Notes
The Mason reference guides states that this "can be used as a 'body stain' in porcelain at high temperatures". However we find that it works well as a body and engobe stain at any temperature. They indicate a maximum firing limit 2300 degrees F (1260 degrees C) and that free zinc oxide influences the color more than any other element. They state that "generally, zincless glazes should not contain magnesium oxide". However the G2934 is a zinc-free high-MgO matte and this stain works very well, even at low percentages.
Old Number: 158
Related Information
Mason stains in the G2926B base glaze at cone 6
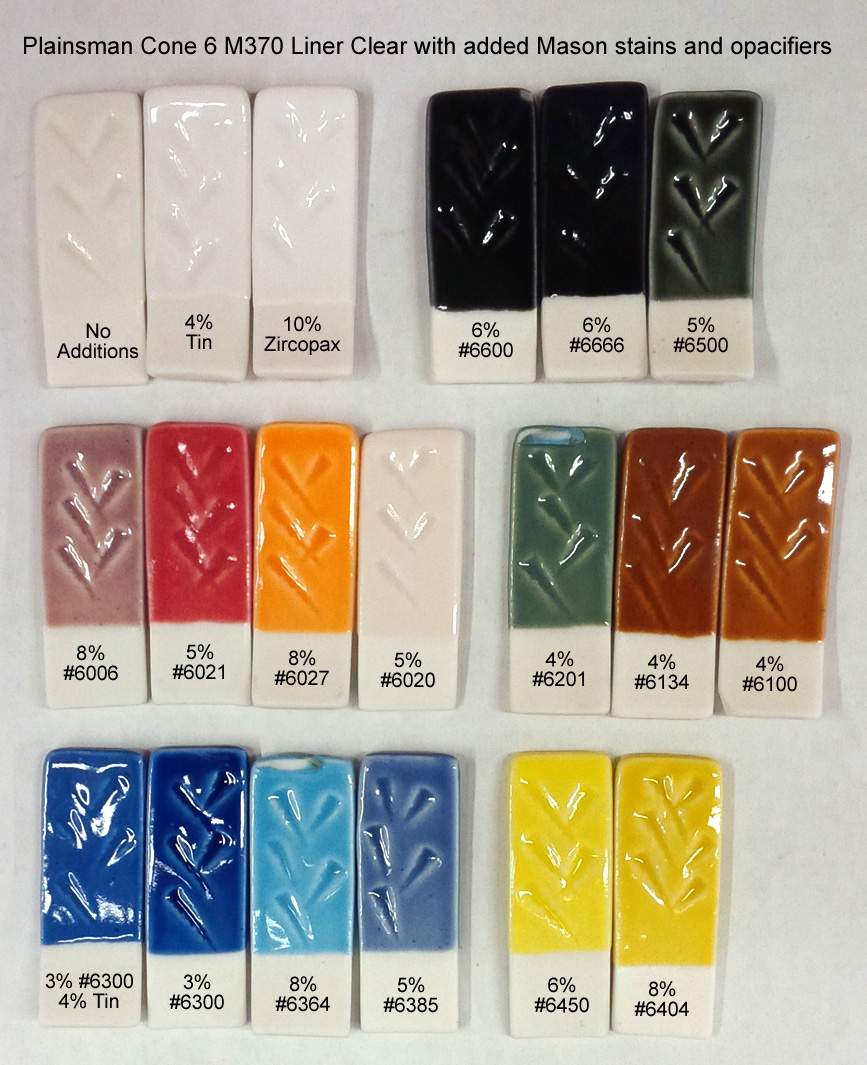
This picture has its own page with more detail, click here to see it.
