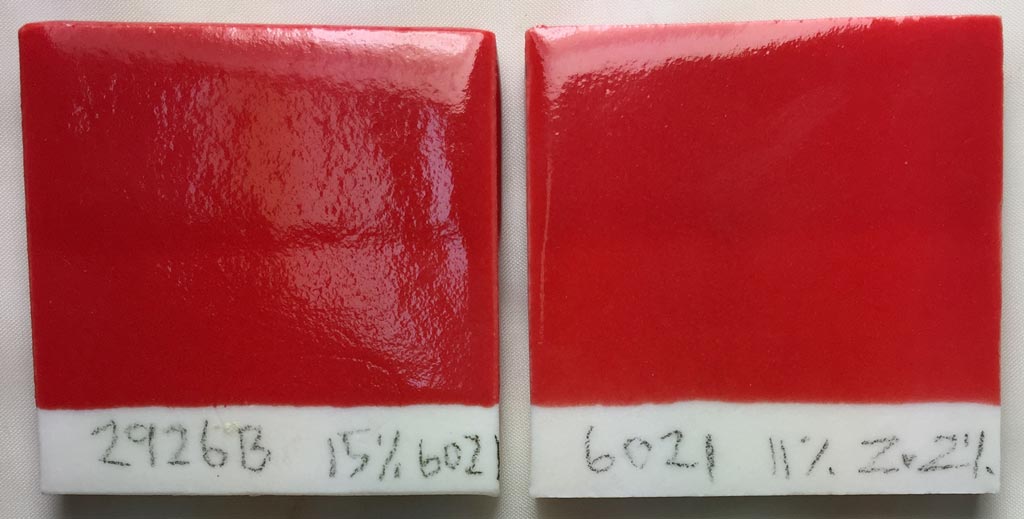
This picture has its own page with more detail, click here to see it.
These are cone 03 porcelains with G2931K clear glaze base plus Mason 6021 encapsulated stain (which is very expensive). The one on the left has 15% stain added. The one on the right is slightly less dense red but has only 10% stain plus 2% zircon (zircopax). Notice the zircon has smoothed the surface also, this is a known benefit of using it with encapsulated stains. The 2% addition is not enough to opacify, the color remains deep and translucent. But the surface is still not completely smooth and glassy as is the base transparent glaze on its own. This can be improved using a drop-and-hold firing schedule.
Glaze with an encapsulated stain is bubbling. It needs Zircopax.
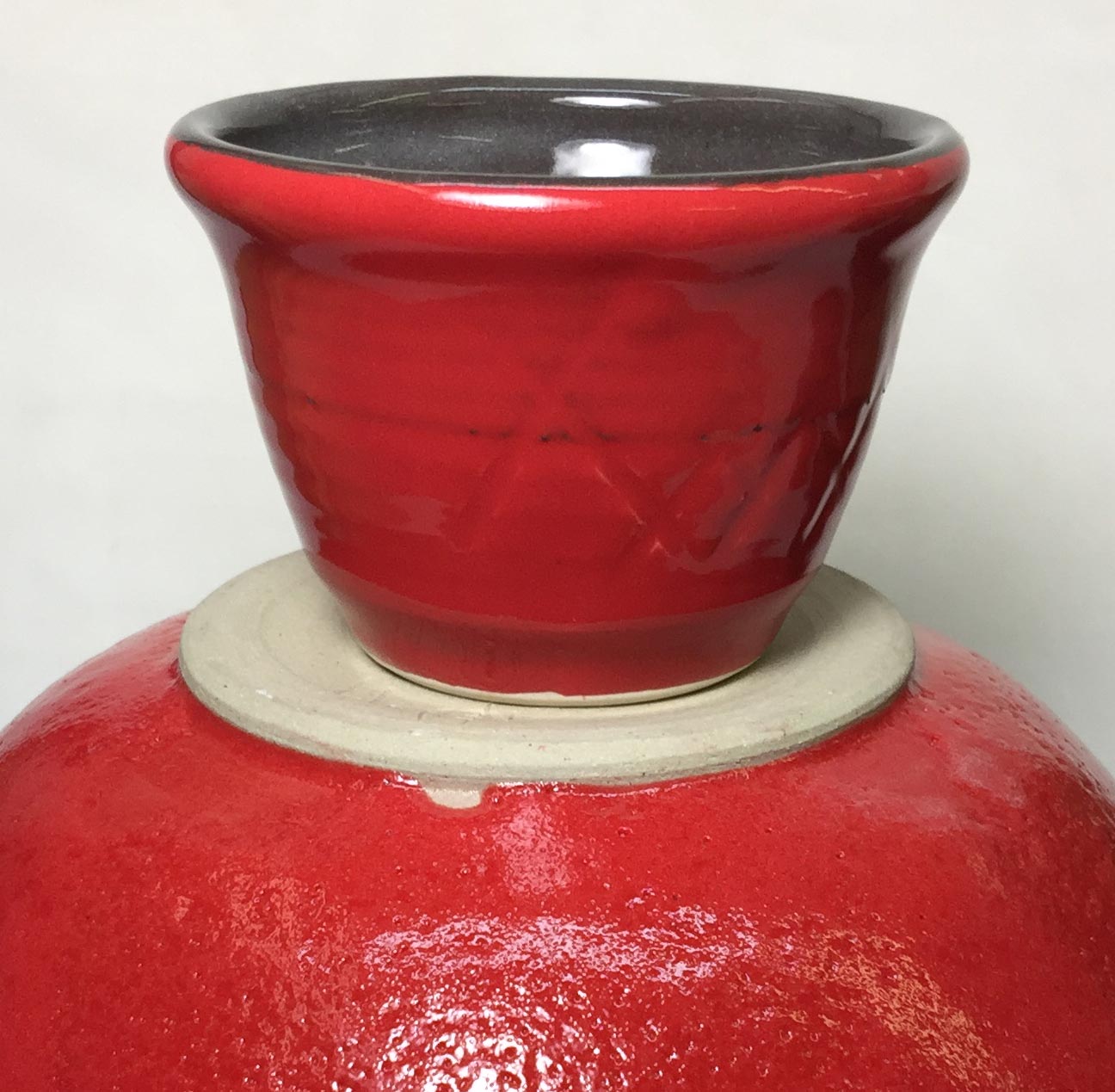
This picture has its own page with more detail, click here to see it.
