Notes
This form of copper carbonate is the article of commerce. What you are getting when you buy it is a mixture of theoretical copper carbonate and copper hydroxide. The chemical structure sees two Cu atoms bonding to an OH each and sharing a CO3. Data sheets might quote the amount of Cu metal in the material (rather than CuCO3 or Cu(OH)2).
Copper Carbonate has a fairly complex decomposition. The accompanying curve shows the history of weight loss as this material is fired (courtesy of Bob Hickerson, World Metal, LLC). It is interesting to compare this chart with the one for Copper Hydroxide to see the difference in the amount of weight lost, and when and how fast it occurs.
As with other metallic coloring carbonates, copper carbonate is bulkier than the oxide form, thus it tends to disperse better to give more even results. It is also more reactive chemically and thus melts better. As such, it is ideal for use in brushwork where minimal speck is required. However, it produces gases as it decomposes and these can cause pinholes, orange peeling and blisters in glazes. Also, the carbonate form contains less copper per gram, therefore colors are less intense than the oxide form.
The hydroxyl component is an important aid in dispersing the powder throughout the glaze slurry and thus avoid specks in the fired glaze.
Supplies of green copper carbonate basic often vary in color and density (darker and heavier, lighter and fluffier) reflecting variations in raw materials and manufacturing procedures. Despite variations in the physical appearance of the material, the amount of contained copper metal remains essentially constant.