This glaze, G2926B, is our main glossy base recipe. Stains are a much better choice for coloring it than raw metal oxides. Other than the great colors they produce here, there are a number of things worth noticing. Stains are potent; the percentages needed are normally much less than for metal oxides. Staining a transparent glaze produces a transparent color, it is more intense where the laydown is thicker - this is often desirable in highlighting contours and designs. For pastel shades, add an opacifier (e.g. 5-10% Zircopax, more stain might be needed to maintain the color intensity). The chrome-tin maroon 6006 does not develop well in this base (alternatives are G2916F or G1214M). The 6020 manganese alumina pink is also not developing here (it is a body stain). Caution is required with inclusion stains (like #6021). Bubbling, as is happening here, is common - this can be mitigated by adding 1-2% Zircopax. And it’s easy to turn any of these into brushing or dipping glazes.
Tuning the degree of gloss on a matte black glaze
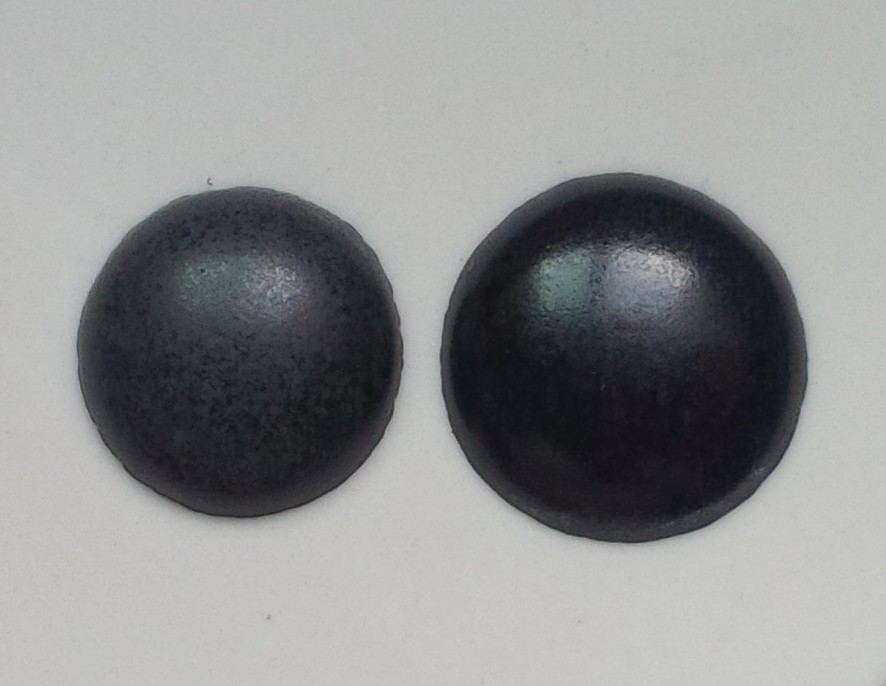
This picture has its own page with more detail, click here to see it.
These 10-gram balls were fired and melted down onto a tile. The one on the left is the original G2934 Plainsman Cone 6 MgO matte with 6% Mason 6600 black stain. On the right, the adjustment has a 20% glossy G2926B glaze addition to make it a little less matte. Notice the increased flow (the ball has flattened more) with the addition of the glossy. In addition, while the percentage of stain in the one on the right is actually less (because of the dilution of the transparent), the color appears darker! Tuning the degree of matteness when making color additions is not just for appearance, for functional ware it is also about achieving a surface that does not cutlery mark and is not leaching heavy metals.