These two pieces are fired at cone 6. The base transparent glaze is the same - G2926B Plainsman transparent. The amount of encapsulated red stain is the same (11% Mason 6021 Dark Red). But two things are different. Number 1: 2% Zircopax (zircon) has been added to the upper glaze. The stain manufacturers recommend this, saying that it makes for a brighter color. However, that is not what we see here. What we do see is the particles of unmelting zircon acting as seeds and collection points for the bubbles (the larger ones produced are escaping). Number 2: The firing schedule. The top one has been fired to approach cone 6 and 100F/hr, held for five minutes at 2200F (cone 6 as verified in our kiln by cones), dropped quickly to 2100F and held for 30 minutes.
A glaze incompatible with chrome-tin stains (but great with inclusion stains)
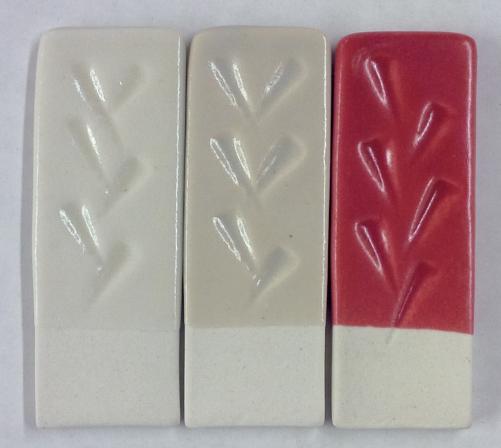
This picture has its own page with more detail, click here to see it.