The raw powder begins to melt between 1950 and 2000F. At around 1500F it gases and will discolor nearby items in the kiln.
Related Information
Copper carbonate fuming
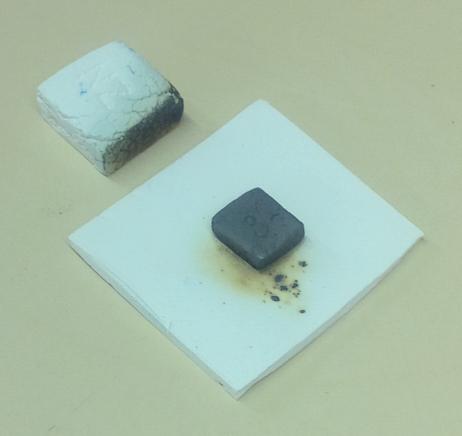
This picture has its own page with more detail, click here to see it.
And example of how copper carbonate fumes during firing. The white sample on the left was near the copper sample, at around 1500F the fumes discolored its facing edge. These are permanent, they do not fire out but get darker with increasing temperature (this is 1950F). The kiln shelf was also discolored outward about half an inch from the copper specimen.
Black ash glaze for 20% raw metal pigments: Suitable for functional ware?
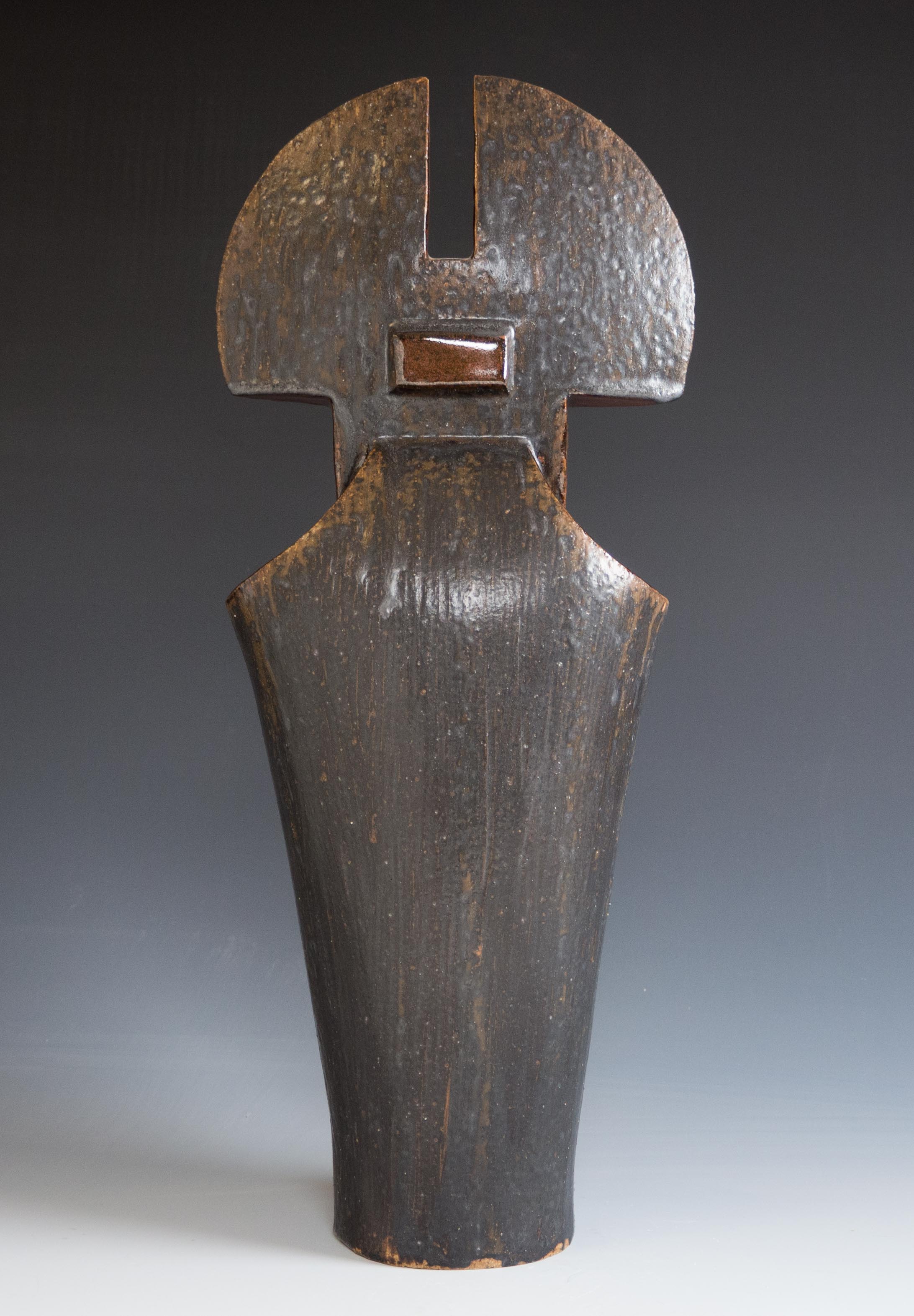
This picture has its own page with more detail, click here to see it.
This glaze is 49% Wood Ash, 24% Soda Feldspar and 27% Ball Clay. 10 copper carbonate and 10 manganese dioxide are added to that. This beautiful sculpture was made by Dan Ingersoll, aesthetically this glaze is perfect for it. But there are two red flags here. Significant manganese and copper metal fumes are certain to be generated at cone 10 (they are seriously not healthy) so anyone using this must be very careful. But there is something much more serious - this glaze is being used on functional ware. Copper is well known to destabilize other metals in the fired glass. This 10:10 combination is a perfect storm for leaching heavy metal into food and drink. This is not an argument for the use of commercial glazes, it is one for common sense application of the concept of limit recipes.
TGA-DTA Sample curve for Copper Carbonate
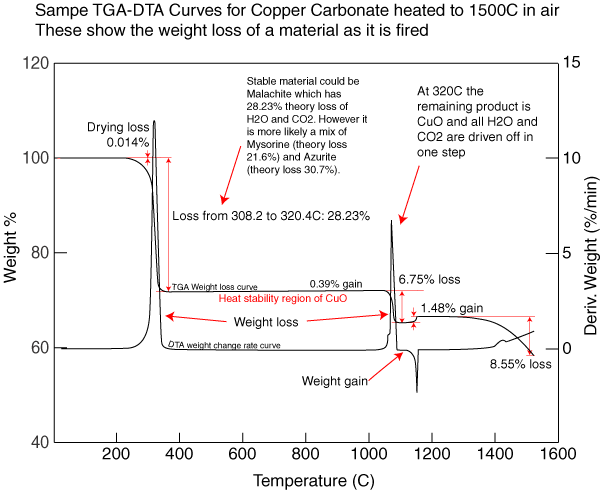
This picture has its own page with more detail, click here to see it.