Absolutely Jet-Black Cone 6 Engobe on M340
This could also be super white
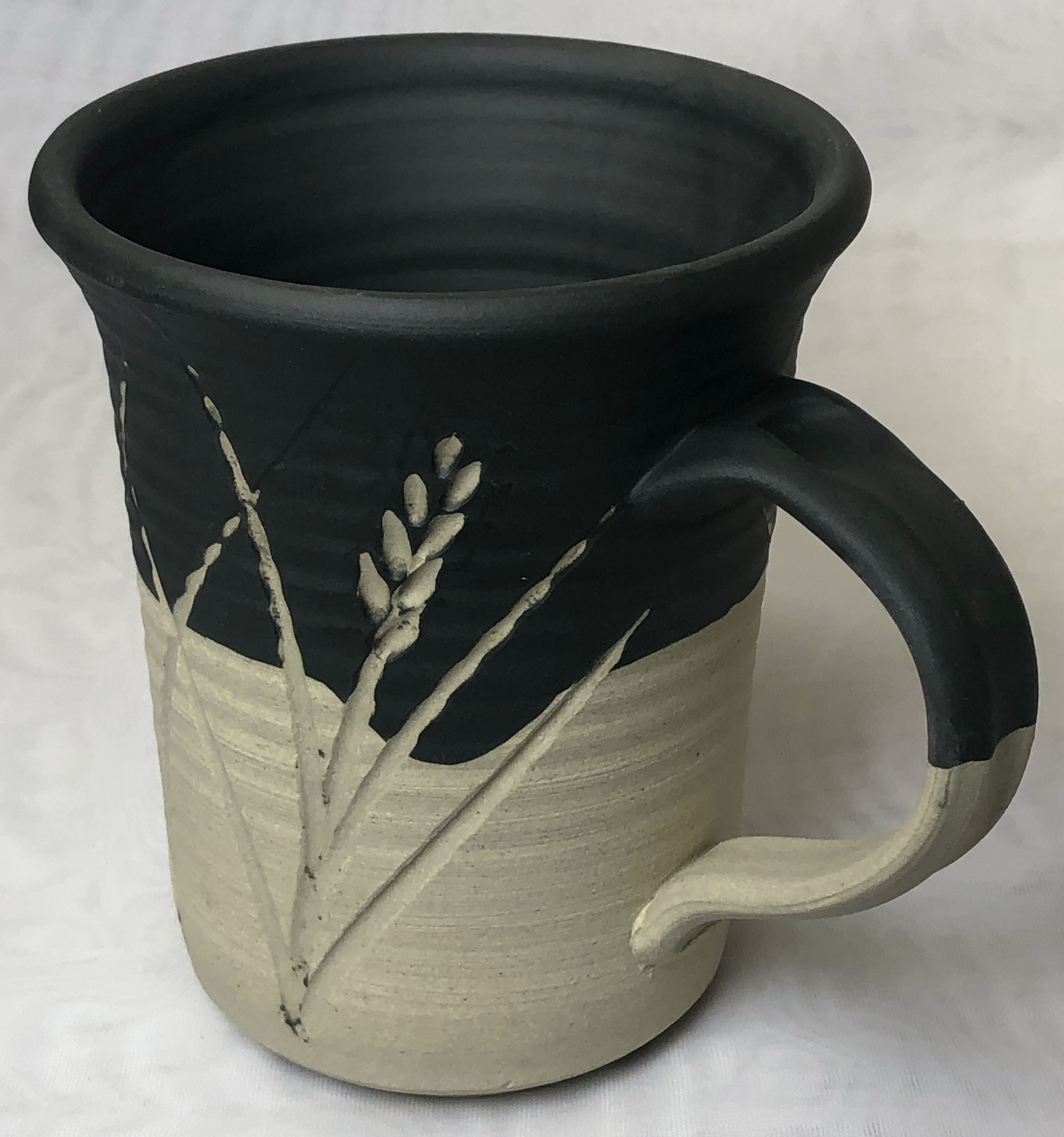
This picture has its own page with more detail, click here to see it.
This is the L3954B engobe. 15% Mason 6600 black body stain has been added (instead of the normal 10% Zircopax used for white). Of course, a cover glaze is needed for a functional surface. We put a lot of development work into producing a recipe fits this body, M340. It works even when thickly applied because it has the same fired maturity as the body. Lots of information is available on using L3954B (including mixing and adjustment instructions). Engobes are tricky to use, follow the links below to learn more. L3954B is designed to work on regular Plainsman M340 (this piece), M390 and Coffee Clay. Most important we document how to adjust its maturity, and thus firing shrinkage, to fine tune fit if needed. These bodies dry better than porcelains and are much less expensive, so coating them with an engobe to get a surface like this makes a lot of sense. Ed Phillipson discovered this 80 years ago, enabling selling ware made from these clays as white hotel ware.
