All Articles
A ChatBot gives jaw-dropping glaze recipe advice - Jan 2025A Low Cost Tester of Glaze Melt FluidityA One-speed Lab or Studio Slurry MixerA Textbook Cone 6 Matte Glaze With ProblemsAdjusting Glaze Expansion by Calculation to Solve ShiveringAlberta Slip, 20 Years of Substitution for Albany SlipAn Overview of Ceramic StainsAre You in Control of Your Production Process?Are Your Glazes Food Safe or are They Leachable?Attack on Glass: Corrosion Attack MechanismsBall Milling Glazes, Bodies, EngobesBinders for Ceramic BodiesBringing Out the Big Guns in Craze Control: MgO (G1215U)Can We Help You Fix a Specific Problem?Ceramic Glazes TodayCeramic Material NomenclatureCeramic Tile Clay Body FormulationChanging Our View of GlazesChemistry vs. Matrix Blending to Create Glazes from Native MaterialsConcentrate on One Good GlazeCopper Red GlazesCrazing and Bacteria: Is There a Hazard?Crazing in Stoneware Glazes: Treating the Causes, Not the SymptomsCreating a Non-Glaze Ceramic Slip or EngobeCreating Your Own Budget GlazeCrystal Glazes: Understanding the Process and MaterialsDeflocculants: A Detailed OverviewDemonstrating Glaze Fit Issues to StudentsDiagnosing a Casting Problem at a Sanitaryware PlantDrying Ceramics Without CracksDuplicating Albany SlipDuplicating AP Green FireclayElectric Hobby Kilns: What You Need to KnowFighting the Glaze DragonFiring Clay Test BarsFiring: What Happens to Ceramic Ware in a Firing KilnFirst You See It Then You Don't: Raku Glaze StabilityFixing a glaze that does not stay in suspensionFormulating a body using clays native to your areaFormulating a Clear Glaze Compatible with Chrome-Tin StainsFormulating a PorcelainFormulating Ash and Native-Material GlazesG1214M Cone 5-7 20x5 glossy transparent glazeG1214W Cone 6 transparent glazeG1214Z Cone 6 matte glazeG1916M Cone 06-04 transparent glazeGetting the Glaze Color You Want: Working With StainsGlaze and Body Pigments and Stains in the Ceramic Tile IndustryGlaze Chemistry Basics - Formula, Analysis, Mole%, Unity Glaze chemistry using a frit of approximate analysisGlaze Recipes: Formulate and Make Your Own InsteadGlaze Types, Formulation and Application in the Tile IndustryHaving Your Glaze Tested for Toxic Metal ReleaseHigh Gloss GlazesHire Us for a 3D Printing ProjectHow a Material Chemical Analysis is DoneHow desktop INSIGHT Deals With Unity, LOI and Formula WeightHow to Find and Test Your Own Native ClaysI have always done it this way!Inkjet Decoration of Ceramic TilesIs Your Fired Ware Safe?Leaching Cone 6 Glaze Case StudyLimit Formulas and Target FormulasLow Budget Testing of Ceramic GlazesMake Your Own Ball Mill StandMaking Glaze Testing ConesMonoporosa or Single Fired Wall TilesOrganic Matter in Clays: Detailed OverviewOutdoor Weather Resistant CeramicsPainting Glazes Rather Than Dipping or SprayingParticle Size Distribution of Ceramic PowdersPorcelain Tile, Vitrified TileRationalizing Conflicting Opinions About PlasticityRavenscrag Slip is BornRecylcing Scrap ClayReducing the Firing Temperature of a Glaze From Cone 10 to 6Setting up a Clay Testing Program in Your CompanySimple Physical Testing of ClaysSingle Fire GlazingSoluble Salts in Minerals: Detailed OverviewSome Keys to Dealing With Firing CracksStoneware Casting Body RecipesSubstituting Cornwall StoneSuper-Refined Terra SigillataThe Chemistry, Physics and Manufacturing of Glaze FritsThe Effect of Glaze Fit on Fired Ware StrengthThe Four Levels on Which to View Ceramic GlazesThe Majolica Earthenware ProcessThe Potter's PrayerThe Right Chemistry for a Cone 6 MgO MatteThe Trials of Being the Only Technical Person in the ClubThe Whining Stops Here: A Realistic Look at Clay BodiesThose Unlabelled Bags and BucketsTiles and Mosaics for PottersToxicity of Firebricks Used in OvensTrafficking in Glaze RecipesUnderstanding Ceramic MaterialsUnderstanding Ceramic OxidesUnderstanding Glaze Slurry PropertiesUnderstanding the Deflocculation Process in Slip CastingUnderstanding the Terra Cotta Slip Casting Recipes In North AmericaUnderstanding Thermal Expansion in Ceramic GlazesUnwanted Crystallization in a Cone 6 GlazeUsing Dextrin, Glycerine and CMC Gum togetherVolcanic AshWhat Determines a Glaze's Firing Temperature?What is a Mole, Checking Out the MoleWhat is the Glaze Dragon?Where do I start in understanding glazes?Why Textbook Glazes Are So DifficultWorking with children Make Your Own Ball Mill Stand
Description
Pictures of a ball mill rack that you can make yourself
Article
No industrial plant that mixes its own raw glazes would be without a ball mill. Yet potters lack them for a couple of reasons: Expense and awareness.