Left: A cone 6 matte glaze (G2934 with no colorant). Middle: 5% Mason 6006 chrome-tin red stain added. Right: 5% Mason 6021 encapsulated red stain added. Why is there absolutely no color in the center glaze? This host recipe does not have the needed chemistry to develop the #6006 chrome-tin color (Mason specifies 10% minimum CaO, this almost has enough at 9.8%, but it also has 5% MgO and that is killing the color). Yet this same glaze produces a good red with #6021 encapsulated stain at only 5% (using 20% or more encapsulated stain is not unusual - so achieving this color with only 5% is amazing).
A cone 10R blood red - without copper but with risk
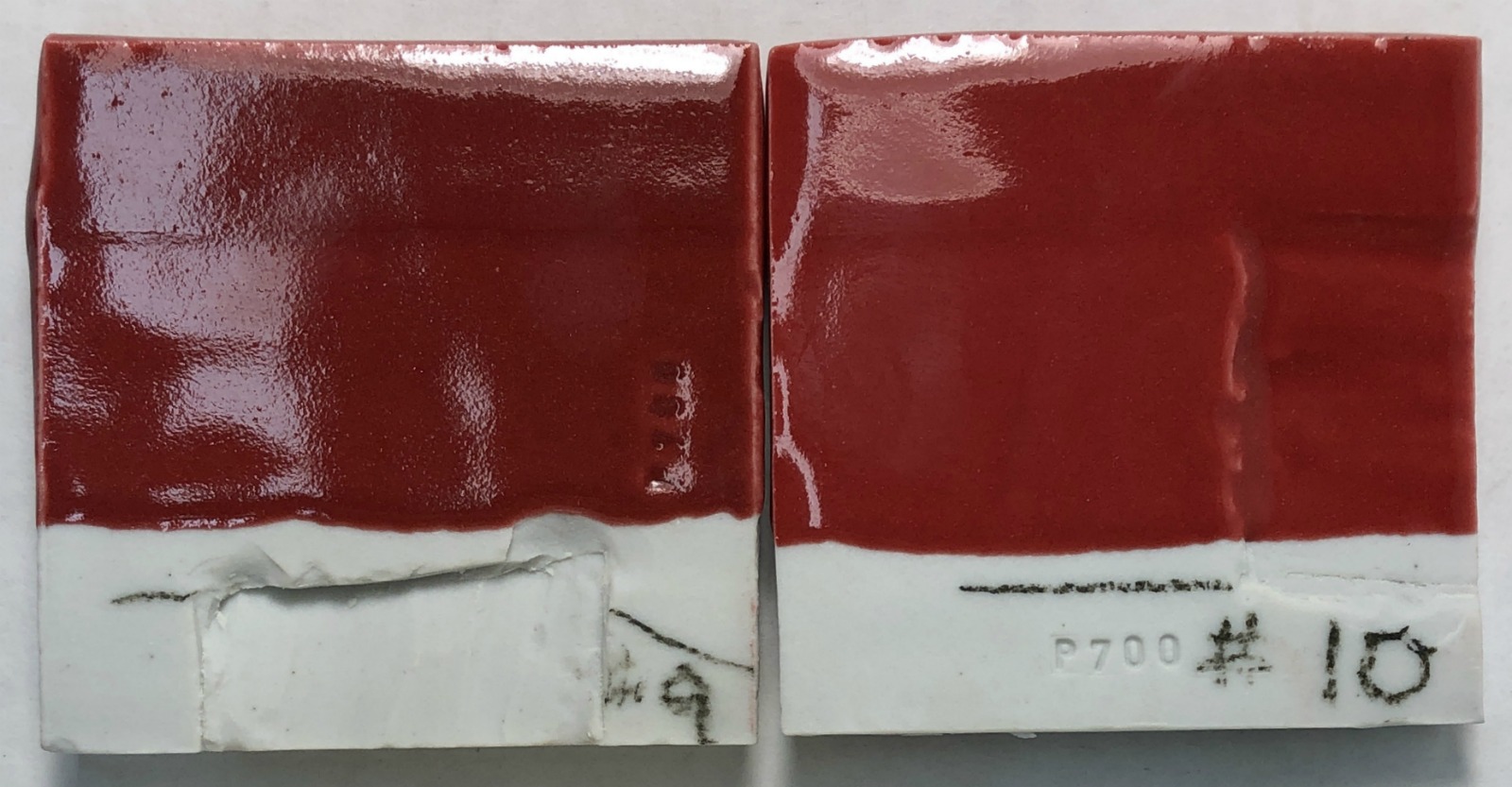
This picture has its own page with more detail, click here to see it.