Malachite diagram

This picture has its own page with more detail, click here to see it.
Copper Carbonate is beginning to melt. When?
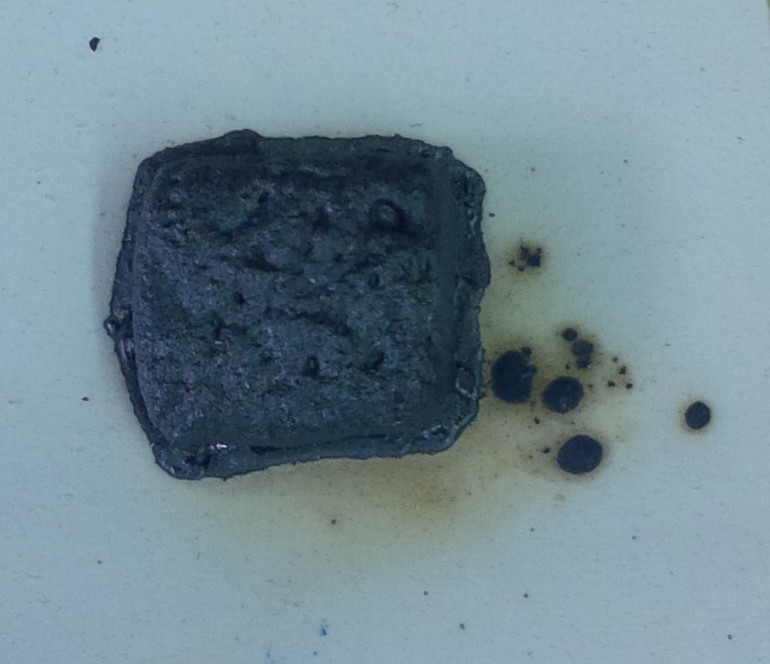
This picture has its own page with more detail, click here to see it.
Copper carbonate is beginning to melt at 2000F (this same sample was fired to 1950F, while shrunk to less than half its size, it was not melting yet).
Copper carbonate powder
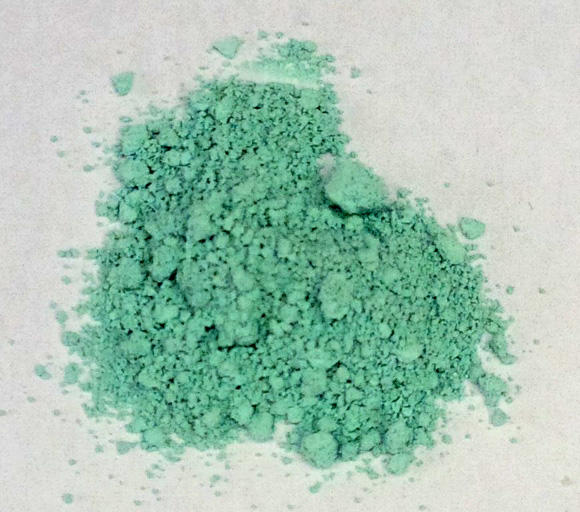
This picture has its own page with more detail, click here to see it.
