All Articles
A ChatBot gives jaw-dropping glaze recipe advice - Jan 2025A Low Cost Tester of Glaze Melt FluidityA One-speed Lab or Studio Slurry MixerA Textbook Cone 6 Matte Glaze With ProblemsAdjusting Glaze Expansion by Calculation to Solve ShiveringAlberta Slip, 20 Years of Substitution for Albany SlipAn Overview of Ceramic StainsAre You in Control of Your Production Process?Are Your Glazes Food Safe or are They Leachable?Attack on Glass: Corrosion Attack MechanismsBall Milling Glazes, Bodies, EngobesBinders for Ceramic BodiesBringing Out the Big Guns in Craze Control: MgO (G1215U)Can We Help You Fix a Specific Problem?Ceramic Glazes TodayCeramic Material NomenclatureCeramic Tile Clay Body FormulationChanging Our View of GlazesChemistry vs. Matrix Blending to Create Glazes from Native MaterialsConcentrate on One Good GlazeCopper Red GlazesCrazing and Bacteria: Is There a Hazard?Crazing in Stoneware Glazes: Treating the Causes, Not the SymptomsCreating a Non-Glaze Ceramic Slip or EngobeCreating Your Own Budget GlazeCrystal Glazes: Understanding the Process and MaterialsDeflocculants: A Detailed OverviewDemonstrating Glaze Fit Issues to StudentsDiagnosing a Casting Problem at a Sanitaryware PlantDrying Ceramics Without CracksDuplicating Albany SlipDuplicating AP Green FireclayElectric Hobby Kilns: What You Need to KnowFighting the Glaze DragonFiring Clay Test BarsFiring: What Happens to Ceramic Ware in a Firing KilnFirst You See It Then You Don't: Raku Glaze StabilityFixing a glaze that does not stay in suspensionFormulating a body using clays native to your areaFormulating a Clear Glaze Compatible with Chrome-Tin StainsFormulating a PorcelainFormulating Ash and Native-Material GlazesG1214M Cone 5-7 20x5 glossy transparent glazeG1214W Cone 6 transparent glazeG1214Z Cone 6 matte glazeG1916M Cone 06-04 transparent glazeGetting the Glaze Color You Want: Working With StainsGlaze and Body Pigments and Stains in the Ceramic Tile IndustryGlaze Chemistry Basics - Formula, Analysis, Mole%, Unity Glaze chemistry using a frit of approximate analysisGlaze Recipes: Formulate and Make Your Own InsteadGlaze Types, Formulation and Application in the Tile IndustryHaving Your Glaze Tested for Toxic Metal ReleaseHigh Gloss GlazesHire Us for a 3D Printing ProjectHow a Material Chemical Analysis is DoneHow desktop INSIGHT Deals With Unity, LOI and Formula WeightHow to Find and Test Your Own Native ClaysI have always done it this way!Inkjet Decoration of Ceramic TilesIs Your Fired Ware Safe?Leaching Cone 6 Glaze Case StudyLimit Formulas and Target FormulasLow Budget Testing of Ceramic GlazesMake Your Own Ball Mill StandMaking Glaze Testing ConesMonoporosa or Single Fired Wall TilesOrganic Matter in Clays: Detailed OverviewOutdoor Weather Resistant CeramicsPainting Glazes Rather Than Dipping or SprayingParticle Size Distribution of Ceramic PowdersPorcelain Tile, Vitrified TileRationalizing Conflicting Opinions About PlasticityRavenscrag Slip is BornRecylcing Scrap ClayReducing the Firing Temperature of a Glaze From Cone 10 to 6Setting up a Clay Testing Program in Your CompanySimple Physical Testing of ClaysSingle Fire GlazingSoluble Salts in Minerals: Detailed OverviewSome Keys to Dealing With Firing CracksStoneware Casting Body RecipesSubstituting Cornwall StoneSuper-Refined Terra SigillataThe Chemistry, Physics and Manufacturing of Glaze FritsThe Effect of Glaze Fit on Fired Ware StrengthThe Four Levels on Which to View Ceramic GlazesThe Majolica Earthenware ProcessThe Potter's PrayerThe Right Chemistry for a Cone 6 MgO MatteThe Trials of Being the Only Technical Person in the ClubThe Whining Stops Here: A Realistic Look at Clay BodiesThose Unlabelled Bags and BucketsTiles and Mosaics for PottersToxicity of Firebricks Used in OvensTrafficking in Glaze RecipesUnderstanding Ceramic MaterialsUnderstanding Ceramic OxidesUnderstanding Glaze Slurry PropertiesUnderstanding the Deflocculation Process in Slip CastingUnderstanding the Terra Cotta Slip Casting Recipes In North AmericaUnderstanding Thermal Expansion in Ceramic GlazesUnwanted Crystallization in a Cone 6 GlazeUsing Dextrin, Glycerine and CMC Gum togetherVolcanic AshWhat Determines a Glaze's Firing Temperature?What is a Mole, Checking Out the MoleWhat is the Glaze Dragon?Where do I start in understanding glazes?Why Textbook Glazes Are So DifficultWorking with children Tiles and Mosaics for Potters
Description
If you are a potter you already know much of what is needed to manufacture tile. However there are some things you need to unlearn to make tile well.
Article
Ceramic supply companies are often amazed at how well some of their tile-making customers are doing and how quickly their businesses sometimes grow. You may not be aware of how quickly the hand-decorated tile, custom tile, and mosaic tile businesses have grown in the past few years. For example, visit http://axner.com and search the 'books' area for the word "Tile", some stunning books are available.