This is G1947U clear glaze with 8% Mason 6021 encapsulated red stain added. The body is P700, a Grolleg kaolin porcelain. The one on the right, having significantly reduced clouding within, has one tiny addition: 2% Zircopax. It is acting as a micro-bubble fining agent, producing a brighter color and smoother surface. But there is a possible problem: These stains are not recommended for use above 2300F. Even though the color is very good, cone 10 is just on the edge of the limit temperature, so suitability for food surfaces would require careful testing for leaching cadmium.
Could inclusion stains work at cone 10 Reduction?
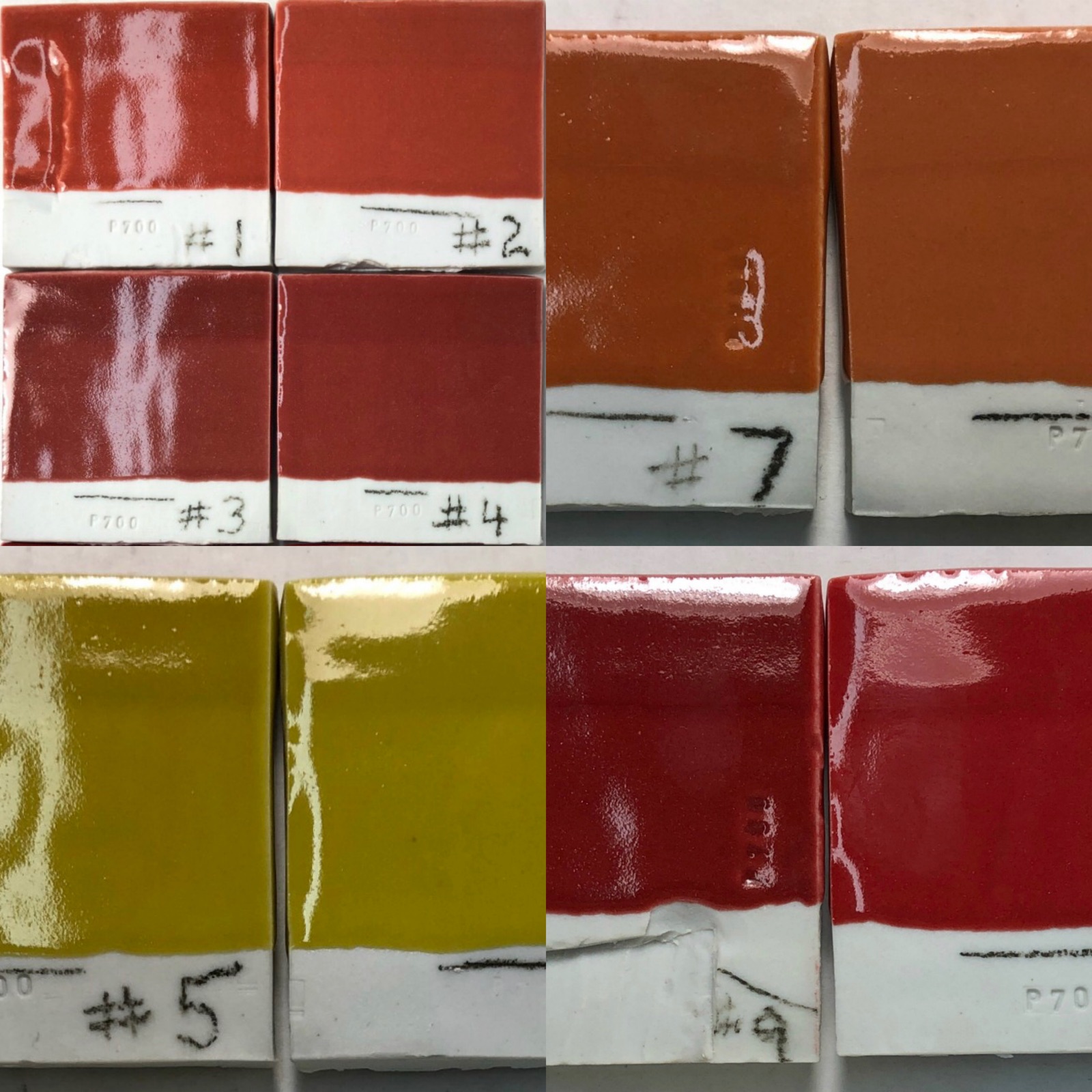
This picture has its own page with more detail, click here to see it.
In theory, these stains are supposed to burn away (decompose) by cone 10, especially cone 10 reduction. But they are alive and well! Although not as vibrant as they would be at