LOI test of common materials flags copper carbonate
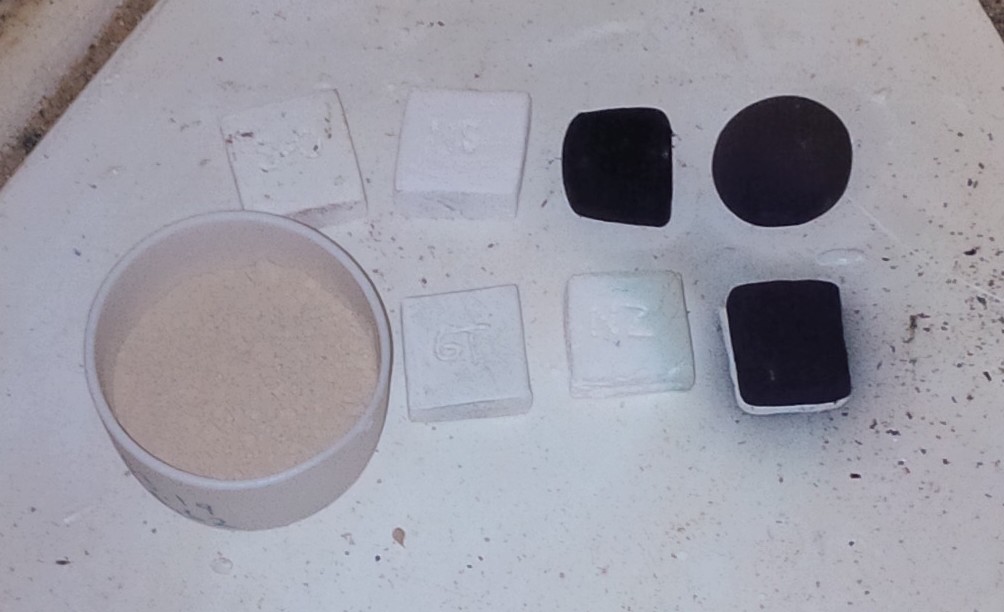
This picture has its own page with more detail, click here to see it.
These are pure samples (with 2% binder added) of (top left to bottom right) strontium carbonate, nepheline syenite, cobalt carbonate, manganese dioxide, bentonite (in bowl), 6 Tile kaolin, New Zealand kaolin and copper carbonate. I am firing them at 50F increments from 1500F and weighing to calculate loss on ignition for each. I want to find out at what temperature they are gassing (and potentially bubble-disrupting the glaze they are in or under). Notice how the copper is fuming and spitting black specks on the shelf, this happens right around 1500F (these stains on the shelf darkened considerably when the kiln was fired higher). Yet copper carbonate does not melt and fully decompose until much higher. No wonder it is implicated in cases of glaze blistering and bubbling.
Pure cobalt carbonate and copper carbonate at 1850F
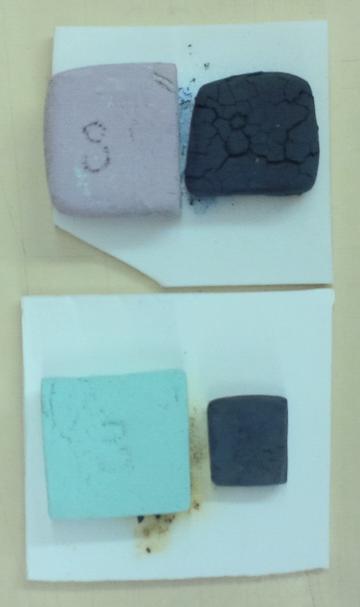
This picture has its own page with more detail, click here to see it.
Cobalt carbonate (top) and copper carbonate (bottom). Left is the raw powder plastic-formed into a sample (with 2% veegum). Right: fired to 1850F. The CuCO3 is quickly densifying over the past 100 degrees and should begin to melt soon. It is long past the fuming stage.
