Notes
Silicon Nitride (Si3N4) is a non oxide man-made ceramic material sythesized by the nitridation of silicon in N2 atmosphere furnaces (other methods are also used). Like other high tech materials, recent advances in super fine powder processing and controlled atmosphere kilns have fostered a commercial renaissance in the manufacture and use of this long known but little used material.
Silicon nitride components are electrical insulators; resist wetting by non-ferrous metal melts; can withstand corrosive and high wear environments, high mechanical stresses and thermal shock. Most important, these properties are maintained at high temperatures. Si3N4 is thus used to make cutting tools, bearings, engine and turbocharger parts. Manufactures are seeking ways to reduce powder processing costs to speed adoption of this remarkable material.
Silicon nitride exists at room temperature in three stable forms: amorphous; and crystalline alpha and beta. The beta is stable at high temperatures and is formed during sintering of the alpha (parts are normally fabricated from alpha powder and sintered to beta). During the transformation a more elongated and fibrous structure evolves producing a much tougher matrix. This fibrous microstructure is a primary reason for the use of silicon nitride and the study of how to optimize and control it has spawned an industry.
The control of many complex factors involving material purity and particle size distribution, forming, and firing interplay to produce and reproduce the desired microstructure. Firing, for example, is normally done in periodic kilns where it is possible to contain vacuum, tightly control atmosphere, and apply pressure. Particles of silicon nitride in the fired matrix can be bound together by the addition of a material that will form a glassy phase with the silica layer on the silicon nitride particles (sintering aids include magnesia, yttria, alumina). This method also enables rearrangement and densification during firing. Alternatively, a lower strength but higher density matrix can be made by the introduction of nitrogen during sintering to bond silicon nitride particles (Reaction Bonded Silicon Nitride or RBSN). A variation on this is GPS (Gas Pressure Sintering) where material is burned to closed porosity and then nitrogen pressure applied to densify it fully. Hot Isostatic Pressing (HIP) is yet another process used; it minimizes the need for additives and maximizes high temperature performance of the part (however equipment and fuel costs are high).
Silicon nitride parts can be formed in many ways:
Casting: Powders with large particle size distributions work well in slip processes, those with narrow distributions give better mechanical strength. Silicon nitride powders can be dispersed in water using common polyacrylate deflocculants. The mechanics of deflocculation and the casting process are akin to using standard clay body slips. Binders can be added to slurries to increase green strength.
Pressing: For pressing the material must be granulated, binder added and moisture tuned (3-5% is common) to obtain the needed flow and hardening characteristics (freeze spraying rather than spray drying is the preferred granulation method since it avoids migration of the binder).
Tape casting: A binder/plasticizer must be used in adequate amount to give the necessary lamination and flow properties.
Injection molding: Used to make parts of complex shape. It is done by mixing the silicon nitride with a high proportion of polymer (special care must be taken to remove it using an appropriate firing schedule).
Consolidation forming: It uses Gel Casting and Direct Coagulation Casting. These require high solids content in the slip and silicon nitride grades with wide particle size distribution.
By Tony Hansen Follow me on
 | 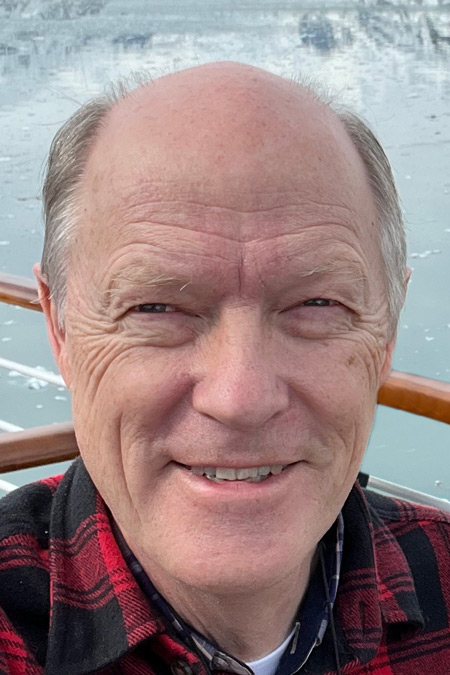 |
Got a Question?
Buy me a coffee and we can talk 
https://digitalfire.com, All Rights Reserved
Privacy Policy