All Articles
A ChatBot gives jaw-dropping glaze recipe advice - Jan 2025A Low Cost Tester of Glaze Melt FluidityA One-speed Lab or Studio Slurry MixerA Textbook Cone 6 Matte Glaze With ProblemsAdjusting Glaze Expansion by Calculation to Solve ShiveringAlberta Slip, 20 Years of Substitution for Albany SlipAn Overview of Ceramic StainsAre You in Control of Your Production Process?Are Your Glazes Food Safe or are They Leachable?Attack on Glass: Corrosion Attack MechanismsBall Milling Glazes, Bodies, EngobesBinders for Ceramic BodiesBringing Out the Big Guns in Craze Control: MgO (G1215U)Can We Help You Fix a Specific Problem?Ceramic Glazes TodayCeramic Material NomenclatureCeramic Tile Clay Body FormulationChanging Our View of GlazesChemistry vs. Matrix Blending to Create Glazes from Native MaterialsConcentrate on One Good GlazeCopper Red GlazesCrazing and Bacteria: Is There a Hazard?Crazing in Stoneware Glazes: Treating the Causes, Not the SymptomsCreating a Non-Glaze Ceramic Slip or EngobeCreating Your Own Budget GlazeCrystal Glazes: Understanding the Process and MaterialsDeflocculants: A Detailed OverviewDemonstrating Glaze Fit Issues to StudentsDiagnosing a Casting Problem at a Sanitaryware PlantDrying Ceramics Without CracksDuplicating Albany SlipDuplicating AP Green FireclayElectric Hobby Kilns: What You Need to KnowFighting the Glaze DragonFiring Clay Test BarsFiring: What Happens to Ceramic Ware in a Firing KilnFirst You See It Then You Don't: Raku Glaze StabilityFixing a glaze that does not stay in suspensionFormulating a body using clays native to your areaFormulating a Clear Glaze Compatible with Chrome-Tin StainsFormulating a PorcelainFormulating Ash and Native-Material GlazesG1214M Cone 5-7 20x5 glossy transparent glazeG1214W Cone 6 transparent glazeG1214Z Cone 6 matte glazeG1916M Cone 06-04 transparent glazeGetting the Glaze Color You Want: Working With StainsGlaze and Body Pigments and Stains in the Ceramic Tile IndustryGlaze Chemistry Basics - Formula, Analysis, Mole%, Unity Glaze chemistry using a frit of approximate analysisGlaze Recipes: Formulate and Make Your Own InsteadGlaze Types, Formulation and Application in the Tile IndustryHaving Your Glaze Tested for Toxic Metal ReleaseHigh Gloss GlazesHire Us for a 3D Printing ProjectHow a Material Chemical Analysis is DoneHow desktop INSIGHT Deals With Unity, LOI and Formula WeightHow to Find and Test Your Own Native ClaysI have always done it this way!Inkjet Decoration of Ceramic TilesIs Your Fired Ware Safe?Leaching Cone 6 Glaze Case StudyLimit Formulas and Target FormulasLow Budget Testing of Ceramic GlazesMake Your Own Ball Mill StandMaking Glaze Testing ConesMonoporosa or Single Fired Wall TilesOrganic Matter in Clays: Detailed OverviewOutdoor Weather Resistant CeramicsPainting Glazes Rather Than Dipping or SprayingParticle Size Distribution of Ceramic PowdersPorcelain Tile, Vitrified TileRationalizing Conflicting Opinions About PlasticityRavenscrag Slip is BornRecylcing Scrap ClayReducing the Firing Temperature of a Glaze From Cone 10 to 6Setting up a Clay Testing Program in Your CompanySimple Physical Testing of ClaysSingle Fire GlazingSoluble Salts in Minerals: Detailed OverviewSome Keys to Dealing With Firing CracksStoneware Casting Body RecipesSubstituting Cornwall StoneSuper-Refined Terra SigillataThe Chemistry, Physics and Manufacturing of Glaze FritsThe Effect of Glaze Fit on Fired Ware StrengthThe Four Levels on Which to View Ceramic GlazesThe Majolica Earthenware ProcessThe Potter's PrayerThe Right Chemistry for a Cone 6 MgO MatteThe Trials of Being the Only Technical Person in the ClubThe Whining Stops Here: A Realistic Look at Clay BodiesThose Unlabelled Bags and BucketsTiles and Mosaics for PottersToxicity of Firebricks Used in OvensTrafficking in Glaze RecipesUnderstanding Ceramic MaterialsUnderstanding Ceramic OxidesUnderstanding Glaze Slurry PropertiesUnderstanding the Deflocculation Process in Slip CastingUnderstanding the Terra Cotta Slip Casting Recipes In North AmericaUnderstanding Thermal Expansion in Ceramic GlazesUnwanted Crystallization in a Cone 6 GlazeUsing Dextrin, Glycerine and CMC Gum togetherVolcanic AshWhat Determines a Glaze's Firing Temperature?What is a Mole, Checking Out the MoleWhat is the Glaze Dragon?Where do I start in understanding glazes?Why Textbook Glazes Are So DifficultWorking with children The Four Levels on Which to View Ceramic Glazes
Description
By knowing which level to view a glaze from you are much better equipped to understand and control it. The levels are process, recipe, material, oxide.