2% Copper carbonate in two different cone 6 copper-blues
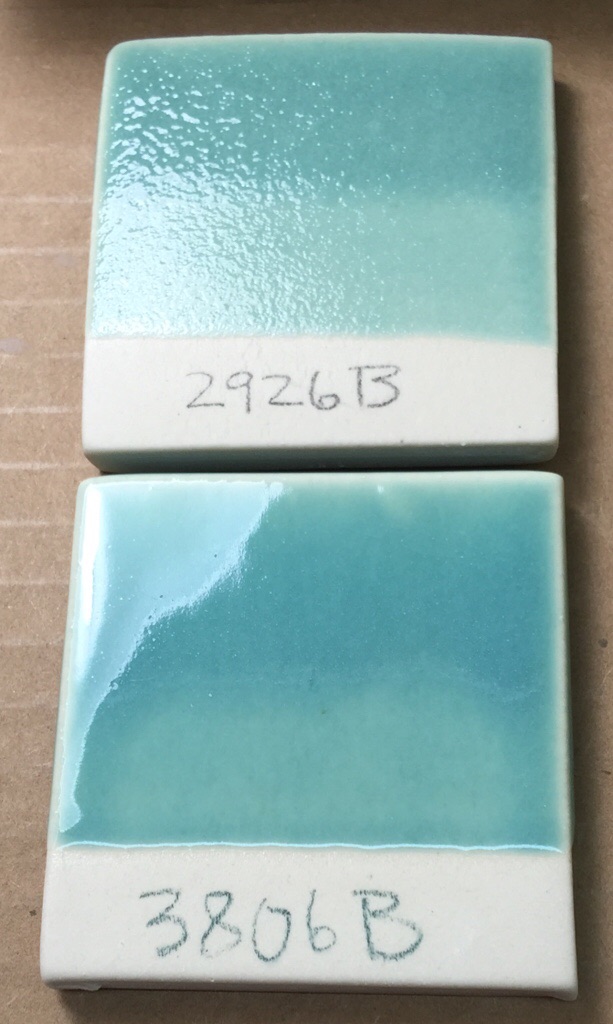
This picture has its own page with more detail, click here to see it.
The top base glaze has just enough melt fluidity to produce a brilliant transparent (without colorant additions). However it does not have enough fluidity to pass the bubbles and heal over from the decomposition of this added copper carbonate! Why is lower glaze passing the bubbles? How can it melt better yet have 65% less boron? How can it not be crazing when the COE calculates to 7.7 (vs. 6.4)? First, it has 40% less Al2O3 and SiO2 (which normally stiffen the melt). Second, it has higher flux content that is more diversified (it adds two new ones: SrO, ZnO). That zinc is a key to why it is melting so well and why it starts melting later (enabling unimpeded gas escape until then). It also benefits from the mixed-oxide-effect, the diversity itself improves the melt. And the crazing? The ZnO obviously pushes the COE down disproportionately to its percentage.
1% and 2% copper carbonate in a cone 6 transparent
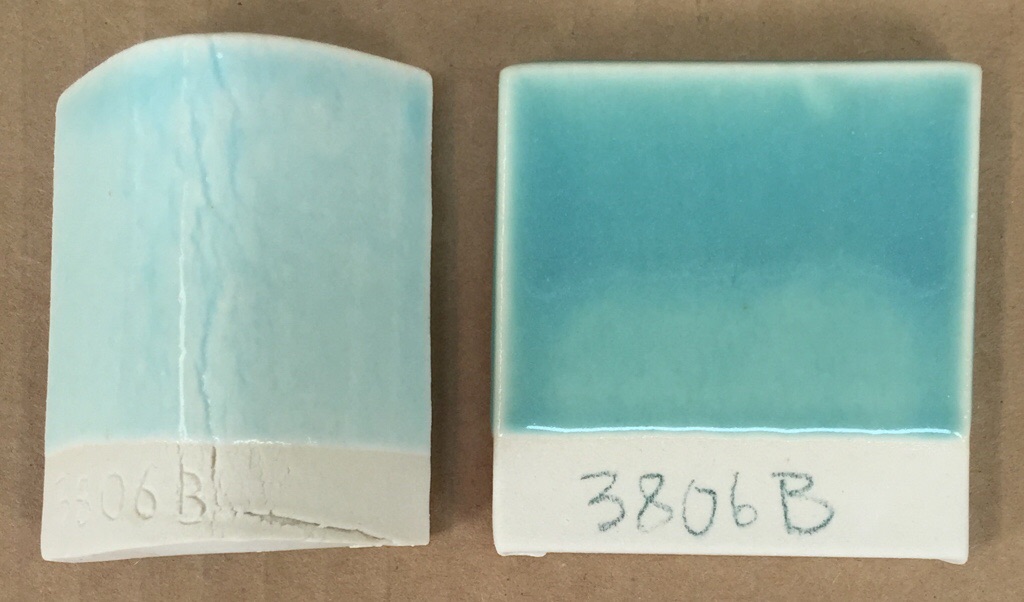
This picture has its own page with more detail, click here to see it.