lower temperatures. The first of each of these pairs (e.g. 1 & 2, 3 & 4, etc) has 8% stain while the other has 8% stain plus 2% Zircopax (except for the orange and yellows which have 10% stain). The 2% Zircopax was added to prevent bubbling, with an associated orange peel surface, a common occurrence with these stains in oxidation firing. But it appears the zircon is not needed in reduction. #1-8 are Cerdec colors, #9 and #10 are Mason #6021. The clear glaze base is G1947U. The firing schedule is C10RPL. The porcelain is Plainsman P700.
Pushing the limits of an encapsulated stain
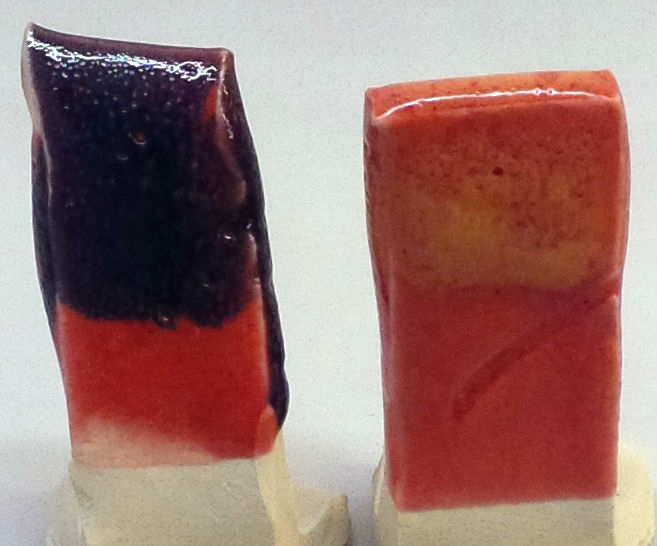
This picture has its own page with more detail, click here to see it.
Mason 6021 encapsulated stain in Plainsman M370 transparent fired at cone 6 on M370 (with second layer of two other colors). Notice the bubbling. This stain is rated to 2300F, it appears that even cone 6 is pushing its limits.