Article
Glazing is perhaps the most difficult aspect of ceramics and the one for which you bear the most accountability (for design, functionality, and safety). It is important to know 'why' glazes do what they do. It is better to 'understand' and control a few glazes than struggle with many that end up controlling you. The traffic in glaze recipes and the trend toward abdicating control to suppliers and consultants, these mentalities breed ignorance and invite trouble. The answer is to formulate your own glazes.
To understand the complexities of glazes one must marshal several different viewpoints, that is, understand things on different levels. There is usually no one simple answer for formulating or fixing a glaze. We recommend you develop the ability to determine which level is most closely related to the problem at hand. Study the trouble shooting articles at the bottom on this page and note how thinking in terms of these four levels helps to formulate questions that lead to solutions.
The Process Level
The technician immerses himself in understanding the equipment used to apply, dry, decorate, fire, and cool the ware. By fine tuning these devices he exercises considerable control over standard plant or studio recipes or glazes purchased ready made from suppliers. When problems arise he/she analyses them mainly in terms of changes he can make to the process.
The Recipe Level
The technician test mixes many glaze recipes or commercially prepared glazes hoping to find one that 'appears' to be visually suitable. When problems are encountered, a recipe is often discarded and the pursuit of another begins. On this level little is learned when a recipe does not work properly. Leaching and crazing 'consciences' tend to be underdeveloped. People trapped in this culture tend to feel quite helpless, glazes are 'mysterious' to them. Many want to have guaranteed solutions handed to them yet they are very tolerant of touchy, difficult, and expensive recipes. Many believe the 'fool proof' recipe is just around the corner.
The Material Level
The technician learns what materials do when fired and uses trial and error blending to produce glazes. He is able to achieve a degree control over the fired visual character and gains confidence. Much more is learned when glazes do not fire as expected. The physical working properties of glazes can be rationalized according to the properties of the components and adjustments made to improve application or mixing properties while maintaining fired characteristics. This approach is particularly applicable to decorative and non-functional products where the pursuit of interesting surfaces is very important. However this method falls short when it comes to producing functional surfaces and exercising greater control of diverse fired properties. Material level formulation tends to perpetuate the acceptance of results based on visual appearance only. Flux saturated glazes are examples of the products of this approach, yet they are usually unstable against chemical or mechanical attack.
The Oxide Level
The technician understands the function of oxides, the building blocks of the final fired glass. He has much greater control of many fired properties that are related directly to specific oxides or oxide systems. When problems occur this level often teaches valuable lessons that can be applied to solve current and future problems. When both the material and oxide levels are considered the technician can achieve a measure of 'material independence' (he can choose what mix of materials is best to supply a given formula of oxides). While things like blistering and crawling can be understood best by considering both the material and oxide mix of a glaze, issues like crazing and color development can only be fully grasped by consideration at this level. Each oxide has well documented contributions and interactions with others in the fired glass and proper understanding of the oxide level provides strategies for dealing with all kinds of glaze properties (i.e. hardness, surface character, crystal development, chemical stability).