The recipe also contains 2.5% tin oxide. The clear base is the best we found to host the copper blue effect (this is actually one we recalculated to source the Al2O3 more from clay and less from feldspar to get much better slurry properties). Other base recipes are more fluid, blister more easily, the slurry does not work as well and they are not as blue. There is an Insight-live.com share to see the recipe and notes at http://insight-live.com/insight/share.php?show=ruY3muruhJ1
Copper fluxes a matte glaze at cone 6
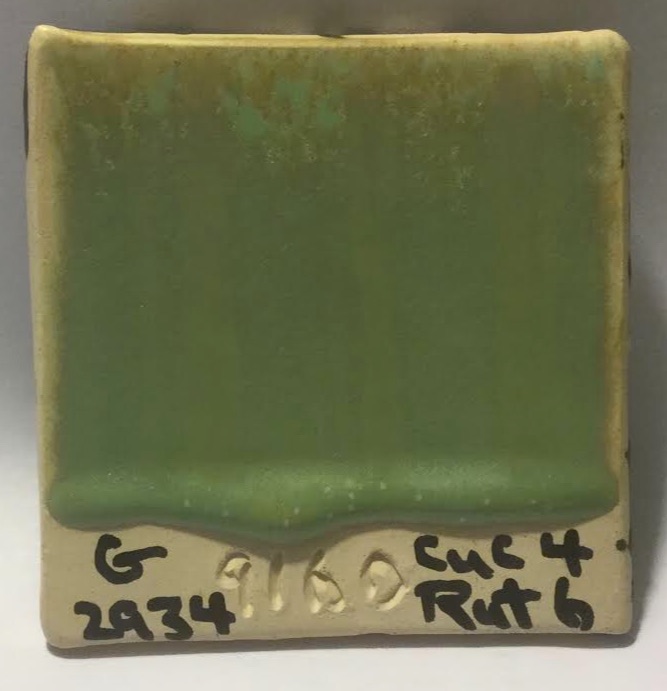
This picture has its own page with more detail, click here to see it.
4% copper carbonate and 6% rutile have been added to G2934 cone 6 matte base. Using a green stain should prevent this. Or some B2O3 could be substituted with SiO2 (via glaze chemistry).
Example of a data sheet for Copper Carbonate
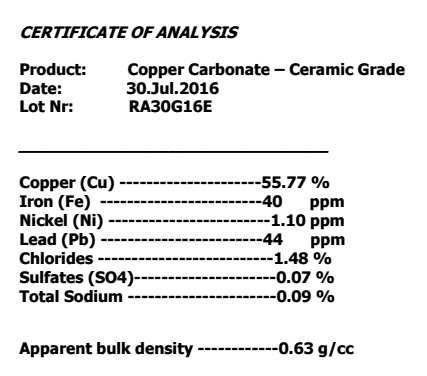
This picture has its own page with more detail, click here to see it.
Notice it does not quote the amount of CuCO3, just Cu metal. It also does not quote LOI percentage (weight loss on ignition, it will be more than 25%). Theoretical copper carbonate is 71.94% CuO (sourced by a mix of copper carbonate and carbonate hydroxide). CuO is 79.9% copper and 20.1% oxygen. Thus, we would expect Cu metal to be 57.5% (in a theoretical material). Since this example has impurities it is a little less, 55.8%.