When using stains, customize the percentage, host glaze and firing schedule
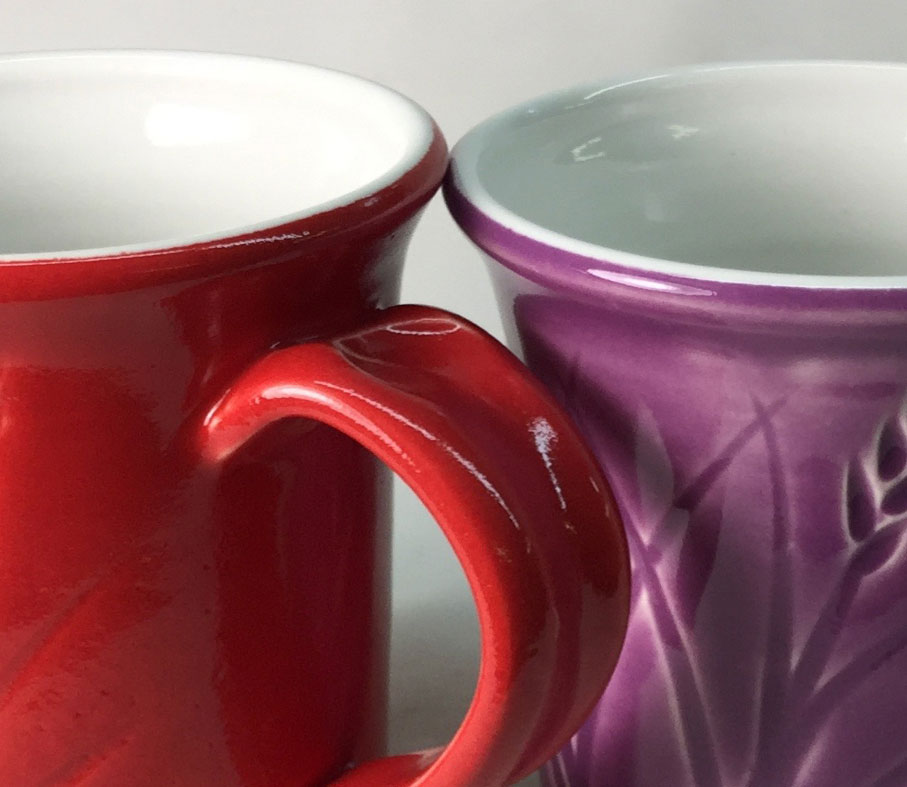
This picture has its own page with more detail, click here to see it.
These are G2926B clear glazes with stains added and fired at cone 6. The one on the left has 11% Mason 6021 encapsulated red. It is pebbling the surface (even with 2% zircon), it may be at the upper end of its firing range. Possible solutions are faster firing up and down to give the stain less chance to decompose. Or firing at cone 5 instead. Or a drop-and-hold firing schedule. Or a lower percentage, that could impart a bit of variation where it is thicker and thinner (like the purple one). A different host glaze, perhaps one with less boron. The purple one has 10% Mason 6304, it is not affecting the glossy glaze surface. But the percentage needs to be higher to prevent the wash-out of color where it is applied thinner.