We encourage you to learn about materials and ceramic calculations.
Related Information
The Dragon
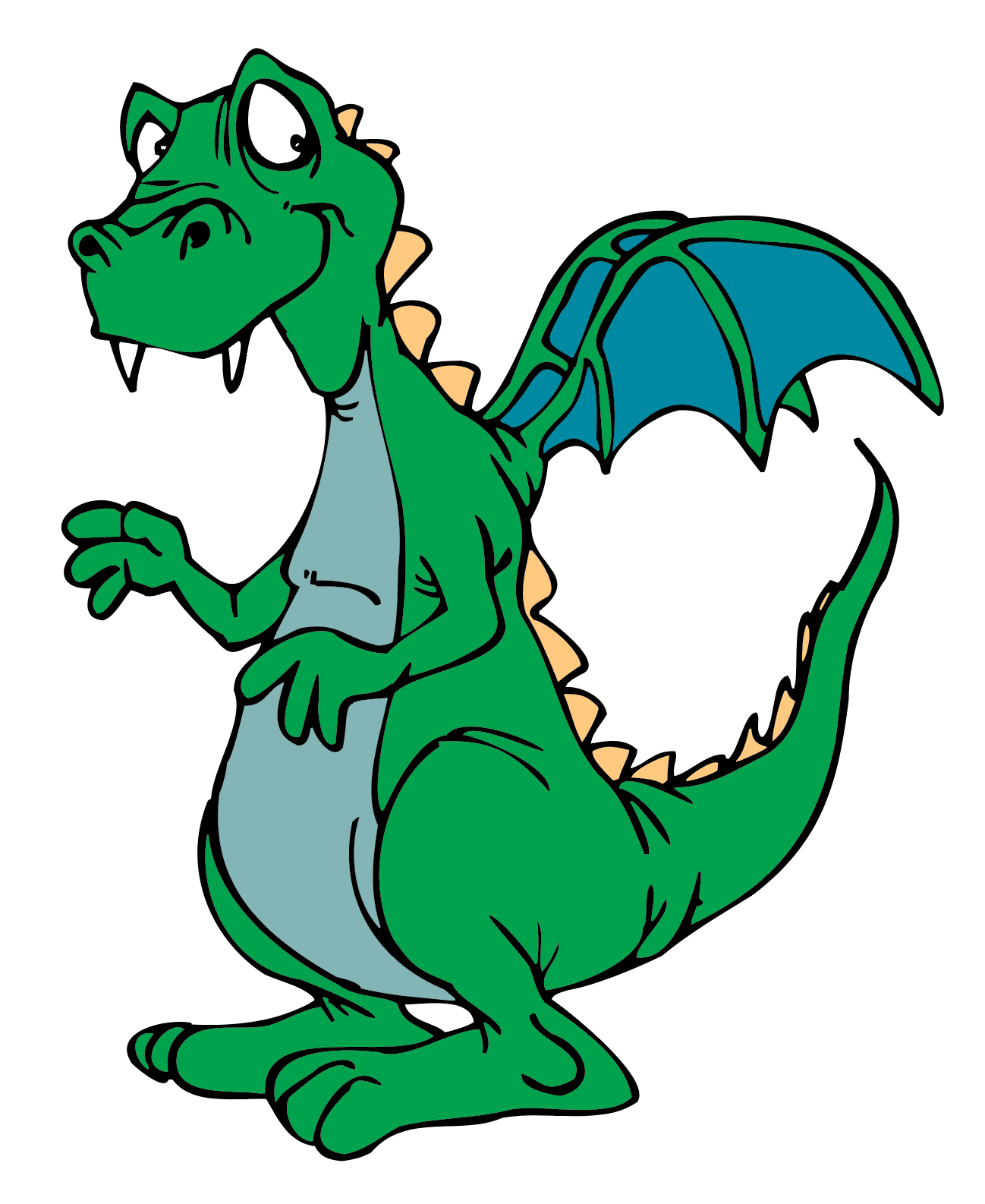
This picture has its own page with more detail, click here to see it.
This is how we personify the challenges facing willfully non-technical ceramic technicians. He is not as harmless as he looks. And he is not out for your best interests.
Links