Switching copper carbonate for copper oxide in a fluid glaze
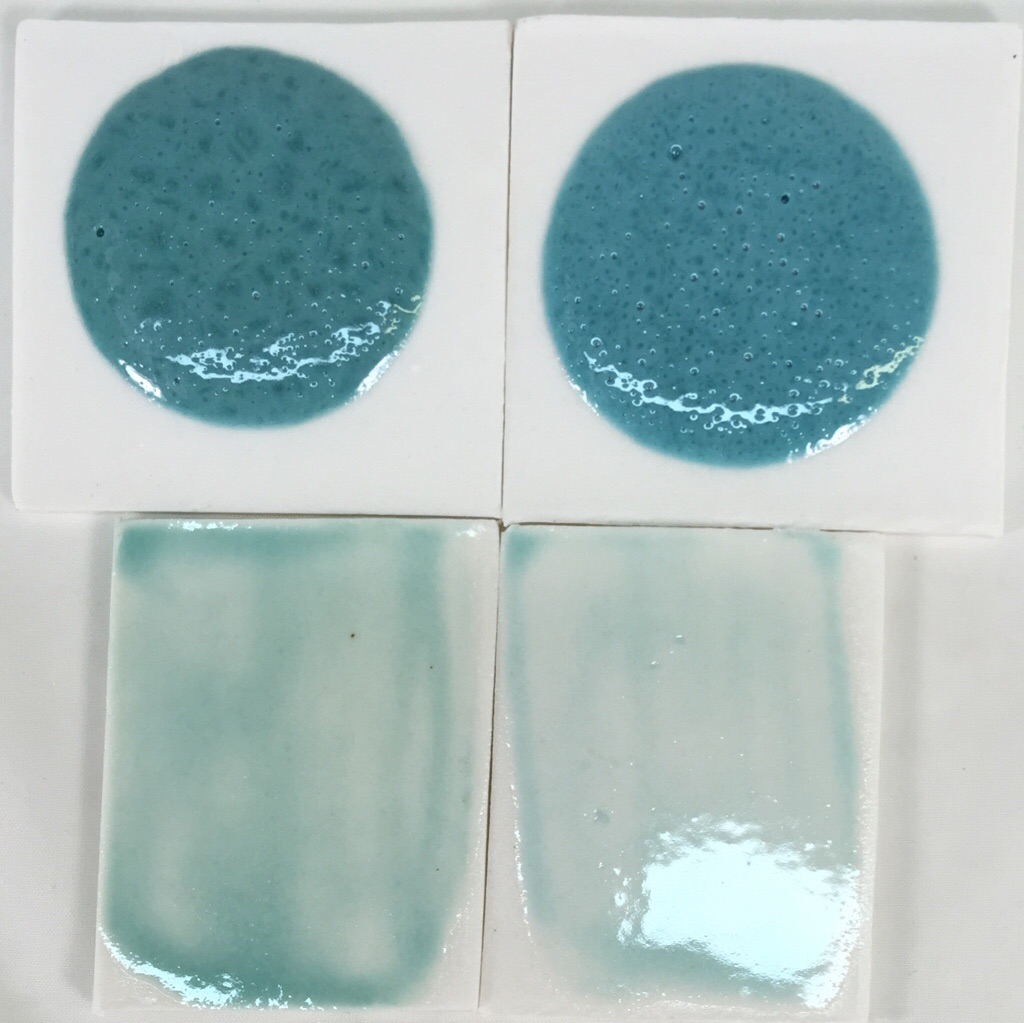
This picture has its own page with more detail, click here to see it.
The top samples are 10 gram GBMF test balls melted down onto porcelain tiles at cone 6 (this is a high melt fluidity glaze). These balls demonstrate melt mobility and susceptibility to bubbling but also color (notice how washed out the color is for thin layers on the bottom two tiles). Both have the same chemistry but recipe 2 has been altered to improve slurry properties.
Left: Original recipe with high feldspar, low clay (poor suspending) using 1.75% copper carbonate.
Right: New recipe with low feldspar, higher clay (good suspending) using 1% copper oxide.
The copper oxide recipe is not bubbling any less even though copper oxide does not gas. The bubbles must be coming from the kaolin.