Stunning black silky matte glaze at cone 6
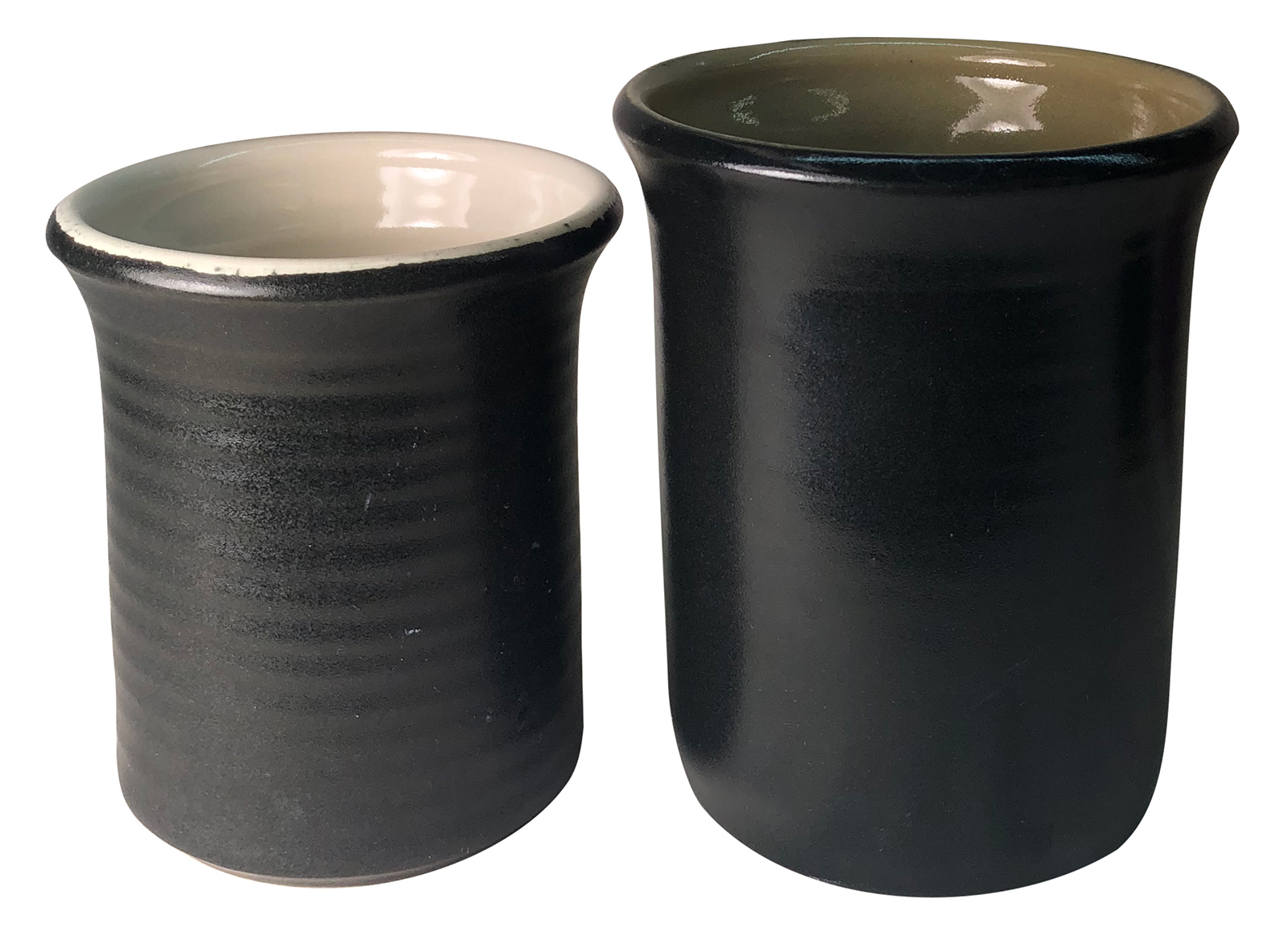
This picture has its own page with more detail, click here to see it.