A ball mill is a porcelain jar a little more than half filled with porcelain balls (they can also be alumina or natural stones). Glaze is poured in, a lid secured, and it is rotated on a motorized rack (often for hours). The tumbling of the balls within grinds particles smaller and smaller. The creamier glaze applies better, has more stable viscosity, fires more consistently and cleaner with less specks and imperfections (eg. pinholes and blisters), and melts better. Ball mills also enable you to employ native materials.
Jar: Jars need to be heavy and strong. They are expensive, a 1 gallon jar typically costs about $100 US and weighs 15+ pounds. These jars are not easy to make. They must have a water tight lid. A jar must be a true cylinder or it won't rotate without hopping in the rack. They are not glazed on the inside. They are best made by casting a low shrinkage porcelain (it would be extremely difficult to dry and fire a thick thrown perfect cylinder shape made from a plastic porcelain). Typically small jars have a range of ball diameters from 1-4 cm. The pebbles cost about $6 US per pound and you need about 10+ lbs for a 1 gallon jar.
Rack: A rack (or stand) costs $700-1300 US. However you can build your own for much less.
Front and Back View
Unit weighs about 50 pounds. The lower assembly is welded from angle iron, the upper from 1/8" flat steel.
Motor
One rod is longer and extends out the other side of the bearing for the large pulley to mount on. It is driven by a 1/4 hp 1725 rpm electric furnace motor (this type of motor is mass-produced and inexpensive). The motor does run quite warm.
Pulleys & Rollers
The pulley ratio is about 5.5:1. The large is a self locking mount type. The rotating rods are 1" cold roll. Hydraulic hose with slightly less than 1" inside diameter has been pulled over the rod to grip the jar and make it run smoothly. Apply grease to the rod if the hose is difficult to pull on.
Casters
Use a caster wheel welded sideways at both ends to keep the rotating jar on center (the jar needs an unobstructed shoulder to ride against these casters).
Bearings
Four pillow block bearings hold 1" cold roll steel rods in place. The rods are far enough apart so that the shoulder of the jar runs low enough to contact the caster wheels.
Legs and Feet
Thread bolts into the feet as shown so the rack can be leveled and to prevent it from rocking on the floor.
General Notes
- You can use a vertical-sided plastic jar in a pinch, the grinding action between the jar walls and balls is lost but the balls will still crush the particles between them if you mill for longer periods. Wine making carbuoys are good also since they are very straight cylinders that will roll without hopping in the stand.
- The jar must be cylindrically true or it will rock and hop while turning.
- Fill the jar 55% with balls.
- The jar should not turn too quickly (about 30 RPM).
Related Information
Ball mill jar and rack made by @andygravesstructures
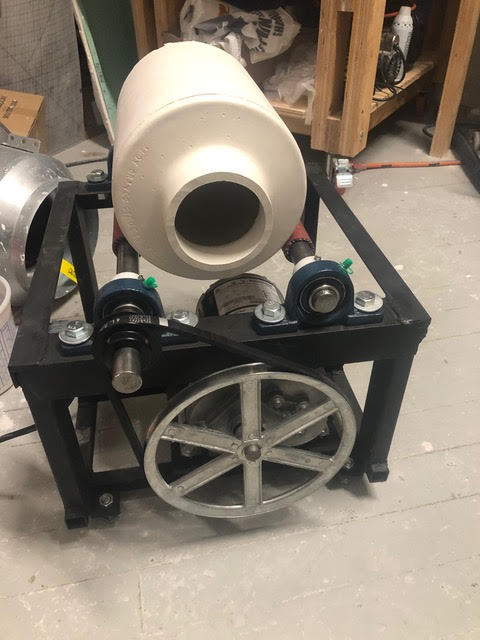
This picture has its own page with more detail, click here to see it.
Links