Comparing the melt fluidity of four copper blue cone 6 glazes
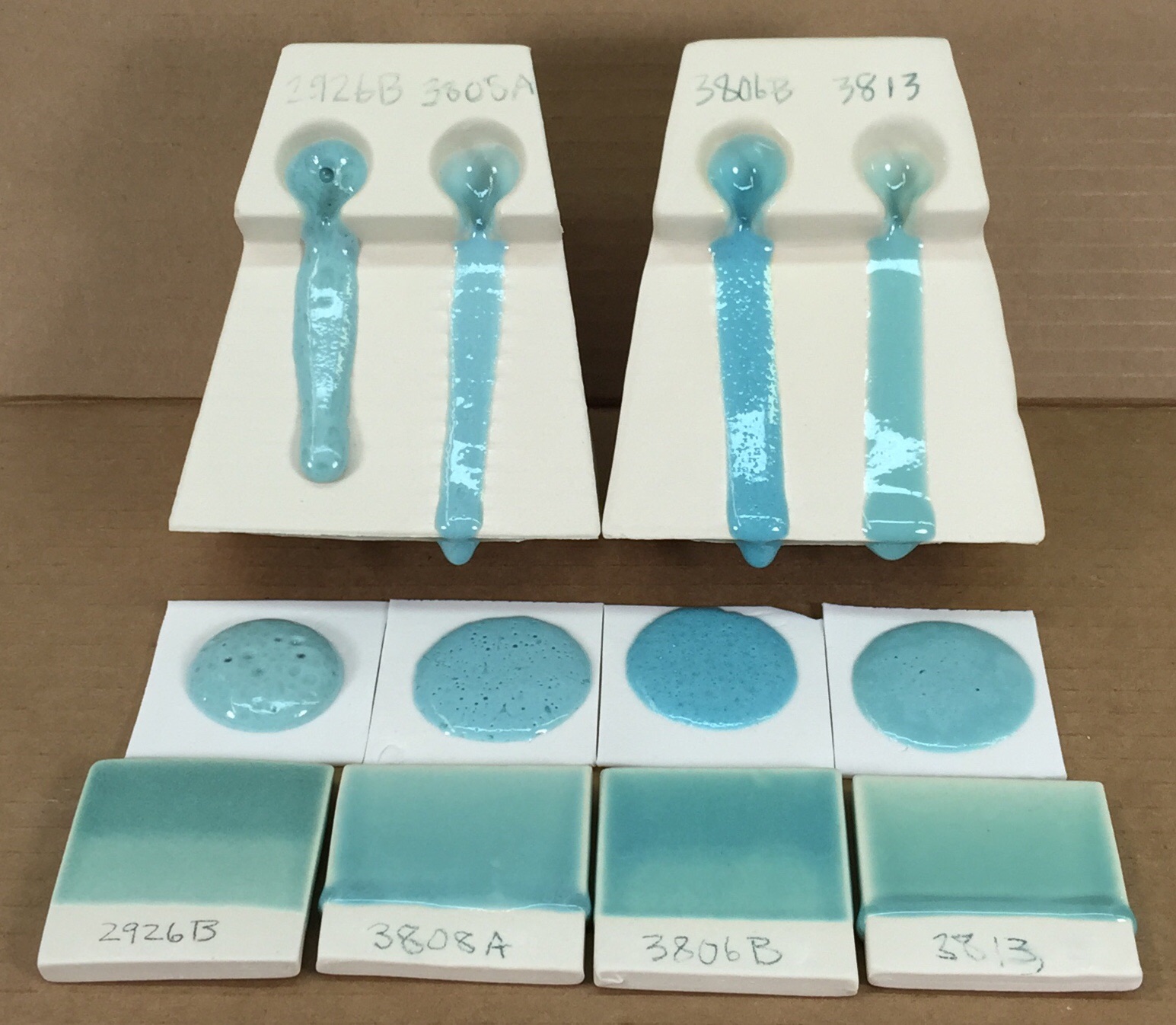
This picture has its own page with more detail, click here to see it.
The first glaze is a control, a standard non-fluid clear with copper. The other three are the short-listed ones in my project to find a good copper blue recipe starting recipe and fix its problems (which they all have).
The GLFL testers for melt flow at the back and the GBMF test melt-down-balls in front contain 1% copper carbonate. The glazed samples in the front row have 2% copper carbonate. L3806B, an improvement on the Panama Blue recipe, has the best color and the best compromise of flow and bubble clearing ability.
Links