This contains 6% Mason 6600 black stain (Mason 6666 gives dark brown, don't use it). The base recipe, G2934, is an excellent balanced-chemistry host for a wide range of stains to produce equally stunning reds, yellows, oranges, etc. The fritted version of the recipe, G2934Y, provides an even better host. This glaze is affected by the clay it is on. The body on the right is highly vitreous, this has produced a finer texture that glistens in the light. The body on the left is a whiteware having 1% porosity (Plainsman M370). Firing schedule is also a factor, slower cooling will dull the color more. We use the PLC6DS firing schedule.
L3954J black engobe on a cone 10R whiteware body
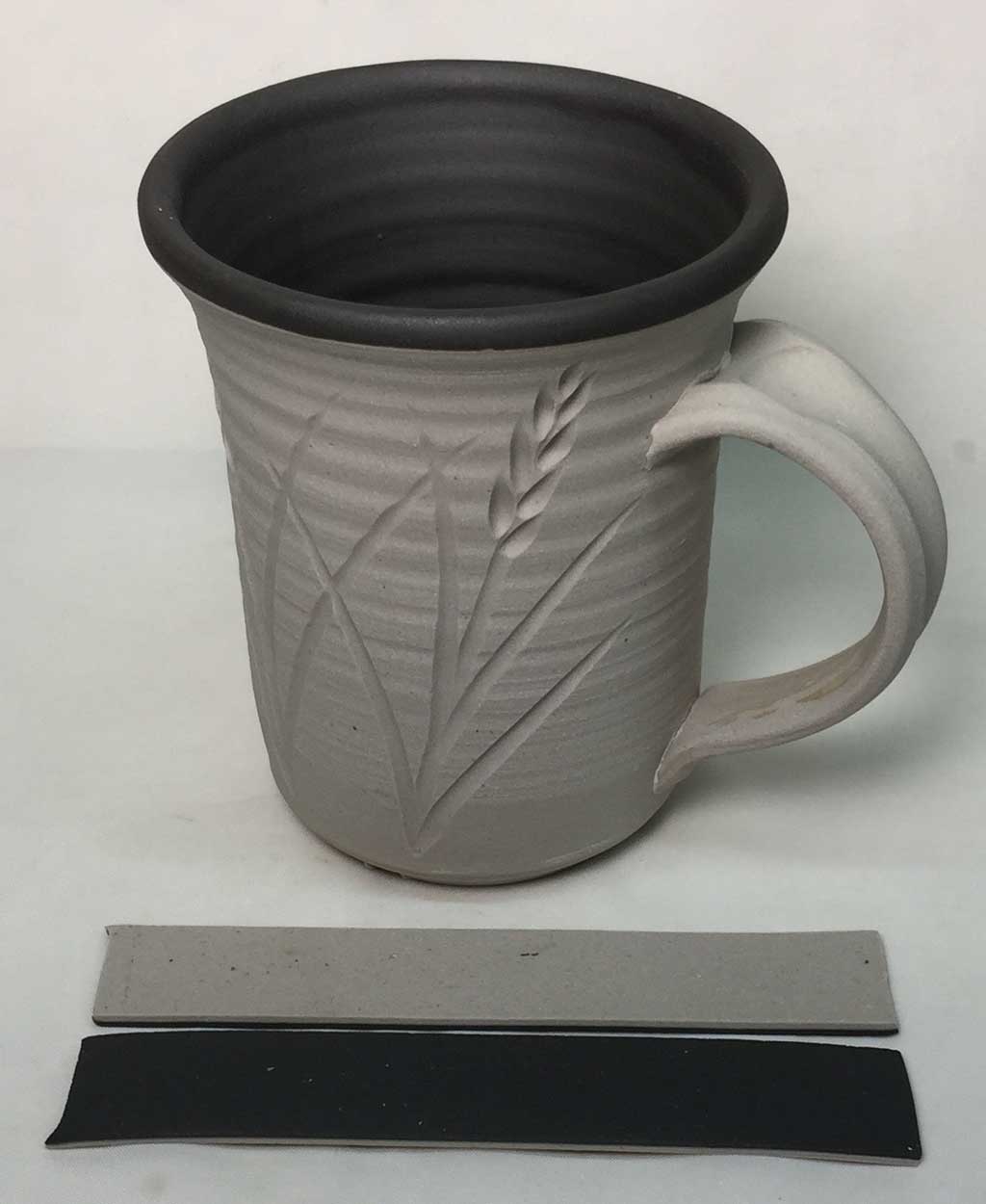
This picture has its own page with more detail, click here to see it.