Timeline to make a cone 6 red porcealin test
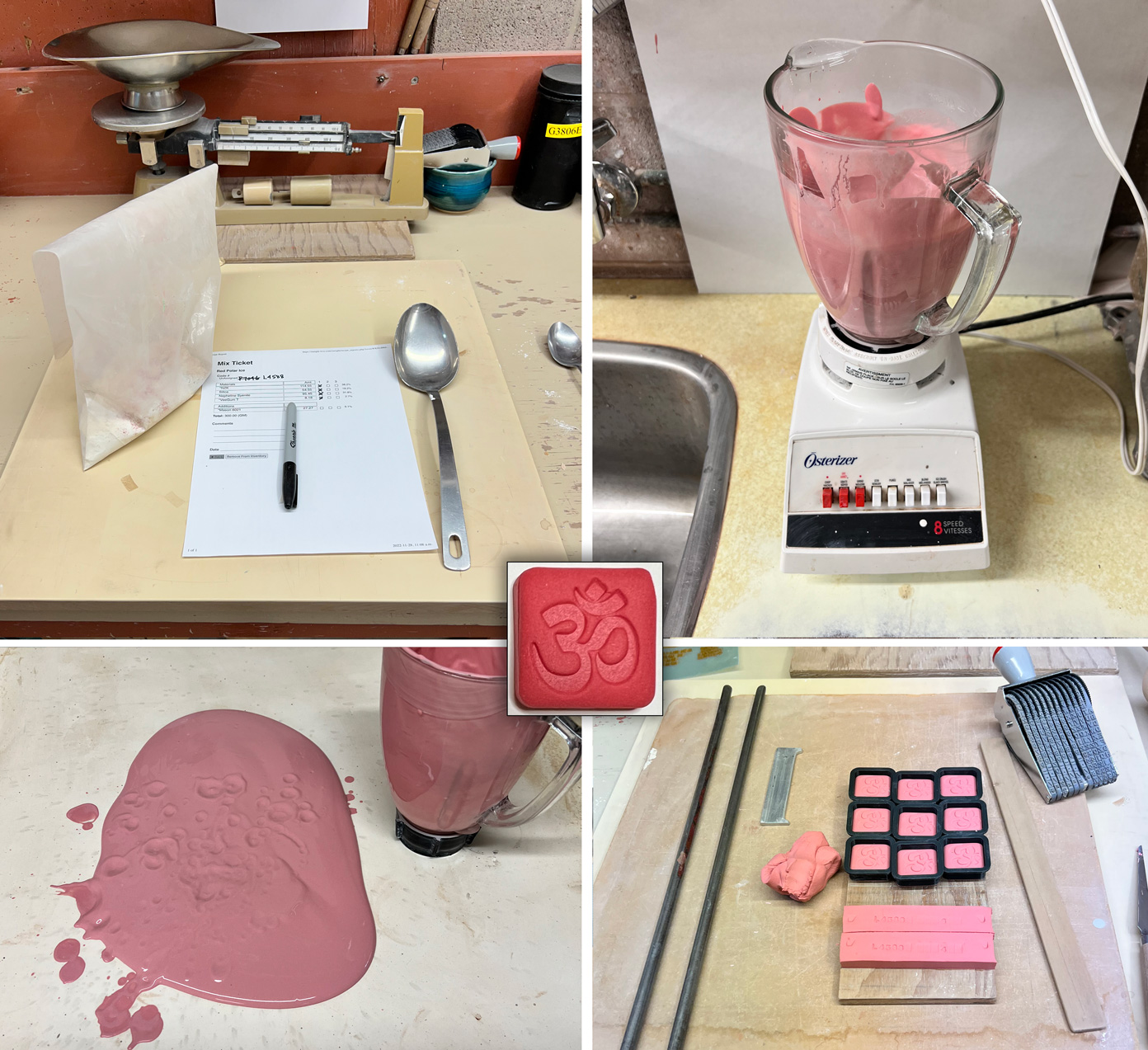
This picture has its own page with more detail, click here to see it.
This is L4588 red burning porcelain. I got the idea after coffee break and was rolling and pressing specimens right after lunch.
10.30 am: I got the idea to make this, created a record in my Insight-live account, code-numbered it and printed the recipe.
10.35 am: I started weighing it out.
10.40 am: I blender mixed it really well to remove all agglomerates.
10.45 am: I poured it onto my plaster bat.
12.30 pm: It had stiffened to the perfect consistency to roll a couple of SHAB test bars and press and stamp some porcelain theme rocks.
Next day: In the kiln. Next day: Incredible red porcelain at cone 6.
Much of the reason not to be intimidated by mixing tests like this is having all the tools and materials close at hand and a good record-keeping system. And making sure to enter results, notes and pictures as tests are completed. And linking this to related tests (I am also working on a pink and a blue).
Links