Anyone who has visited a modern tile plant in Italy, Spain, Turkey, etc. is amazed at the innovation of these companies and the kind and size of automated production equipment they use. The dust pressing, silk screening, glass fritting, engobing, fast firing processes that are the mainstay of the industry are almost completely unknown to potters. However, although these companies produce huge volumes of tile, there are many niche custom tile markets for small players to fill around the world.
There are some interesting aspects of tile production that make it a good 'bread and butter' source of income compared to more traditional forms of hobby pottery. For example:
- You don't have to make the tile, you can buy them already bisque fired. Huge tile plants in Turkey and Italy measure their output in thousands of square meters per day and bisque tiles are inexpensive (although you may have to do a little hunting for a supplier that buys in volume).
- Wax Line: This is a great product sold only at the axner.com site. If you want to hand decorate or silk-screen then check this out.
- Tiles are flat so you can silk screen decoration onto them and do large murals or repeating designs easily. You can utilize graphics software on your computer in the design and pattern making process and you can showcase your artistic and design abilities in vivid color and line.
- If you buy bisque tile and work at low fire you can expect much fewer manufacturing problems and you'll be able to gear your production up very quickly.
- While great tiles can be made at any temperature and in any kiln this is one area where electric kiln users have a big advantage. Low fire is economical and technically ideal for non floor tile production because the tiles don't warp or sag during firing and you can utilize very brightly colored glazes.
- Mosaics add a third dimension to tile craft, they can be applied to almost any surface (including pottery). There are lots of ways to make and fire the small tiles and warping and shrinkage problems are a non-issue. Stunning examples of mosaic tile are can be found in currently available books. If you visit countries in Europe or Asia, for example, go to buildings that have fine mosaic work and study how the tiles are shaped and arranged (there is no randomness, definite visual techniques are employed).
However if you want to make your own tiles you should be aware that you will have to relearn and unlearn some things. Techniques that you may have gotten away with in pottery will not necessarily work in tile production. For example, avoiding drying cracks and dry warping can be very difficult in hand made tiles made by a pressing, rolling or extruding. This is because the clay body must be plastic and have a high water content (and therefore high shrinkage).
By contrast, industry employs dust pressing, it is undoubtedly the fastest and most precise method for tile making and no drying racks or chambers are required (RAM pressing is also used for special shapes). Dust pressed tiles have no drying shrinkage and remaining water can be expelled in the kiln. Also, the dust pressing method puts a lot of the burden of manufacture on mechanical engineers (which are easier to find than ceramic engineers).
Potters who begin making tile also find it very difficult to fire tile without warping it, even at low temperatures. Industrial kilns, by contrast, can heat a tile so evenly that vitreous tiles up to 120cm by 80cm can be fired perfectly flat and very quickly. Standard tiles, even vitreous ones, can be fired in an hour. The average potter would say that these things are impossible (they are in any kiln they are used to using). Industrial kilns are highly controlled tunnels that the tiles convey through in a continuous fashion, periodic pottery kilns require a lot of shelves to fire any amount, this severely reduces kiln efficiency an evenness of firing.
The tile industry is very well represented on the internet, perhaps better than any other segment of ceramics. Check out a search engine for some inspiration. There are some amazing tile shows held around the world, the one in Orlando, Florida each year, for example, is huge. While it is mainly tile companies show casing their ware at this show, there are lots of related industries that participate also. Anyone interested in tile who walking through a show like this will have ideas flooding into their minds faster than they can write them down.
If you are serious about tile production, be willing to get your information from industry rather than other potters, that is where the real knowledge can be found. If you can find a way to communicate with the ceramic engineers at these companies (not the salesman) you will often find them very helpful and giving, that has been our experience.
Here are a few suggestions if you are beginning to make handmade tiles:
- Dry the tiles on plaster board, it will absorb water from the whole surface evenly. Sandwiching tiles between plaster boards during drying can also work (as long as they are free to shrink without excessive drag)
- Don't cut slices directly from a slug of manufactured clay because laminations during extrusion will result in cracks or warping
- Use clay as stiff and non-plastic as possible to minimize drying shrinkage (use of a grogged clay body will also reduce shrinkage)
- Don't disturb tiles after cutting them, if you need to move them cut them on paper and slide the paper onto another board.
- Paint edges with wax to help decrease the drying at edges that makes them curl
- Dry slowly and evenly in a high humidity air flow drier if possible
- Cut channels in the back of the tiles if they are thick
- Flip them on boards, do not handle or bend them.
By Tony Hansen Follow me on
 | 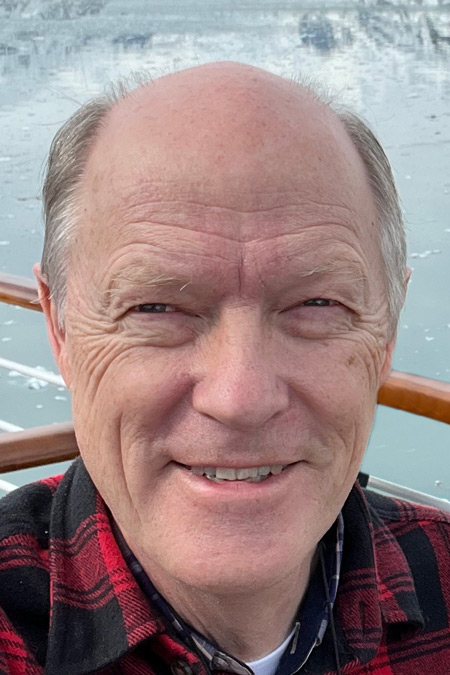 |
Got a Question?
Buy me a coffee and we can talk 
https://digitalfire.com, All Rights Reserved
Privacy Policy