The body is Plainsman H570 (0.5-1% porosity). This piece is not glazed. The firing schedule is C10RPL. Notice the EBCT test bars in front (engobe compatibility). These sandwich the body and the L3954J engobe together in a thin strip, differences in fired shrinkage curl the bar during firing (toward the one of higher shrinkage). The straighter the bars fire the better the fit. My regular engobe for use on our buff stoneware, L3954N (Plainsman H550, 2-3% porosity), has lower fired shrinkage than this (since that body is less vitreous). This one increases that shrinkage (with 5% more nepheline syenite, 5% less silica and 3% less ball clay). This employs 10% Mason 6600 stain to produce the jet-black fired product. 6600 is their cobalt black stain but the 6666 cobalt-free one should also work, both are suitable as body stains and recommended to 2300F (1260C) - cone 10 is technically above this limit but we have not encountered issues.
A gunmetal glaze I have wanted for decades!
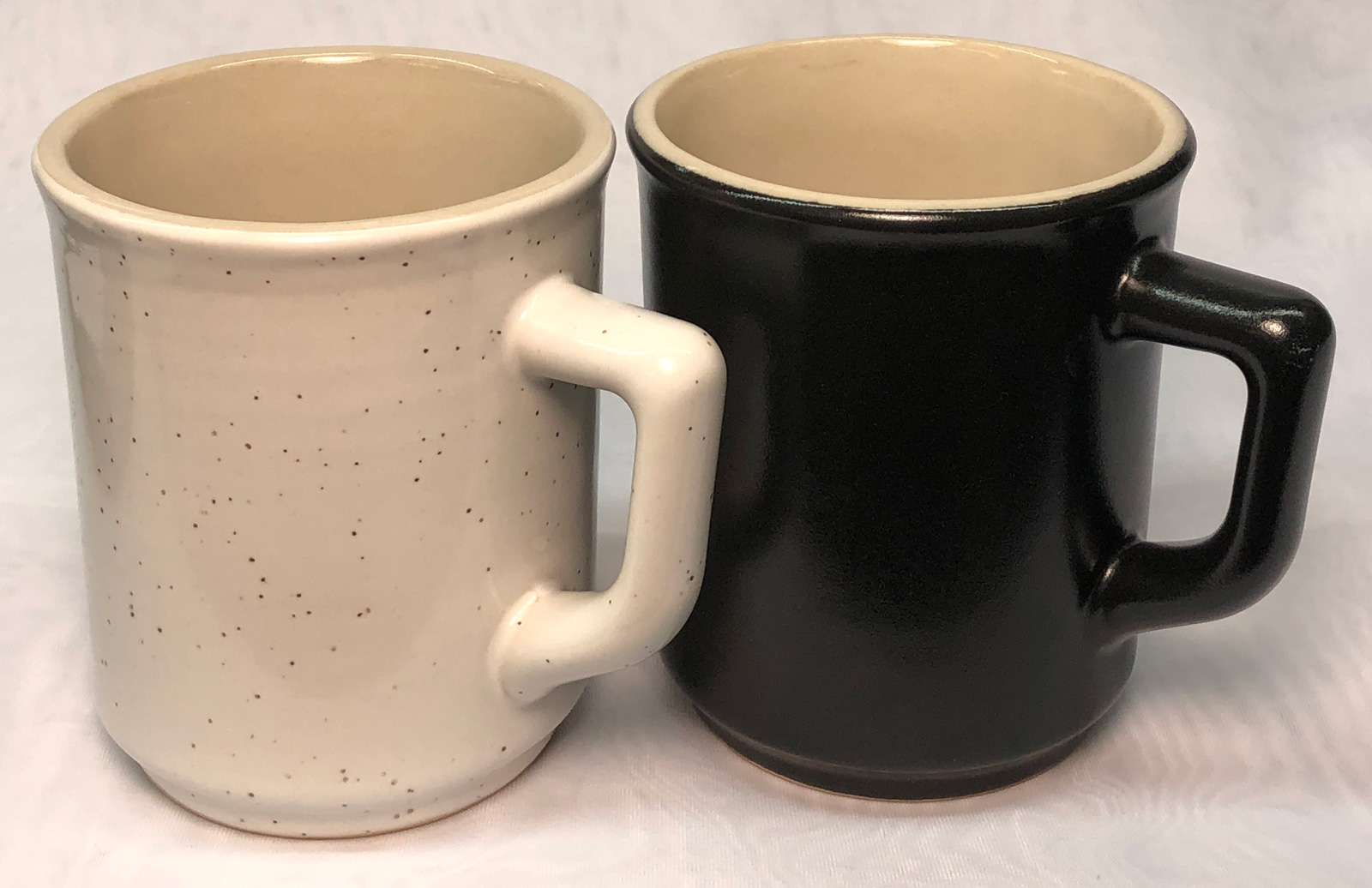
This picture has its own page with more detail, click here to see it.
I finally have a perfect functional, durable gunmetal black! It has an incredible silky surface. It does not cutlery mark. It does not craze on anything. It is easy to clean. This is G2934Y with 6% Mason 6600 black stain fired using the PLC6DS schedule. I had to tune it a bit, adding about 15% glossy G2926B, because it was a little too matte on initial firings. But now it is perfect. These are heavy mugs made using the M340 casting recipe (and the casting-jiggering process). The speckled mug was made by casting a thin layer of the speckled version of the slip first, then filling the mold with the regular slip. I used a 40-minute cast to get walls nice and thick!
Polar Ice Porcelain with Body Stains - by Robert Barritz
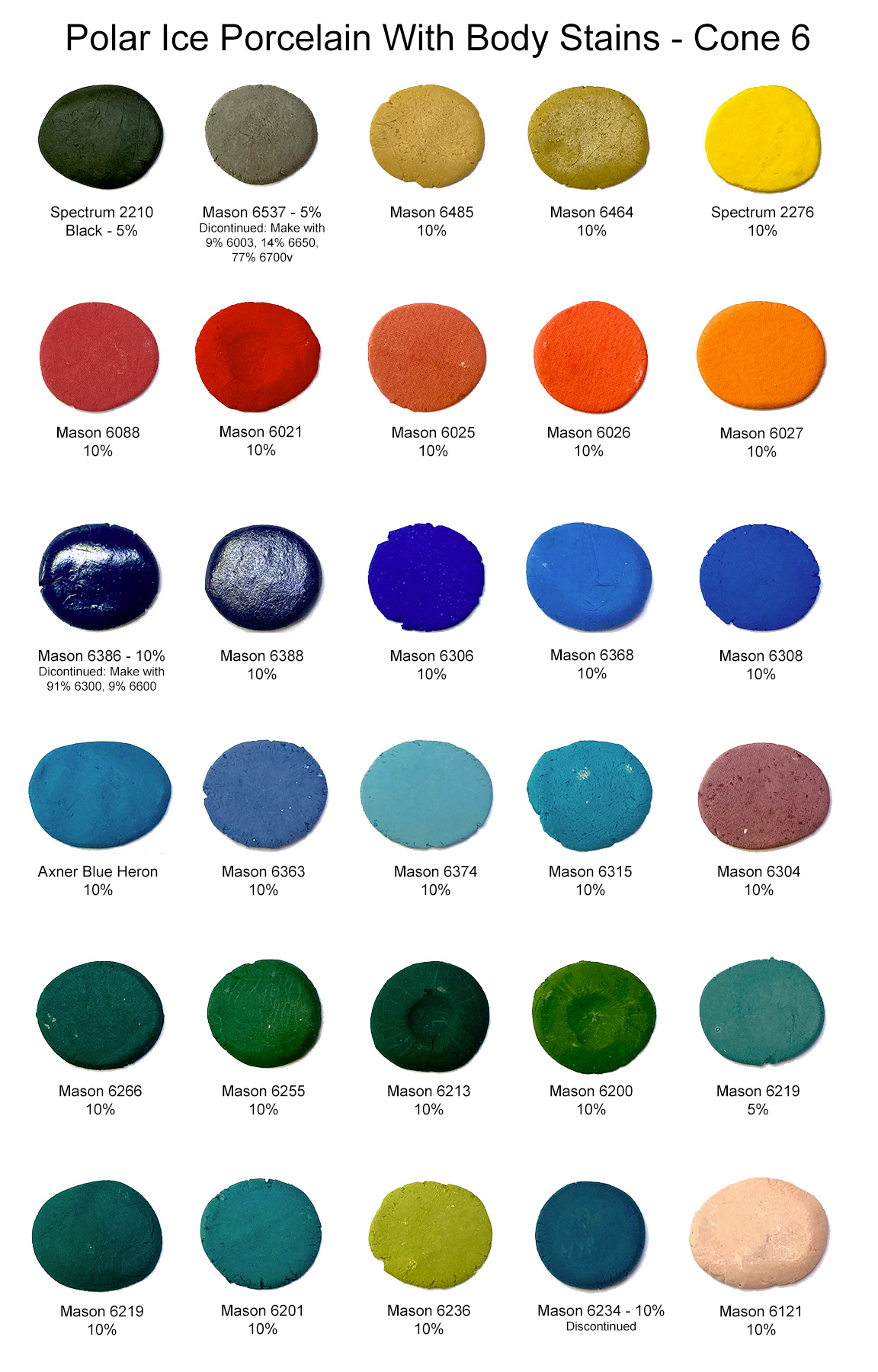
This picture has its own page with more detail, click here to see it.
Robert has done really valuable work in this research, what an amazing range of color! Surfaces are unpolished and unglazed. All are fired to cone 6. Browns are missing, they can be made using iron oxide. For blacks, Mason 6600 is also effective. The blues can be intense using lower percentages than shown here, as low as 2% can be effective. There is an optimal amount for each stain, beyond that, increases in percentage bring little increase in color intensity. There is another reason to keep stain percentages to a minimum: To reduce the impact on body maturity (and firing shrinkage). Blues, for example, can significantly heighten the degree of vitrification, even melting the porcelain. If you plan to marble different colors, keeping stain percentage as low as possible is even more important, unless you can do fired shrinkage compatibility testing, for example, the EBCT test. Need to develop your own white porcelain? See the link below.
Stains in bodies will usually bleed color into glazes used over them, especially if the body is vitreous. This can be leveraged to create or amplify variegation. Strangely, stains can increase micro bubbles in transparent glazes.
Links